Money Found In Puget Sound: Aeration Blower Saves $44K Annually For WWTP
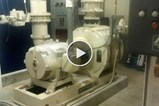
Water Online Radio case studies are a convenient way to discover water/wastewater solutions that are working for customers in the field. Hear directly from the end-users and technology providers who have successfully overcome some of today's most prevalent and problematic water challenges.
In this first installment to the monthly series, you'll learn:
- how Aerzen aeration blower efficiency is saving a Puget Sound utility an estimated $44,000 per year.
- the energy and O&M gains offered by new blower technology.
- the difference between positive displacement, turbo, and hybrid blowers.
- how to manage air demand to find your efficiency "sweet spot."
The segment features interviews with John Franz, wastewater treatment plant manager for the City of Anacortes, WA, as well as Kevin Grant, a regional sales manager for Aerzen USA.
Here's a sample of the conversation with John Franz:
Water Online Radio: John, there are a lot of organizations that you could have worked with to get more energy-efficient machinery. Why did you go with Aerzen?
John Franz: That's a really good question. At the time we started looking at this project, a very popular way at wastewater treatment plants to achieve this savings was to go with one of the new turbo blowers. The new turbo blowers are very efficient machines, and there are a number of them that have been installed and were operating successfully.
People were really quite happy with them. When we started talking to vendors about how to analyze this and how to select a piece of equipment, we came across Aerzen company, and they had a really new technology that they called the hybrid blower.
That machine, when we examined it and compared it to the turbine blowers, it was just a little bit more efficient than a turbine blower. But more important to us, it had a broader range of operation.
...and with Kevin Grant:
Water Online Radio: Kevin, Aerzen likes to say, “We deliver performance to the power of three.” Talk about that.
Kevin Grant: Traditionally, Aerzen started out being a rotary-load positive displacement blowers, also known as PD blowers, which are generally the workhorse of the industry and traditionally, the technology started back in the 1860s, but we also have the turbo blower that we've introduced into our product line, which is not a positive displacement.
It's like centrifugal technology, and it's a high-speed, high-efficiency unit. Traditionally, in this market, there's things called multi-stage centrifugal. This is a single-stage high-speed. It works off of air oil bearing, so there's no oil in the machine, and uses a permanent magnet motor and an inverter to get to speeds 30,000 to 40,000 rpm.
That's one technology. The PD is the other technology, and then, like I said, Aerzen started developing about 12 years ago a new product they call the hybrid, which was a cross between the single-stage oil-free screw compressors and a PD.
Basically, it combined the efficiency of a screw compressor, but with the economy of our PD blowers. Between the PD, the hybrid, and the turbo, that gives us three different technologies that we can approach any application or any problem. That's where the performance of three comes from.