Chopping Action | ||||
---|---|---|---|---|
Vaughan's patented chopping action significantly reduces downtime by not only eliminating clogging problems, but also reducing downstream issues with solids. The built-in chopping design also eliminates the need for a grinder or comminutor to condition solids prior to pumping. The elimination of clogging issues means less manpower wasted unclogging pumps. All Vaughan chopper pumps are available with a written non-clog guarantee, which is your assurance of clog-free operation. |
||||
![]() |
![]() |
![]() |
||
From Rags to Riches: Chopper Pump Gets It Done | Vaughan Centrifugal Chopper Pump In Action | The Lift Station Solution |
ABOUT VAUGHAN COMPANY
Vaughan Company has a long history of innovation and quality. Jim Vaughan, the founder of Vaughan Company, invented the world's first chopper pump in 1960. The business started in the garage of Jim's gas station in Elma, Washington. Jim repaired the local dairymen's manure pumps, which experienced constant maintenance problems caused by clogging on bedding and twine. After spending many a wasted hour repairing pumps, Jim developed a unique design that effectively became the original chopper pump. Immediately, Jim realized he had invented something worthy of a patent. |
In 1961, Vaughan Company purchased a 5,000 square foot building located in Montesano, Washington, This facility was previously used by the Schafer Brothers Logging Company as an engine repair facility for the railroad. Vaughan Company's current facility still incorporates the original building, but with over 35,000 square feet of additional manufacturing space. |
In 1964, Vaughan Company's first patent was issued. Since then, over 40 worldwide patents have been issued or are pending. New design developments have almost exclusively centered on product improvements in efficiency and reliability in the most severe environments.
Improvements in the late 1970's included the development of a seal-and-bearing system for vertical wet well pumps to eliminate sleeve and grease packed bearings. In the 1980's, Vaughan developed the "LCC Series" of higher efficiency 3" through 6" chopper pumps. These designs were further refined with the "HP Series" and also expanded to include 8" through 12" pumps in the 1990's. The "E-Series" chopper pumps were introduced in early 2000, and included further improvements in efficiency, and back pull-out design was introduced. |
Stepping into the 21st Century, Vaughan continues this pursuit of dependability using modern technology. In-house 3-dimensional computer solid modeling design allows Vaughan to create exacting fits and precision castings for all components. Computational Fluid Dynamics (CFD) analysis allows Vaughan to look closely at flow patterns and velocities within the pump, and develop premium efficiency design upgrades. Computer Numerically Controlled (CNC) automated machining creates exacting parts repetition and dependable fits with every pump.
Building a legend does take time. Dependably chopping and pumping heavy solids doesn't happen overnight. It takes years of product development and improvement, and years of proven field experience to earn the title of "Legend". |
Click Here To Download:
•Chopper Pumps Product Catalog
•Brochure: Chopper Pumps
•Brochure: Ro2Mix Process Mixing System
•Rotamix Process Mixing System Brochure
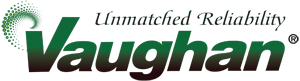
CONTACT INFORMATION
Vaughan Company
364 Monte Elma Road
Montesano, WA 98563
UNITED STATES
Phone: 360-249-4042 x 728
Fax: 360-249-6155
Contact: Josh Neils
CASE STUDIES
-
Fairfield-Suisun Sewer District (FSSD) in California installed a Vaughan Rotamix hydraulic mixing system next to an identical anaerobic digester with a 7-year-old gas mixing system.
-
This project provides an unusual "before-and-after" comparison of how a high-solids loaded digester system with a Rotamix mixing system performed before and after the Foambuster was installed.
-
During 2017’s Hurricane Harvey, the wettest tropical storm on record in the United States, over 52 inches of rain fell in the Houston area. The Vaughan pumps ran continuously for 72 hours with no plugging incidents and no problems while pumping over 2.5 million gallons of unscreened sewage through the lift station. It never flooded and none of the 150 homes served by this lift station experienced sewer back-ups.
-
The use of Vaughan's self-priming chopper pump and nozzles upstream of the influent screens improves plant efficiency and greatly increases the amount of cogenerated electricity from digester gas.
-
The Independence Hill Conservancy District's Taney Lift Station was having continuous problems with wipes, swiffers, and plastics deposited in the incoming lines, which then broke loose in storms and overwhelmed the old non-clog pumps.
-
When the Otay River Pump Station had a floating blanket of grease problem, they turned to the Vaughan Chopper Pump to help eliminate it — while also being a cost-effective solution.
-
Replacing mechanical seals twice per year was difficult and expensive for Chester, IL, but a more serious problem occurred when the seals failed with the Mississippi River at flood stage and the sealed lift station underwater.
-
The main lift station serving the waste water treatment plant in Morgan’s Point, Texas, continually experienced problems with its three standard non-clog pumps. The pumps frequently clogged when rainfall totals reached or exceeded 2 inches. Shop rags, pieces of 2 x 4 lumber, plastic bottles, gloves, and wet wipes all commonly clogged the pumps when the standard demand increased. Pump removal, unplugging, and recurring repairs were required, but the service company was not always available for immediate assistance, causing problems for residents serviced by this lift station.
-
Vaughan Co. provided a 50 HP, 1750-RPM model PE4P6CS-118 vertical pedestal chopper pump for the Carnelian Bay Pump Station to replace an existing pedestal pump, which was having difficulty with ragging.
-
Disposable, throw-away products are making raw sewage pumping tougher than ever. The Jefferson Street Pump Station at the City of Centralia, WA had a problem demanding a cost-effective solution.
FEATURED ARTICLES
-
Vaughan Company introduces its line of Self Priming Chopper Pumps; ideally suited for lift stations, scum wells, portable cleanout, or any retrofits of clogging pumps.
-
The Vaughan Rotamix® mixing system for the blend tank at the Salmon Creek Wastewater Treatment Plant, Vancouver, WA, should have had plenty of mixing flow for stirring up the sludge considering the relatively small size of this tank. Rotamix® is a hydraulic jet mixing system with floor-mounted nozzles powered by a Vaughan Chopper Pump. By Vaughan Company
-
Chopper pumps utilize a chopping action between the impeller and the suction plate to break down solids that pass through the pump into smaller pieces. Vaughan Company, an established pump manufacturer in Washington, U.S.A., designs and manufactures a line of centrifugal chopper pumps.
-
If you go looking for a particular sewage treatment plant in Cincinnati, Ohio, the first thing you'll notice is ... you might not notice it at all. In fact, when following perfectly clear directions to the facility, you might still drive right by it, dismissing it as just another office building. It doesn't register as a treatment plant.
-
Vaughan Co. provided a 50 HP, 1750-RPM model PE4P6CS-118 vertical pedestal chopper pump for the Carnelian Bay Pump Station to replace an existing pedestal pump, which was having difficulty with ragging.
-
The chopper pump is a centrifugal pump that utilizes a chopping action between the impeller and suction plate. These pumps were originally designed in the 1960s for use in the local dairy industry to transport manure to and from storage tanks.
-
Fairfield-Suisun Sewer District (FSSD) in California installed a Vaughan Rotamix hydraulic mixing system next to an identical anaerobic digester with a 7-year-old gas mixing system.