ChartWater BlueInGreen
Tyler Elm
700 W. Research Center Blvd., Suite 1207Fayetteville, AR 72701 US
479-527-6378
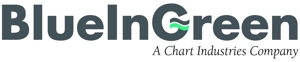
Company Overview
BlueInGreen is a gas dissolution expert that provides the most efficient method of dissolving gases in water. Delivering effective solutions for a variety of water treatment and industrial process applications, including dissolving and entraining oxygen for the biological treatment of wastewater, the remediation of pollutes surface waters, and odor control and corrosion control in collection systems; dissolving and entraining carbon dioxide to create carbonic acid on demand for pH control, remineralization, and acid replacement; and, dissolving and entraining ozone for disinfection and other oxidation of contaminants.