Mazzei Injector Company, LLC
500 Rooster Drive
Bakersfield, CA 93307 US
661-363-6500
Bakersfield, CA 93307 US
661-363-6500
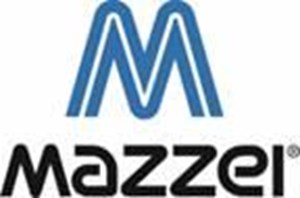
Company Overview
Mazzei, a leader in the design and manufacture of fluid mixing and contacting technologies, provides systems and components for ozone, aeration and chemical treatment for water and wastewater.