With a heritage that extends back to 1919, Kaeser Compressors is an industry leader in industrial compressed air equipment, including rotary lobe and rotary screw blower packages, rotary screw compressors, vacuum pumps, portable diesel screw compressors, air treatment components and other system accessories. Wastewater treatment plants across the country rely on us for air system solutions that are engineered for long life and continuous energy savings. Our products represent continuing advances in innovation, technology and performance. Kaeser’s built for a lifetime™ quality coupled with our commitment to energy efficiency provide our customers with the lowest life-cycle costs possible.
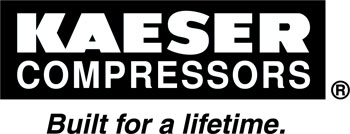
CONTACT INFORMATION
Kaeser Compressors, Inc.
511 Sigma Drive
Fredericksburg, VA 22408
UNITED STATES
Phone: 800-981-6888
Fax: 540-898-5500
FEATURED CONTENT
-
Kaeser Compressors, Inc., the US headquarters of global compressor manufacturer Kaeser Kompressoren, SE, is expanding their facility in the Fredericksburg, Virginia area.
-
Join us as we dive into current blower technologies available and examine how these key factors can shape your decision when selecting the right blower for your project.
-
In this paper, we’ll discuss how many companies are losing thousands of dollars each year to compressed air system leaks. We will address where leaks commonly occur, leak detection methods, and practical advice for an audit and repair plan.
-
In this white paper, we will drill down into which technology has particularly proven itself in terms of energy efficiency in the water industry.
-
The objective of this paper is to define the five steps required in a compressed air assessment. We will use a real-world example with system information from a magnetic materials manufacturer to clearly illustrate each step.
-
Welcome to a world where innovation meets a tradition of superior quality–where KAESER delivers products and an experience that raises the bar for what you expect from blower solutions.
-
Understanding the factors that contribute to a blower's life cycle cost can help you select a blower that delivers long-term savings and reliability.
-
This series explores crucial questions surrounding condensate management. In the first part, we examine where condensate comes from and what it contains.
-
In this segment of Virtual Water Expo, Stephen Horne from Kaeser Compressors discusses the significance of selecting the right blower technology for wastewater treatment.
-
Stephen Horne, Product Manager for Blowers, presents on innovative alternatives to traditional blower room design and construction.
-
In this segment from Virtual Water Expo, Stephen Horne From Kaeser Compressors presents about the impact of air flow in a blower room.
-
Kaeser rotary screw blowers leverage decades of experience in making the most energy efficient rotary screw compressors with the world-renowned Sigma Profile.
-
Kaeser has been designing and manufacturing superior industrial machinery since 1919. With nearly a century of manufacturing experience, we pride ourselves on upholding our traditions of quality and craftsmanship. Our reputation for reliability, energy efficiency, and excellent service has helped us grow into a global leader in blower and compressed air technology.
-
The overall wastewater treatment process is complex, and each step is integral to ensuring water is properly purified. Effluent ends up in the plants, containing substances that must be removed before the water can be properly cleaned and returned for use. The range of potential contaminants is almost endless, and can include food, pulp, waste, or other substances. Afterwards, the water requires further scrubbing, with the aid of bacteria. It is in this part of the process that compressed air (ideally provided by energy-efficient rotary lobe blowers) plays a vital role.
-
Learn about isentropic efficiency, why it's an important metric, and how it compares among blower types.
-
Learn how aeration blowers work and see how Kaeser's screw blowers bring wastewater treatment plants the advantages of screw blower technology with the added benefits of an integrated complete blower package.
-
This product brochure covers Kaeser’s line of CBS, DBS, EBS, FBS and HBS series rotary screw blowers. These screw blower systems feature the world-renowned Sigma Profile™ and are specifically designed for even the most demanding blower applications.
-
Variable speed control for all types of industrial equipment is readily available on the market with competitive pricing to non-variable speed controlled alternatives, including in the air compressor industry. With the advent of prescriptive rebate programs for variable speed compressors and other equipment, the demand for these types of controls has increased.
