Measuring slurry settling finally automated
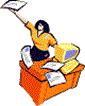
Contents
Introduction
Mudline – optical technique
Automated monitoring
Testing the system
Results
Summary
With a digital camera and specially designed software, Mudline monitors and automatically locates solids settling in mineral slurries in real time. It can provide very accurate settling measurement and has the capability of multi-cylinder and fast settling tests, which are almost impossible for manual recording. Mudline is the work of Australia's CSIRO Thermal and Fluids Engineering with the support of Rio Tinto Research and Technology Development, Melbourne.
The system is highly automated and user friendly. It is easy to use and set up. Locating test cylinders, calibrating the scales and image/data processing are all carried out automatically by the software. The results are displayed in real time as well and are recorded in a computer file for easy access for further analysis.
Replacing manual measurement as it does, it almost doesn't need to be pointed out that Mudline offers significant cost and time advantages to mining and mineral processing companies, and with more accurate slurry analysis.
Introduction
The conventional method to measure settling velocity is to fill a measuring cylinder (or jar) with slurry, mix the slurry well so that particles are completely dispersed, and then locate and measure the descent of the solid–liquid interface as a function of time. Although this method is simple and direct, it runs the risk of introducing large errors due to the possible misinterpretation of the interface and the errors which may vary from person to person.
The situation may be worse when flocculant solution is added to speed up the settling process. At higher flocculant dosage, the settling time is very short. Therefore, it is very hard to follow the movement of the interface. On the other hand, for very slow settling processes, manual reading is very tedious since settling processes sometimes last for hours or even days.
There are a number of other methods which have been used for measuring particle settling, which include, for example, X-ray radiation, ultrasound, radioactive and magnetic tracers, magnetic resonance imaging, hydrometers and pressure sensors. However, these techniques are generally expensive and complicated. Some of the techniques cannot perform online measurements. Therefore, these methods are mainly used in laboratory studies. A method called the 'conductance method' has also been developed and provides a simple technique to measure settling velocity. However, this method is limited to certain slurries and the conductivity of the slurry with different solids concentration must be known beforehand.
To overcome these difficulties and increase the efficiency and accuracy of measurement, CSIRO and Rio Tinto have developed the Mudline automated measurement system for slurry settling tests using image-processing techniques. (Return to top)
Mudline – optical technique
Mudline is based on collecting light diffused through the slurry and the use of this data by computer software designed for the task.
In the area where particles are rare, the light intensity is high, whereas for the area where the slurry is dense (i.e. particle concentration is high), the light intensity is low due to the blockage of light by the particles. Therefore, the gray-scale in the image of the slurry shows a variation from the free surface to the bottom of the cylinder.
The largest variation occurs around the solid–liquid interface. By processing the images, the interface location can be determined. The whole settling curve can be obtained by taking a series of images of the slurry during settling.
Once an image is acquired, the gray intensity for each pixel is retrieved. An edge-detection technique is applied to the image to obtain the boundary of the cylinder. The location of the solid–liquid interface is then determined using an in-house image-processing software (Mudline). Although the above-mentioned optical technique is simple, the realization of the technique in the software is not, which is probably why it is not currently available in commercial image-processing software packages.
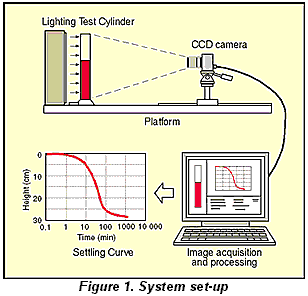
(Return to top)
Automated monitoring
The present automated monitoring system (Figure 1) consists of a charged-coupled-device (CCD) camera (Kodak ES1.0 with a resolution of 1018 x 1008 pixels) with a lens, a lighting device attached to a support platform and an IBM-compatible PC. An EPIX PIXCI-D image-acquisition board was used for capturing images during testing.
The slurry was illuminated using continuous background lighting. The top part of the cylinder (above the liquid surface) was blocked in order to reduce the sharp change of light intensity. The calibration of the physical length of a pixel for a given set-up was performed automatically before the start of the settling test. The cylinder was empty so that all the graduation marks on the cylinder surface can be visible in the image.
These evenly spaced marks showed regular scale-scale peaks in the pixel intensity distribution. By performing fast Fourier transformation on the pixel intensity distribution of the cylinder, the pixel physical length can be calculated from the results if the distance between the two adjacent marks were given. For test cylinders without graduation marks, a manual calibration method has to be used.
The images of the slurry during settling were captured by the CCD camera at small time intervals (depending on the number of points required and the total settling time). The images were processed in real time. The location of the interface and the image were displayed on the screen so that the results could be visually examined. The images can also be saved on the computer for further examination.
