Siemens Industry Inc. is a global technology powerhouse that has stood for engineering excellence, innovation, quality, reliability and internationality for more than 165 years.
As one of the world’s leaders in industry automation and an experienced provider of integrated technologies, we offer products and systems tailored to the requirements of the water and wastewater industry.
The Process Industries and Drives Division can support you in continuously improving the reliability, safety, and efficiency of your products, processes and plants. We can thus help you measurably increase your productivity and improve your time-to-market – with innovative, integrated technology across the entire lifecycle.
Whether your role is engineering, operations, plant maintenance, or even plant management, we offer tailored information to fit your needs. Learn from our vast experience about up-and-coming trends in industry standards as well as innovative technologies such as web-based process control, digitalization, integration of smart instrumentation, remote monitoring and support, and more. Walk through our showcase of process measurement and control solutions and use the pop-up boxes to better understand the available choices. Let your fingers do the walking as you mine down to the information that‘s most important to you.
Take a virtual tour today: usa.siemens.com/solutionscenter
![]() |
![]() |
![]() |
||
The Cost Of Water: Leak Detection, Economy Pumping And Dosing |
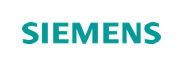
CONTACT INFORMATION
Siemens Process Instrumentation
2060 Detwiler Road, Suite 111
Harleysville, PA 19438
UNITED STATES
Phone: 800-365-8766
Fax: 972-522-4503
Contact: Sales
FEATURED ARTICLES
-
Discover how using ultrasonic technology allows level and pump controllers to progress in ways that enhance both accuracy and usability — rather than remaining static.
-
Join us for an insightful 15-minute session on the transformative role of digital technology in addressing non-revenue water. We will discuss how utilities can utilize data from sensors and hydraulic models to analyze water loss effectively and implement targeted strategies. Discover how artificial intelligence, software, and communication technologies are enabling utilities to identify and reduce NRW water loss at unprecedented costs.
-
Robust position detection is an important feature for valves and actuators. Especially when it comes to vibration, explosion protection and SIL applications across all industries like e.g. chemical and petrochemical industry.
-
Handling the heavy lifting in industrial monitoring, SITRANS IQ Guard adds diagnostics, verification and more to a host of Siemens level solutions—saving companies time and money. By transforming data into actionable insights, levelling up with SITRANS IQ Guard lets operators focus on strategy and decisions—not troubleshooting.
-
In today’s economic climate, finding cost-saving opportunities has become crucial for the survival of companies across various sectors, including water and wastewater management. Inefficiencies in processes or measurement equipment can lead to significant resource and revenue losses.
-
Siemens offers a comprehensive range of power supplies known for their reliability and efficiency, particularly the SITOP series, which is designed to handle critical network conditions and provide stable power across multiple voltage levels. These power supplies are integral to numerous industrial applications, ensuring seamless automation and energy management.
-
SITRANS FMT020 is the new state-of-the-art transmitter in our electromagnetic flow meter range, that will include backward compatibility with existing sensors.
-
Siemens has evolved its industry-leading solutions to include control for 80 GHz radar sensors or ultrasonic transducers.
-
Read about how Welsh Water sought innovative solutions, exploring clamp-on technology for accurate sewage flow measurement.
-
Siemens’ extensive portfolio includes various flow measurement technologies, such as Coriolis, clamp-on ultrasonic, vortex, and differential pressure meters, catering to a wide range of industrial needs.
-
Our top 10 OT cybersecurity questions to start asking today will help provide insight to the state of cybersecurity at your facility and leave you ready to tackle any challenges.
-
Now more than ever, it is crucial to be proactive, and protect your military installations and industrial sites with a fast and reliable technology: SIBERprotect.
-
This documentation is intended to help system integrators to setup a water plant more securely.
-
It’s never been more important to have a strong industrial network as the backbone of your operation to make sure your data gets where it needs to go on time, every time.
-
To avoid damages and downtime from cyberthreats, it’s important to implement a holistic approach addressing the
primary components of a security strategy: people, process and technology. -
This session will look at the example of a customer who thought they were having performance problems with their 10 year old flowmeter, what they discovered when they took the meter out of the pipeline, and how the upgrade to a transmitter with today’s built in features got them right back in business, confident that they could detect issues in the future before they impacted their facility’s performance.