-
Can water be aesthetic? Absolutely! At any rate, the German-Swiss family business Neoperl ensures that it flows in a highly aesthetic way. Neoperl products shape the water stream, regulate the flow rate and protect water from contamination.
-
Carl Kaeser Sr. established his machine workshop in 1919. Learn the history of what made KAESER a highly successful global supplier of compressors and compressed air systems that remains true to its roots.
-
It's not always possible to install your equipment in a nice, indoor location. If you need to install your blower outdoors where it will be exposed to the elements, Kaeser offers an outdoor installation kit.
-
To accurately evaluate a blower system’s performance, an Air Demand Analysis (ADA) measures the actual flow, pressure, and power consumption over a set period. This provides a baseline that shows which units are running, when they are running, and how efficient the entire system is in terms of specific performance (kW/100 cfm).
-
Compressed air quality is mission critical in manufacturing. When determining the right air treatment components for a compressed air system, there is a great deal to keep in mind. In this paper, we discuss compressed air quality and how it impacts operating costs and production.
-
With over ten thousand air systems audits under our belt, we've seen it all and learned a few things. One of the most common problems we see is that most systems have far more capacity than needed. On average, users operate at 44% of peak capacity. It's so common, we'd say it is an epidemic, and even our own customers are not immune despite our efforts to inoculate with education. This article takes a look at some actual examples of over-sized systems and the costs that resulted. Learn how to properly plan for a compressed air system and what your options are with an existing system.
-
Kaeser has expanded its product range with the introduction of magnetic bearing turbo blowers.
Turbo blowers are used wherever pressures as high as 20 psi are needed, e.g. wastewater treatment, aerobic fermentation and flue gas desulphurization.
For flow rates up to 4700 cfm there is the 200 hp series, and the 400 hp series for flow rates up to 10,500 cfm. Both of these model ranges include three PillAerator designs. Each impeller design delivers different pressures and flow rates.
-
For many years, Kaeser has been building custom engineered solutions for our industrial compressor customers, and these are a natural fit for wastewater application. These are complete blower systems in purpose-built enclosures designed for exceptional reliability, simple maintenance, and superior energy efficiency. For new plants or expansions, eliminate costly and time consuming building design, permitting, inspection and construction. Greatly reduce onsite installation and commissioning costs. Reduces noise and ensures proper ventilation and longer life for the blowers. Can be built for any climate or weather conditions.
-
In 2019, Kaeser Compressors assumed control of the venerable line of PillAerator turbo blowers, strengthening its ability to serve the wastewater industry — or wherever else atmospheric process air is needed on a constant pressure level. Watch this video to understand what inspired the decision, as Manual Dias, Business Development Manager at Kaeser, covers the advantages that turbo blowers offer versus other types of blowers. Al Moreno, Kaeser's District Manager, then highlights the company's screw blower technology, followed by Global Product Manager Peter Werhahn, who provides the business case for investing in turbo blowers.
-
Kaeser Compressors' rotary screw blowers offer superior performance, fast installation, low noise operation, and lowest life cycle costs to help wastewater treatment plant operators and designers revolutionize their plant's aeration system.
-
Precision management of dissolved oxygen (DO) allows wastewater treatment plant operators to maintain optimal biological conditions in their activated sludge basins. However, older blowers and a lack of advanced aeration oversight can sabotage that effort while substantially wasting money.
-
Upgrading the aeration system in a wastewater operation is typically burdensome because of the design work, permits, construction, and commissioning required for a structure before a new blower system can be installed. An affordable, purpose-built blower system delivered in its own secure, weatherproof enclosure may be a viable alternative that can be commissioned sooner and at lower cost than one that requires renovations or new construction.
-
It’s common for wastewater treatment plant operators and design engineers to get comfortable with one type of blower for aeration. However, multiple blower technologies are available to consider when designing a new system. Understanding the difference between them, as well as the pros and cons of each based on the specific application, is critical to the decision-making process.
-
In municipal and industrial wastewater treatment, there has been a shift from manual to automatic process control in order to increase efficiency and improve effluent quality.
