Mixed Up About TWAS?
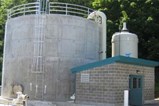
The Vaughan Rotamix® mixing system for the blend tank at the Salmon Creek Wastewater Treatment Plant, Vancouver, WA, should have had plenty of mixing flow for stirring up the sludge considering the relatively small size of this tank. Rotamix® is a hydraulic jet mixing system with floor-mounted nozzles powered by a Vaughan Chopper Pump. The Rotamix system replaced a troublesome propeller mixing system in this tank. The blend tank is used to evenly mix primary and other sludges before they are pumped into the primary anaerobic digester. And yet the treatment plant was calling to report that the mixing system provided was not working to their satisfaction. They were seeing no upper surface mixing once the tank level got higher than about 6-8 ft. in this 23' dia. x 23' high, 70,000 gallon cylindrical tank.
While the system worked "like a Jacuzzi" when mixing sludges that flowed similar to water, investigation by several Vaughan and consulting engineers and Vaughan's process specialist revealed two primary problems: (1) the polymer thickened waste activated sludge (TWAS) going into this tank was much more viscous than anticipated, and (2) TWAS, which floats, was being added through a standpipe located above the upper surface of the sludge in the tank, leaving the TWAS unmixed at the top of the tank.
To find solutions to this dilemma Vaughan Co, the mixing system supplier and an experienced user of ANSYS CFX, modeled the tank and mixing system using a fluid model developed from sludge rheology data provided by a treatment plant in England. Vaughan Co. was uniquely prepared for this challenge, having modeled in excess of 700 large tank mixing systems using CFX, a computational fluid dynamics (CFD) computer program that simulates complex fluid flow. Many of these systems have been modeled with non-Newtonian fluids, such as sewage sludge. Within a few weeks eight different trials had been run showing that the system mixing velocity could be doubled by using the same pump, motor and mixing flow but by changing: (1) the number of mixing nozzles from two to four, (2) rearranging the nozzle angles to spread out and better distribute the momentum around the tank, and (3) lowering the sludge standpipe so that TWAS was dumped into the tank as close as possible to the nozzles.
Get unlimited access to:
Enter your credentials below to log in. Not yet a member of Water Online? Subscribe today.