Troubleshooting Tips For Common Pump Performance Issues
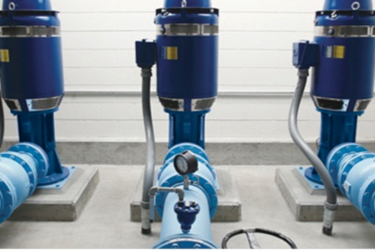
Noise, vibration, heat, and excessive maintenance/repair events are just some potential pump issues inside a water or wastewater utility. Here are some guidelines for troubleshooting pump performance and some steps to take to ensure maximum efficiency and payback from an investment in performance for clean water pumping applications — raw water feeds, treatment processes, storage, and distribution in municipal drinking water systems or effluent pumping in wastewater treatment plants.
Warning Signs Of Potential Problems
Every pump is designed to operate within a certain range of speed and volume of water moved —typically for a period of 15 to 25 years. But cause-and-effect signs of less-than-optimum installation can appear sooner than that. Look for a progression of warning signs that typically arise as deterioration increases. The more extreme the improper application, sizing, or installation of the pump, the more rapidly these warning signs may progress:
- Noise. Look for the earliest signs of pump performance problems in the form of noise, hum, or rattle that increases between inspection periods.
- Vibration. Feeling a pump during maintenance inspections — from top to bottom and side to side — can detect minor vibrations before the situation escalates. Critical pumps can even be equipped with sensors to feed vibration data to plant SCADA systems automatically.
- Heat. Whether coming from the motor housing or the pump itself, heat is another sign of friction, wear, pressure, or out-of-tolerance issues.
- Leaks. Not every drop of water indicates a problem. Pumps with packing-assembly shaft seals are designed to leak at a rate of about a drop per second. Mechanical-seal pumps should not leak at all.
- Wasted Energy Costs. The windings on a 500-HP pump demand the same amount of electricity whether that pump operates at the optimum ‘sweet spot’ of its pump curve or is throttled back way below it. (See ‘Proper Sizing’ bullet below.)
- Catastrophic Damage. If early warning signs of pump wear or misalignment are missed, the first incidence of bearing failure, shaft breakage, impeller damage, or pump casing damage should be an instant red flag.
Problem Prevention Starts With Better Planning
Whether looking to remedy problems in an existing installation or to design a new application for optimum performance, here are four focal points for optimizing pump performance and lifecycle costs:
- Pump Selection. Most pump decisions come down to the footprint space available and the volume/pressure needs of the application (Figure 1). In raw water feed applications, match bearing and shaft materials to the abrasiveness of the water composition.
- Proper Sizing. Running outside of recommended pump curve limits can result in cavitation, vibration, or excessive wear. For example, undersized pumps that never build enough pressure typically lead to premature wear or failure. Ideally, pumps should be sized to run between 70 percent and 110 percent of their optimum performance range, after calculating all losses in the system back to the pump’s discharge point (Figure 2).
Instead of installing an oversized pump in anticipation of municipal growth, size the pump to satisfy current demand while running at just 70 percent of optimum pump performance. Run it until demand reaches 110 percent of the optimum performance, and then replace it. This can be less expensive than paying elevated energy, maintenance, and wear costs for the oversized pump across the same time frame.
Be sure to recalculate total system needs and adjust pump performance if alterations to treatment plants or distribution systems cause the original pump to drift outside its recommended pump curve.
Photo courtesy of Xylem
Figure 1. Raw water pumps that encounter excessive amounts of sand and dirt can quickly exhibit noise, vibration, bearing wear, and even catastrophic shaft or impeller failure due to wear in as little as a year. Changing shafts and bearings to harder or more resilient materials — such as these self-healing rubber bearings — can resist wear and forestall mechanical breakdowns.
Graphic courtesy of Xylem
Figure 2. Each pump has a specific ‘sweet spot’ of most efficient operation within its total range of acceptable operating parameters. Pump curves are developed for each pump based on the amount of pressure or head it can generate (expressed on the vertical axis) across the range of applicable speed or volume of water moved (expressed on the horizontal axis).
- Proper Installation. Even when the proper style and size of pump are selected, improper installation can spawn a series of problems leading to inefficient operation and premature wear or failure.
- Alignment. Pumps that are not level or that have misaligned pump and motor shafts can cause bearing wear issues to compound over time.
- Impeller Settings. Improper clearance between an impeller and pump casing is a leading cause of pump damage and failure. While that spacing needs to be close in order to maximize efficient water movement, metal-to-metal contact between the impeller and casing will accelerate wear.
- Pump Base Support. Proper grouting under the baseplate of a pump — an often-misunderstood factor in pump installation — is critical to preventing vibration. The baseplate should never rest on the jacking nuts used to level it but should be firmly grouted in place to solidify the entire installation as an integrated structure.
- Pipe Support. Using pump connections to support a long length of pipe or using flange bolts to pull piping into line with the pump creates stresses that can warp a cast-iron pump casing, cause uneven bearing wear, and ultimately break the casing. Assembled or disassembled, flange connections should cause no movement of the pipe or pump.
- Cleaning/Screening. Make sure that any construction debris inside pumps or pipelines is removed before making the final connection. Debris wrapped around impellers, bearings, or seals can cause imbalance and wear. Be sure to install strainers to catch debris that can clog and damage pumps (Figure 3), especially with raw water intake pumps.
- Maintenance Scheduling. Protect the investment in a properly selected, sized, and installed pump with appropriate care. For example, raw water pumps subject to silted intake water should be inspected at least once a month. Other pumps moving filtered water out of the treatment plant can go a longer time between inspections. Adjust maintenance inspections to account for recent upstream or downstream changes in water collection, treatment, or distribution processes that might impact pump performance.
Photos courtesy of Xylem
Figure 3. Raw water intake pumps are especially susceptible to fouling from a wide variety of debris that can restrict water flow, cause immediate damage, or result in excessive wear over time. Keeping factory-provided protective screens installed as instructed can save unnecessary downtime and repair expense.
Finally, Repair Or Replacement?
Repair vs. replacement decisions typically come down to a matter of age and cost. When the cost of repair for a 10-year-old pump exceeds 50 percent of the cost of a new pump, it is probably time to consider a new, properly sized pump installation. Until then, here are several alternate strategies:
- Oversized Pumps. Using flow control valves to restrict flow is not the answer. It might be possible to improve oversized pump efficiency by equipping it with a variable frequency drive (VFD). For multistage pumps, removing one impeller might enable the pump to operate within the recommended pump curve, even though energy consumption remains the same.
- Undersized Pumps. Undersized pumps can run more effectively if system pressure demand can be lowered.
- Abrasive Applications. Existing pumps can be rejuvenated by upgrading to more abrasion-tolerant shafts, bearings, and impellers, provided that early warning signs of wear have not gone unheeded for too long.