-
In 2012, the Town of Francesville in Indiana contacted Air Diffusion Systems to provide a solution for several suspended solids violations and energy efficient treatment. Air Diffusion Systems was able to provide an unique solution to correct biochemical oxygen demand (BOD) and total suspended solids (TSS) problems using Kaeser Compressors’ CB Com-paK blowers.
-
Energy is a huge portion of a wastewater treatment plant’s operating costs, with aeration blowers a significant user. System splitting with an adaptive master controller reduces electrical, maintenance, and initial investment costs.
-
Kaeser Compressors has revolutionized compressed air controls with the sigma Control2.
-
Kaeser’s custom engineered solutions are compressed air and vacuum systems built to specification for the most demanding and challenging installations. Whether in custom enclosures or modified ISO shipping containers, these complete systems are designed for exceptional reliability, simple maintenance, and superior energy efficiency no matter what the installation limitations may be. They eliminate space, weather, and accessibility constraints and can significantly reduce construction, installation, and operating costs.
-
Comparing blower performances across different manufacturers and technologies has long been a difficult task. For many years, it was all too easy to present data that, although accurate, was potentially misleading. Manufacturers were selective about what information they published as well as what conditions they chose to specify performance. The result was a numbers game the buyer frequently lost. Fortunately, the Compressed Air and Gas Institute (CAGI), in cooperation with its members, has developed a tool for a fair comparison between blowers.
-
Kaeser Com-paK blower systems offer the best combination of quality construction, reliable performance, and ease of ownership. The Com-paK design features a full scope of supply that is unmatched in the industry. Our complete package design minimizes time and money spent on engineering, procurement, documentation, and installation. Com-paK units arrive fully assembled and ready to operate.
-
Written by Kaeser’s system experts, this white paper compares rotary lobe and screw blowers, isochoric and isentropic compression, and how to properly apply these technologies for designing an energy efficient system.
-
Kaeser Compressors’ Blower System Installation Guide: Layout Considerations for a Reliable, Energy Efficient, and Safe Blower System provides essential tips for planning and installing a blower system. Written by Kaeser’s blower and engineering experts, this e-book includes installation diagrams, information on piping, ventilation, controls as well as additional resources for ongoing energy management.
-
Kaeser screw blowers use up to 35 percent less energy than conventional rotary blowers and even achieve significant energy savings compared to currently available screw blowers.
-
The next big thing is here and it’s the Industrial Internet of Things (IIoT). To understand how the IIoT applies to a wastewater treatment plant, look no further than your front yard.
-
System controls are critical to a wastewater blower system. Without them, a system with multiple blowers operating on their individual controls will run more than necessary and result in wasted energy. Maintenance costs increase and worst of all: process performance suffers.
-
As part of her tour marking the opening of this year’s Hannover Messe, German Chancellor Angela Merkel and Polish Prime Minister Beata Szydlo paid a visit to Kaeser Kompressoren’s trade show booth. Naturally, Kaeser was delighted to welcome Chancellor Merkel and Prime Minister Szydlo. For her part, the Chancellor was enthusiastic about the power of innovation demonstrated by the Coburg-based compressed air system provider.
-
Wastewater treatment plants provide a critical service to our communities. WWTP systems operate continuously and equipment must be completely reliable and sustainable. Kaeser delivers exceptional air system solutions for wastewater treatment operations that are engineered for long life and continuous energy savings.
-
When it comes to the costs of running a wastewater treatment plant, the conversation tends to begin and end with blowers. These machines are a staple in wastewater operations, gobbling up energy and running up the power bill as they function, so it’s worth taking the time to make the right investment.
-
Wastewater managers are always under pressure to reduce costs. Lowering the electric bill — which also saves precious resources — is a high priority.
-
Operators are constantly looking for ways to improve the aeration stage by revamping, replacing, or modifying the blowers and their packaging.
-
When it opened in 1846, the Danube-Main (Ludwig) Canal was an ambitious engineering project intended to put the recently founded Kingdom of Bavaria on the map as a modern industrial power.
-
A Kaeser EBS series screw blower is making wastewater treatment considerably more efficient and effective at the Goldsteig dairy factory in Cham in the Upper Palatinate region in Germany.