XR In The Water Sector: Training A Workforce That's Ready — Not Just Certified
By Dave Dwyer
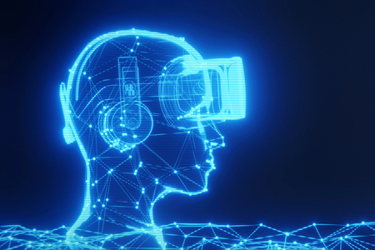
When the water stops, everything else stops. Hospitals, factories, homes — they all depend on one thing: a utility workforce that knows exactly what to do, when to do it, and how to do it under pressure. But that workforce is shrinking. The systems are aging. And the traditional ways we train? They’re not keeping up.
Water utilities are facing a perfect storm. Regulations are tightening. Equipment is breaking down. Experienced operators are retiring in waves. Meanwhile, the number of certified replacements is falling short — and fast.
The U.S. Bureau of Labor Statistics projects a 6% decline in water and wastewater treatment plant operators by 2032. The U.S. EPA reports that one-third of the current workforce is nearing retirement. In Texas, it could hit 50% in a decade. At the same time, only 36% of candidates are passing the operator licensure exam. That’s a pipeline problem — and it’s growing.
Let’s Be Honest: Binders And Ride-Alongs Aren’t Cutting It
Most utilities still rely on job shadowing, thick manuals, and occasional hands-on sessions. That might check a compliance box, but it doesn’t build confidence or capability — especially when a real emergency hits.
You don’t learn to respond to a chemical leak by flipping through a binder at 2 a.m. Watching someone do a valve shutdown once doesn’t prepare you to lead it under pressure. When experienced workers walk out the door, they take decades of muscle memory and instinct with them. What’s left behind is a crew under pressure and underprepared.
In the field, the cost of underprepared teams is real. Failed pressure tests. Slow response to chemical imbalances. Missed inspection marks. These aren’t paperwork problems — they can trigger service outages, regulatory fines, or even public health alerts. It’s not enough to check a box. Utilities need crews who can do the job — and prove it — under real pressure.
We don’t need more theory. We need training that sticks. Training that scales. Training that builds readiness.
XR Isn’t The Future. It’s The Fix.
Extended Reality (XR) is the umbrella for immersive training tech — virtual reality (VR), where crews rehearse procedures in a fully digital space, and augmented reality (AR), which overlays guidance onto the real world. XR lets utilities train without shutting down systems, tying up instructors, risking safety — or waiting for a live scenario that may never come.
This isn’t about trendy tech. It’s about performance. XR gives utility teams the repetition, realism, and reinforcement they need — in a way that traditional training simply can’t.
Train Like It’s Real — Because It Will Be
Immersive training means crews can practice complex, high-risk, or rarely performed tasks until they’ve mastered them — not just memorized them. That includes:
- Diagnosing pump and valve issues in live walk-through simulations
- Practicing confined space entry and chemical handling
- Enforcing PPE protocols and flagging hazards through visual cues
The result? Up to 75% better knowledge retention, faster response times, and fewer mistakes when it counts. That’s not hype — that’s proven. And unlike traditional drills, these scenarios are repeatable, measurable, and available on demand.
Pressure Test Your Team — Before the Pressure Hits
Imagine a backflow preventer anomaly triggers a pressure drop. It’s rare, but when it happens, there’s no time to pause. Crews need to isolate, diagnose, and resolve the issue — fast.
With XR, they’ve seen it before — and practiced it under pressure. Not once, but 10 times. There’s no panic, no guesswork — just execution. XR collapses the distance between training and doing. That’s the game-changer.
Start Where It Matters Most
XR shouldn’t be a science experiment. Start where it makes the biggest impact:
- High-risk, high-compliance procedures
- Steps that slow crews down or lead to rework
- Tasks where proficiency fades between events
You don’t need to XR everything. Focus on the tasks that carry the most risk, cost, or inconsistency when they go wrong. Build targeted modules. Test them. Track the results. Refine and scale what works — all without taking critical systems offline.
Forget flashy rollouts. XR works best when it’s precise and practical. Don’t convert entire workflows just because the demo looks slick. Start with what slows crews down, trips compliance, or drives rework. Train for those moments first. Prove the impact. Then expand. This isn’t about volume — it’s about value, one critical task at a time.
This Isn’t About Technology — It’s About Readiness
Manuals can’t prepare teams for high-stakes decisions. XR can. It builds real-world capability in a risk-free space. Supervisors can see who’s ready and who’s not — and train accordingly.
It’s faster. It’s smarter. And it works.
XR isn’t experimental anymore. Utilities, manufacturers, and defense agencies are already using immersive training to improve response times, reduce rework, and build real readiness. These aren’t test cases — they’re frontline applications where teams need to perform under pressure. XR accelerates learning, sharpens decision-making, and helps teams get it right the first time — without taking systems offline or risking safety.
Utilities Don’t Need More Talk — They Need Tools That Work
Aging infrastructure, workforce gaps, regulatory heat — these aren’t future problems. They’re here now. And they’re not slowing down.
Every delay in upskilling the workforce is a risk multiplier — for operations, compliance, and customer trust.
XR isn’t about bells and whistles. It’s about preventing the next outage, the next compliance violation, the next safety incident — before they hit the headlines.
Learn From The Sectors That Can’t Afford To Fail
Aviation, defense, energy — they’ve all adopted XR because failure isn’t an option. They didn’t wait for perfect conditions. They moved fast because readiness matters.
Water utilities face the same stakes. Large systems. Environmental risks. High visibility. XR is already solving these challenges in other sectors. It’s time to apply it here.
Train Like You Mean It — And Keep The Water Flowing
Utilities can’t afford to lose knowledge faster than they can replace it. XR bridges that gap. It accelerates onboarding, reinforces experience, and gives leaders real data about performance.
When the workforce is prepared, everything runs better. Response times drop. Mistakes are avoided. Water keeps flowing.
That’s not a vision. That’s the mission. Let’s train like it.
David (Dave) Dwyer is the Chief Operating Officer (COO) of Mass Virtual, where he leads operations and strategy to deliver transformative extended reality (XR) solutions focused on improving human performance. With extensive global experience in program management, IT, sales, and marketing, Dave’s diverse background is unified by a customer-first philosophy. Guided by the principle to “make it work,” he and the team at Mass Virtual successfully scaled the business in a hyper growth stage for three consecutive years. A passionate advocate for leadership development, he mentors students through programs at UCF and local high schools, believing in the importance of building strong leaders for the future.