Anti-Fouling Filtration Membranes Separate And Reclaim Oil, Grease, Emulsions From Water
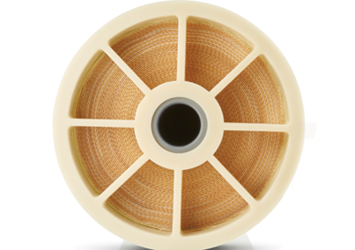
Treating problematic industrial water streams for reuse or disposal — especially those contaminated with oils, greases, or emulsified materials — can be very challenging in terms of performance efficiency and cost. Fortunately, new advanced-filtration membranes are making headway in those challenges. Here’s how industrial water-treatment professionals ranging from filtration-system designers to third-party water-treatment services to in-house wastewater-system operators are reaping the benefits.
Better Outcomes Start With Better Membranes
Filtration applications encounter challenges ranging from physical media performance, to flux rates, to improved process economics, or any of those combined. The presence of oils, greases, or emulsified materials — as encountered in oil-and-gas-production, machine-shops, industrial washdowns, etc. — only ups the ante.
For new or existing applications seeking to achieve greater throughput, removal rates, and/or recovery rates than those afforded by existing membrane-filtration systems (as well as other oil/water separation technologies), the choice of new, anti-fouling membranes offers improved performance.
One key difference of these proprietary anti-fouling membranes is in their physical composition. The composite base membranes feature 75-percent porosity, a hydrophobic polymer matrix that repels water, and a hydrophilic inorganic filler that pulls water through the membrane creating capillary forces that deliver higher flux than standard hydrophobic membranes (Figure 1). These base membranes are then treated to produce super hydrophilic membranes to further improve resistance to fouling by oils and other viscous substances.
The comparison shown below illustrates other structural differences (Figure 2). Because the composite material is a single layer rather than a cast thin layer over a larger pore size structural support, these membranes can be backwashed without concern for delamination. Backwashing allows for alternate cleaning methods that can reduce fouling and extend the lifetime of the membrane.
Photo courtesy of PPG
Figure 1. Anti-fouling membranes with combined hydrophobic/hydrophilic properties offer high-flux performance with backflush cleaning durability to extend life. This combination of features is ideally suited for filtration applications complicated by oils, greases, and various emulsified materials.
Photo courtesy of PPG
Figure 2. One key difference between anti-fouling microfiltration (A.) and ultrafiltration (B.) membranes vs. conventional polyacrylonitrile (C.) and polyvinylidene fluoride membranes (D.) is that their structure is a single layer versus an extruded thin layer over a larger pore size.
Greater Efficiency Accommodates Multiple Aspects Of Concern
The benefits of the anti-fouling membrane technologies provide clear performance enhancements and improved economics that make it well suited for a variety of applications. These include oil/grease/water separation, including reverse-osmosis (RO) pretreatment applications. Consider these advantages:
- High Flux Rates. Compared to older, conventional membrane designs, these new, anti-fouling membranes offer good separation and high flux rates (Figure 3) at similar or lower pressures for water reuse or clean-water discharge. They can also be better at recovering reusable oils and grease than other filtration options. For example, activated carbon technology can provide good filtration at high flux rates as compared to membrane filtration, but it offers no good options for oil/grease recovery and it also comes with attendant disposal costs and efforts.
- Exceptional Permeate Quality. The precise pore size distribution of this anti-fouling membrane allows for very efficient removal of total suspended solids, free oil, emulsified materials down to less than 10 ppm levels. Consistent porosity captures more of the contaminant and delivers better water quality in the permeate, even in commercial-greywater-reuse applications challenged by soap, surfactants and other debris.
- Reduced Fouling. The ability to operate membranes at lower transmembrane pressures (TMP) helps to reduce fouling in any application. Anti-fouling membranes were developed to handle more difficult-to-treat waters where other conventional membranes would foul quickly, keeping the membrane clean and extending life.
- Improved Economic Performance. Extending membrane life reduces membrane replacement costs. And high-flux performance reduces the number of elements required, reducing energy consumption and enabling a smaller system footprint that can lower capital costs.
Photo courtesy of PPG
Figure 3. Microfiltration and ultrafiltration membranes made with an anti-fouling treatment provide at least double the flux rate of conventional PVDF and PAN membranes in crossflow testing conducted at 50 psi transmembrane pressure and a feed flow of 1.5 gpm.
The Proof Is In The Performance
This white paper provides an overview of proprietary-polymer, high-flux, permeable-membrane technology. It also includes case studies of highly demanding applications. Polyalkylene-glycol recovery in a heat-treating application reduced the turbidity of the initial feed stock from the range of 110 nephelometric turbidity units (NTU) down to 0.385 NTU in the initial ultrafiltration permeate while it reduced oil and grease content from 85 ppm to less than 5 ppm. This extended the functional life of the coolant and significantly reduced disposal costs. Also, an automotive parts manufacturer significantly reduced the percentage of total suspended solids and oil and grease in its parts-washing process while slightly reducing conductivity without changing pH value, producing clean permeate water at a recovery rate of greater than 90 percent (Figure 4).
Photo courtesy of PPG
Figure 4. This photo shows how cloudy an automotive-parts-washing solution appeared at 450 NTU (left) before filtration through ultrafiltration membrane and how clear it was (right) at less than 1 NTU, following treatment.