The time interval was small (can be less than one-tenth of a second) at the start to resolve the fast settling stage. It was increased to a maximum value of about 20–40 minutes towards the compression stage (i.e. particles compacting at the bottom). The sampling frequency at different stages was automatically adjusted. Mudline is the in-house image-processing software developed to provide a graphical user interface. The processed data together with the time were output to a text file that was later used for analysis and presentation. (Return to top)
Testing the system
A slurry of iron ore with a weight concentration of 4.5% and a flocculant solution (Ciba Magnafloc 800HP) were provided by Rio Tinto Research and Technology Development. Three measuring cylinders with capacities of 500, 1000 and 2000 mL, respectively, were used. The total settling duration varied from a few minutes to more than 24 hours. It should be noted that although three cylinders were used in the present experiments, results from only one cylinder are shown in this paper.
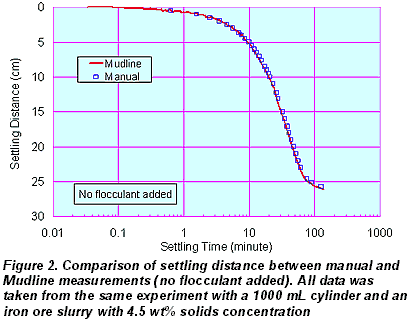
(Return to top)
Results
The automated particle settling measurement system and the edge detection technique were tested in a series of experiments with different cylinders. The slurry was also diluted (2.25%) to test the measurement. The settling rate was very small in this case and the total settling time was about 24 hours for the compression process to be completed. Since the liquid above the interface was quite clear or there were not many very fine particles suspended in the liquid, the edge of the particle-laden liquid was clearly visible.
Both the manual and automated measurements of the interface location were carried out simultaneously to the same settling test. For the manual measurements, a ruler was attached to the cylinder. Data was taken at approximately 5 mm intervals and the corresponding time was recorded using a stopwatch. The measurements from Mudline and the manual method produced similar results (Figure 2).
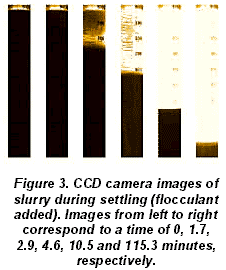
In the case of adding flocculant solution, the large particles are combined into agglomerates, whereas fine particles are usually suspended in the liquid. The large flocculants settle much faster than the fine particles. Therefore, the liquid part of the slurry during settling is normally very muddy (this part of the image is normally gray or dark due to the blockage of the backlighting) and the clarity depends on the amount of flocculant added. Although some of the regions were very dark from the beginning, the intensity showed a significant increase, which allows the interface to be detected (Figure 3)
Figure 4 shows the settling curves of the slurry with flocculant. The flocculant dosage was about 42 g/t. The agreement between the Mudline results and the manual results is reasonably good, the maximum relative error being less than about 3.5%. The difference was mainly due to the misinterpretation of the interface where the slurry was the muddiest, and therefore the interface was to some extent ambiguous. This misinterpretation may be due to both the manual and the Mudline measurements. This difference is so small that the effect on the settling rate is negligible.
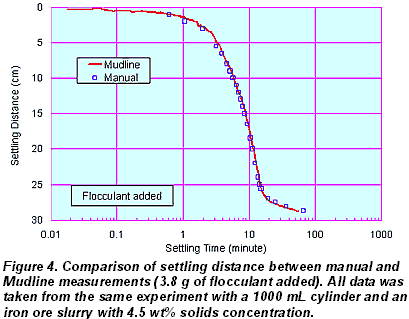
(Return to top)
Summary
The tests described above have demonstrated that Mudline is an accurate and fast system for automated slurry settling measurement. The results demonstrated that the movement of the liquid–solid interface can be monitored automatically with satisfactory accuracy. The settling curves measured by Mudline agree with those measured manually, and demonstrate that Mudline is well suited to industrial applications. (Return to top)
Acknowledgments
The financial support of Rio Tinto Research and Technology Development is gratefully acknowledged. The authors would like to thank Tony Kilpatrick and Glen Cross of CSIRO for their help in manufacturing the measurement system and carrying out the experiments.
This article is based on the paper 'An automated measurement technique for slurry settling tests' by Yonggang Zhu, Jie Wu and Ian Shepherd of CSIRO Thermal & Fluids Engineering, and Mark Coghill, Nikk Vagias and Karen Elkin of Rio Tinto Research and Technology Development, which has been accepted for publication in Minerals Engineering.
For more information contact Dr. Dilip Manuel, Business Development Manager, CSIRO Thermal & Fluids Engineering at Tel: 61 3 9252 6073;
e-mail: Dilip.manuel@dbce.csiro.au.
This article originally appeared in Innovation Online, a bi-monthly online magazine showcasing new technology, products & services impacting on Australia's built environment. For more information, visit http://www.dbce.csiro.au.
Subscribe to our free e-mail newsletter.