-
The water and wastewater industry faces increasing cyber threats, highlighting the need for integrated IT security solutions. Siemens offers industrial security products and services to protect processes and plants from cyber threats.
-
SIWA Meter Data Management optimizes processes for water utilities, reduces non-revenue water, and ensures accurate billing. It helps detect leaks and anomalies in meter data, and provides valuable insights for maintenance and replacement programs.
-
Siemens' SIWA Leak Finder is a water leak detection solution that combines artificial intelligence and hydraulic modeling to reduce non-revenue water by up to 50%. It helps utilities save money, resources, and reduce environmental impact.
-
In this webinar learn lessons on delivering value from digital solutions and AI from groundbreaking advancements in automotive, oil and gas and what they can mean for water.
-
Siemens USA is pleased to announce that we have released our fully upgraded and expanded SITRANS FC Coriolis Mass Flowmeter portfolio. With this release, we have significantly enhanced our offering and capabilities.
-
Join us as we discuss the mechanism behind water hammer, its causes, and ways to prevent it from happening in the first place.
-
Discover why Siemens is your one-stop-shop for process automation, instrumentation, analytics, and weighing technology.
-
There has been no shortage of studies, discussions and debates surrounding the concept of energy efficiency over the past 40 years. Scientific studies suggest a relationship between greenhouse gas emissions and global climate change, strengthening the belief that human activity was harming the environment.
-
You can't manage what you don't measure. Learn how you can take energy efficiency to the next level.
-
Explore how utilities can deal with non-revenue water, or water that has been produced and is lost before it reaches the customer.
-
A range of devices are required to cost-effectively manage the lifecycle of produced water. Operators often face the question of which process instrumentation is the right fit given the unique requirements of their application.
-
The following article highlights four key advances in Coriolis flow measurement’s journey from the 1970s to today.
-
Easy, fast, and reliable valve control is essential to the smooth and reliable operation of your process.
-
Liquid, slurry, or solids measurements? Dirty applications? These maintenance-free sensors deliver the reliable performance you need, no matter what the environment.
-
Discover a best-in-class solution for straightforward flow monitoring of liquid processes in number of industries, including water and wastewater, HVAC, power and chemical.
-
Learn how a municipal water treatment department reduced annual maintenance costs by $265,000, while forecasting an ultimate savings of up to $3 million in yearly non-revenue water losses.
-
Learn about an easy-to-install system that works in conjunction with a variety of heavy duty motion sensing probes.
-
With millions of liters of water treated, accuracy and reliability are a necessity for a municipal water system. Learn about the instruments that they use to meet their needs.
-
A municipal water district had questioned the accuracy of their water meter readings and, after testing, they found that the billing amounts were too low. Discover the solution that they chose to provide reliable flow rate measurement.
-
Learn about a municipal wastewater treatment facility located in Louisiana that was having problems with its clamp-on ultrasonic flow meter, and how the issue was resolved.
-
Explore some of the most common beliefs currently being sold about radar in the environmental market.
-
A county water authority in the Northeast U.S. supplies over 40 million gallons per day to its 340,000 residential customers. In this case study, learn why they chose Siemens pressure transmitters.
-
Learn why the accuracy of the Coriolis sensors is better than any other insitu measurement technology.
-
This article will focus on the pump control functionality of advanced level controllers and how they can help to optimize your process.
-
In municipalities, approximately 6 billion gallons of water are lost to leaks every day. In this article, discover a solution to water loss and excess energy costs.
-
Siemens proudly announces its expanded support of The Water Tower by becoming a sustaining partner.
-
When it comes to project execution, having quick access to equipment can make or break your success.
-
The term Digitalization is thrown around all the time in today’s work environment. With people still working remotely, reduced maintenance and support budgets and the ever-present pressure to improve performance and reduce downtime, digitalization offers some real advantages. However, with these advantages comes concerns. Concerns about cloud security, susceptibility of networks to outside access and making sure only the proper people see the specific information they should. These are key questions that are being asked and deserve to be answered.
