WWEMA Window: The Changing Nature Of The Water Construction And Procurement Industry
By Allen Walker
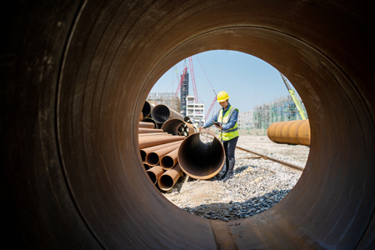
This article is my third since 2021. The subject of the prior articles has been from the perspective of a manufacturer’s representative and reporting from the field on items related to project funding, supply chain impacts on construction, and the general state of the industry from the point of sale and installation. So why not continue the discussion with this article?
We have discussed the supply chain challenges and personnel shortage issues previously. And as promised, I will update the reader on where these challenges are one year later. The supply chain issues seem to be persistent, but slightly better year over year. Evidence that the long lead times are prevalent and are here to stay can be seen from the proposals being offered by multiple manufacturers that need chip related and electrical control panel items as well as small-horsepower horizontal motors to complete the product offering. Challenges at the metal casting foundries seem persistent as well but have improved slightly in the past year. However, there is no quick remedy expected to emerge any time soon that will get the equipment supply chain back to the delivery time periods our industry saw in 2019.
Another primary focus in our industry is on how the many upcoming infrastructure related projects are going to get built. I was discussing this issue with Marty Boyd, PE and Lindsey Bryant, PE of Carter & Sloope Consulting Engineers recently and they noted that “there just isn’t enough skilled labor and tradesmen in the infrastructure construction market and not enough entering the workforce to build projects quickly.” The impact on the industry is that there are fewer contractors bidding individual projects and the contractors that are able to bid are asking for longer construction period language in the contracts. It is not uncommon to see one or two bidders on projects and in order to get them interested, the Owners had to agree to longer construction periods than originally stated in the bid documents. Marty and Lindsey also noted that “having only one bidder also creates challenges with local, state, and federal procurement requirements and can cause delays in projects proceeding because sole source approval has to be obtained.”
Contractors are stating that due to the limited supply of skilled personnel and superintendents, it is not uncommon for the contractors to concentrate on projects that are in relative proximity to each other so that the superintendent can easily travel from one site to the other and move skilled personnel more easily between two sites. By using the approach noted, it also requires the contractor to seek longer construction periods so that scheduling conflicts are limited when “sharing” project resources are required. Also, depending on the project equipment delivery times quoted by the suppliers, project construction times can be impacted by when certain equipment can be delivered from the manufacturer. All in all, longer construction periods are now the norm compared to previous years.
The longer construction periods are also challenging the funding side of the project. Longer construction periods add cost to the project that are not necessarily budgeted when the project estimated costs are assembled years before the project bids. Cost impacts are recognized by the contractor having to keep equipment and personnel active longer. Also, the cost for a manufacturer to have to finance the equipment sale longer before being paid (particularly on projects where the engineer specifies that the manufacturer is paid 90% upon delivery and 10% upon owner acceptance of the project) is also a consideration. The manufacturers are seeing their risk models being redefined by longer construction periods and higher interest rates.
The marketplace is recognizing that alternative payment terms to the manufacturer over multi-year construction projects can reduce some of the equipment related costs. It is becoming more common that the owner allows progress payments to be made to the manufacturer as they hit certain milestones rather than only paying them 90% upon delivery of finished product. Such a solution limits the risk to the manufacturer for financing equipment on a multi-year construction project and can potentially greatly reduce the capital cost of the equipment.
For the future, the industry is excited about the additional funding that the Build America, Buy America (BABA) legislation designated for the water industry over the next five years. The new bucket of money will no doubt be used for the betterment of the industry. The challenges for the manufacturers to meet the requirements imbedded in the legislation in order to meet the BABA materials of supply doctrines are still a point of discussion between the manufacturers and the federal government agencies that are tasked to manage the projects funded by the BABA legislation. Although there are many water-related companies that manufacture their products in the U.S., there are some specific manufacturers that are needed to make a project functional whom are still waiting to see what the on-shoring requirements will be for them and what the waiver process will entail in the short term. As of this writing, it is expected that the final documents from the federal reviewers will not give final directives until the end of this calendar year on this subject. We are all waiting on the final requirements to the regulations to be published so we as an industry can see if they help or hurt on the items discussed above.
In summary, the industry can expect costs of equipment and construction to remain at current levels in the short term and also to slowly creep higher year over year in the future. The number of projects that will be funded through the infrastructure legislation will guarantee that demands on equipment supply and construction companies remain at capacity. I will leave the reader with one interesting data point that I have tracked over the last 30 years in the state of Georgia. Over that period, I tracked the ratio of the total equipment cost on a new water or wastewater treatment plant to the total cost of construction for the project. Prior to 2020, the equipment cost vs total construction cost of the project showed that the equipment cost was in the 25% to 30% range of the total construction cost. Currently, that ratio has dropped to 17% to 20%. That data point should tell the reader that the more recent inflation factors have impacted the contractors more than the manufacturers since 2020.
Allen Walker is Senior Sales Engineer at Templeton & Associates Engineering Sales. He serves on the Water and Wastewater Equipment Manufacturers Association (WWEMA) Board of Directors and as Chair of the WWEMA Manufacturers Representatives Council. WWEMA is a non-profit trade association that has been working for water and wastewater technology and service providers since 1908. WWEMA’s members supply the most sophisticated leading-edge technologies and services, offering solutions to every water-related environmental problem and need facing today’s society. For more information about WWEMA, visit www.wwema.org.