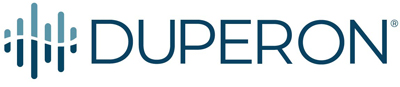
ABOUT DUPERON
Duperon is the leader in simple, adaptive screening technologies and provides solutions for coarse screening, fine screening, low flow screening, ultra screening, washing compacting and conveying.
We continually look to our customers to measure our own performance, and we are committed to continue to introduce products that are simple, adaptive solutions for preliminary treatment and management of water and water resources. We don’t want to simply meet expectations or deliver a product – we seek to truly excel in service and responsiveness that goes beyond a customers’ needs and provides solutions for their problems, today and in the future. Simply put, we want to WOW our customers.
We serve customers, groups, and associations that share the company’s commitment to the global goal of making a difference: for people, for water, for the planet. Duperon technologies are designed and manufactured in Saginaw, Michigan and installed in North America and internationally.
CONTACT INFORMATION
Duperon
1200 Leon Scott Court
Saginaw, MI 48601
UNITED STATES
Phone: 800.383.8479
Contact: Sales
FEATURED CONTENT
-
Adaptable bar screens can automatically adjust their raking speed and screen openings based on flow rates, to take advantage of the finest screening possible in any flow condition.
-
How close to the source of problematic clogging materials a debris handling solution is installed can be just as important as how efficiently that solution neutralizes them. Here are several ways to evaluate each of those variables and choose the best option.
-
Duperon today announces the commercial availability of the Duperon Dual Auger System (DAS), a solution to pump clogging caused by flushable wipes and other pump-fouling debris.
-
Of all the challenges wastewater treatment plants (WWTPs) face, screening debris from the flow at the headworks is one of the first encountered. Until recently, that has involved choosing one screen size to accommodate both average and peak flows or installing two different screen sizes. Water Online spoke with Duperon Product Manager Bryce Funchion to discuss the possibilities of a new way to get the best of both worlds.
-
With all the potential debris running through wastewater collection systems — including higher concentrations of “flushable” wipes than ever — the debate over chopping them to bits, or not, has become a fundamental question for wastewater utilities. Now, new perspectives and new mechanisms are giving wastewater treatment plant (WWTP) operators new opportunities for cutting the wipes problem down to size.
-
Flushable wipes are wreaking havoc in collection systems and treatment plants around the globe. While this is not a new issue to those in our industry, COVID-19 has made it a mainstream topic as more households consume disinfecting and flushable wipes. The improper disposal of these down the toilet can have negative impacts on the operating cost and efficiency of an entire collection system and treatment train. Here is how nipping the problem at its source can pay dividends throughout the process.
-
Depending on the age and design of wastewater infrastructure, it is easy for screening performance at the headworks of wastewater treatment plants (WWTPs) to get caught between a rock and a hard place. With so many challenges, what can be done to reduce the high risks of performance inefficiency, costly maintenance, or outright equipment failure? Fortunately, next-generation bar screen designs are poised to address these issues.
-
Some of the more challenging problems facing sewer systems and wastewater treatment plants (WWTPs) have less to do with wastewater and more to do with debris that has no business being there in the first place. Water Online spoke with Duperon mechanical engineer Steve Dill to learn about more resilient approaches to minimizing costly pump jams by eliminating debris closer to its source rather than just chopping it down to size.
-
Duperon Corporation, leader in innovative preliminary liquids/solids separation systems, announces that two FlexRake FRHD automated bar screens installed at the Mud Lake Water Users, Inc. (MLWU) irrigation company in Eastern Idaho are successfully protecting MLWU’s 160,000-gallon-per-minute pumps from tumbleweeds and other debris.
-
The West Bay County WWTP, rated for 10 MGD and seeing an average flow of 4.5-6 MGD; prior to the installation of the Duperon® Washer Compactor, the plant collected approximately 20 yards of debris each week.
-
The Roaring Fork Water & Sanitation District WWTP receives residential activated sludge at an ultimate site capacity of 1 MGD. Prior to the 2009 installation of the Duperon FlexRake Low Flow, the plant had operated with a manually-raked bar screen.
-
When Hurricanes Katrina and Rita struck the Gulf Coast in 2005, the impact was immediate and devastating.
-
In 1993, the Duperon® FlexRake® entered the market as the first multi-rake wastewater screen to operate without a lower sprocket, bearing or track. Designed by Duperon Corporation founder Terry Duperon, the patented equipment reflected his belief that mechanics should operate as simply as possible. The result was a mechanically-cleaned bar screen that consisted of just three main components — screen, raking device and drivehead. Despite its simplicity, the unit quickly proved to be far more reliable than other, more complicated designs. Paired with the industry’s first five-year warranty in wastewater, the Duperon® FlexRake® soon became a benchmark for low maintenance and ease of operation.
-
Since the beginning, Duperon has collaborated with customers to provide customized solutions for site-specific applications. Our most recent development to follow in this tradition transports debris up to 40 feet directly from the discharge of the washer compactor.