-
Water hammer, which can occur in just about any pumping system and even steam systems, can lead to pipe breakage, equipment damage or even total system failure. Addressing water hammer at the source is the savviest and most cost-effective way to handle the issue.
-
Any process plant constantly generates a high volume of status data. Today, this data can be extracted from the plant, stored, analyzed, and prepared to meet operator needs and lower marginal costs.
-
Process automation is the eyes, ears and heart of every plant: it measures, analyzes, regulates and controls industrial processes to increase efficiency and improve product quality – helping you stay competitive and profitable despite ever-increasing demands.
-
Fully featured, advanced pressure transmitters require competitive lead times to go with them. Siemens’ North comprehensive local stock means that we have the right transmitters for you, whenever you’re feeling the pressure.
-
After years of relying on an inflexible tracking process, A.P. Nonweiler introduced cloud-based remote monitoring technology to increase inventory transparency, save valuable man-hours, and minimize the risk of costly shutdowns.
-
Level controllers have evolved to meet today’s environmental challenges and industry demands. Learn how they support improved process management and, ultimately, a better bottom line.
-
Updated with new interactive features, videos, customer stories, and more, the Siemens Virtual Process Automation Solutions Center allows you to walk through the world of process measurement and control solutions – without ever having to move your feet. Hear directly from our experts about up-and-coming trends in industry standards as well as innovative technologies such as web-based process control, digitalization, integration of smart instrumentation, remote monitoring support, and more. Navigate around the room and click on the pop-up boxes to focus on the information that’s most important to you.
-
The SITRANS FS290 is a portable ultrasonic flow meter system for remote monitoring of volumetric flow in pipes. The system is made up of the SITRANS FST090 battery-operated transmitter and SITRANS FSS220 clamp-on transducers. The transducers are installed quickly and easily on the outside of a pipe – without any process interruptions or plant downtime.
-
Manufacturers around the world are being forced to do more with less, as they grapple with finite resources and numerous challenges. The chemical process industries (CPI) in particular are facing challenges as they look to increase productivity. Digitalization and automation are game changers that can help to overcome obstacles, but they come with their own set of challenges.
-
There are many reasons to verify the performance of your SITRANS FM electromagnetic flow meter. Whether you need to ensure that the meter’s accuracy complies with local agency requirements, provide a customer with a certificate of verification for billing purposes, or simply perform some troubleshooting, the SITRANS FM magmeter family provides options for both internal verification or independently certified external verification.
-
Siemens Process Instrumentation brings you innovative measurement solutions to increase plant efficiency and enhance product quality, including flow, temperature, pressure, level, weighing, and valve positioning. And we understand that in the process industry, every second counts – which is why we offer world-class engineering, testing, and production directly from our 183,000 ft2 state-of-the-art manufacturing facility in North America. Your production doesn’t stop, so why would we? Siemens delivers the instruments you need and the reliability you depend on, with same-day shipping and service available 24 hours a day, 365 days a year.
-
Even as cyber threats increase in scale and frequency to critical infrastructure sectors, the water industry shows a varied level of preparedness from one utility to the next. Implementing an effective cybersecurity program is both necessary and achievable. We've gathered industry leaders and technology experts to examine the current state of cybersecurity in the water sector and share practical advice on securing your facility against threats.
-
There’s a lot to be considered in the price tag of an ultrasonic instrument. Derek Moore from Siemens explains how the historical way of thinking only of capital costs needs to change to the more holistic approach of total expenditures.
-
The addition of the Siemens SITRANS store IQ hardware solution and app allowed Decatur immediate access to flow rate, totalizer, and head measurement on all their devices.
-
The Saalfeld-Rudolfstadt Association in Germany must rely on cutting-edge technologies that optimize flow measurement in order to allow for smooth processes and supply 82,000 inhabitants with clean drinking water.
-
When it comes to level instrumentation, one technology definitely does not fit all. Assuming you can use the same level device to meet every measurement need is unlikely to yield optimal results for your processes – or your bottom line.