WWEMA Window: Lessons On Galvanic Corrosion For Water And Wastewater Treatment Equipment Specifiers
By Michelle McNish
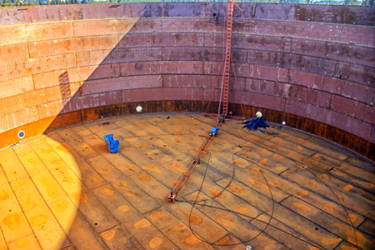
The subject of galvanic corrosion is of interest in the specification and supply of water and wastewater treatment equipment. Galvanic corrosion is a type of corrosion that occurs when two dissimilar metals are in electrical contact with each other, thus forming an electrical cell. A cell is said to consist of an anode and a cathode.
Metals can be classified as either active or passive according to their ability to form part of such a cell. A relatively active metal will form the anode, while a relatively passive metal will form the cathode. In the well-known example of carbon steel with a zinc coating (galvanizing), the more active metal (zinc) corrodes faster than the less active metal (carbon steel). This is why zinc coatings are referred to as a “sacrificial coating” when applied to steel components.
In order to determine which material will corrode (more anodic) and which material will be protected (more cathodic), the Galvanic Series for seawater, available in references or handbooks, can be used. It should be noted that certain alloys which normally exist in a passive state may become active in low-velocity or poorly aerated water and at shielded areas.
Galvanic corrosion occurs when two dissimilar metals are in metal-to-metal contact immersed in a conductive liquid. Electrical contact is needed for galvanic corrosion to occur. Galvanic corrosion will NOT occur when dissimilar metals are submerged into a conductive liquid but NOT in electrical contact with each other. Keep in mind that other types of corrosion may occur if the metal is not compatible with the liquid.
In water and wastewater treatment equipment, galvanic corrosion occurs where submerged stainless steel (cathode) components are used in combination with submerged zinc hot dip galvanized (HDG) steel structure, which acts as the anode. The zinc coating located directly adjacent to the stainless steel is directly affected first and then corrosion spreads outward. To avoid galvanic corrosion when both stainless steel and galvanized steel are submerged and electrically connected, galvanized steel should be used instead of stainless steel. If this is not possible, galvanic corrosion can be prevented if the direct metal-to-metal contact is eliminated through the use of non-conductive (rubber or plastic) insulators. If the possibility of galvanic corrosion is to be completely eliminated, every single stainless-steel component will need to be completely isolated from the galvanized steel components that they are in contact with, which increases equipment costs.
There are several conditions that determine the rate of the galvanic corrosion. The greater the difference in potential between metals on the Galvanic Series chart, the higher the rate that galvanic corrosion will occur. Also, as the surface area of the cathode relative to the anode increases, so does the rate of galvanic corrosion. The composition of the liquid will also have an effect on the galvanic corrosion rate, although this composition is dictated by process requirements and not equipment concerns. It should be noted that galvanic corrosion does not occur at the same rate in all liquids.
When stainless steels are listed in the Galvanic Series chart, there are values given for stainless steel in the “active” and “passive” states. Under most operating environments, there is an extremely thin (1-5 nanometers thick) chromium-rich oxide film that forms naturally on the surface of stainless steel. This thin film is chemically stable (i.e., passive) when there is sufficient oxygen available. If this film is removed or not able to form due to severe environmental conditions, then the stainless steel is considered active. In the vast majority of water and wastewater treatment applications, stainless steel will be in the passive state.
Galvanic corrosion will also occur where stainless steel (cathode) is used in combination with painted carbon steel or cast iron (anode). Painting is not sufficient to provide the barrier needed to electrically isolate the two metals and, therefore, prevent galvanic corrosion. In many cases, more substantial isolation is needed in the form of non-conductive spacers. In this system where painting is perceived to protect the steel from corrosion, it actually accelerates galvanic corrosion. The paint will cause the corrosion of the steel to accelerate at the coating holidays in the form of pitting. In the absence of stainless-steel isolation with non-conductive insulators, the stainless-steel components can be coated and the corrosion rate will be significantly decreased.
Another way to prevent galvanic corrosion of components is through the use of a cathodic protection system. Properly designed, installed, and maintained cathodic protection corrosion control systems can save owners tens of thousands of dollars in maintenance, repair, and recoating costs on the submerged steel components of a treatment system over the design life of the equipment. In this system, sacrificial anodes (typically magnesium alloy H1C) are uniformly distributed on the surface of the collector components. The size and quantity of anodes is based on the surface area of steel and stainless steel and the amount of time the anodes are expected to protect the system.
Another cathodic protection method is an impressed current system. In this system, an electrical current is caused to flow from an electrode (cathode) to the structure to be protected (anode). The effect of this impressed current is to counteract the naturally arising electrical currents present whenever conductive and dissimilar materials are in electrical contact. Impressed current systems tend to have a low initial cost with higher operating and maintenance costs than a galvanic system with sacrificial anodes.
Coal tar coatings are commonly used to isolate aluminum handrail systems from steel mounting surfaces. These same coatings can be used to isolate submerged stainless-steel components from steel structures provided precautions are taken to prevent damage to the coating when assembling or during operation.
Specifiers are urged to carefully evaluate the possibility of galvanic corrosion when selecting materials for water and wastewater treatment equipment.
Example 1: Consider a wastewater sludge collector mechanism used in a clarifier, where a hot dip galvanized collector mechanism has stainless steel fasteners. Experience indicates this situation will experience insignificant galvanic corrosion overall because the surface area of stainless steel relative to the surface area of HDG is small. The HDG coating located directly next to the stainless-steel fasteners will be affected first and then corrosion will spread outward. In order to eliminate any chance of galvanic corrosion at the fasteners, hot dip galvanized fasteners should be considered.
Example 2: Consider the same HDG collector mechanism with stainless steel fasteners but now with stainless steel squeegees to sweep the bottom of the tank. This mechanism will experience significant galvanic corrosion because the surface area of stainless steel relative to the surface area of HDG is large enough to cause concern. Specifiers should strongly consider use of galvanized steel squeegees in this situation.
As illustrated above, there a number of factors that affect whether and the degree to which galvanic corrosion will occur. Operators and others involved in treatment technology equipment selection should be mindful of the equipment’s metal composition, its intended installation environment, particularly what metals the equipment may have immediately adjacent to it when integrated, and whether it will be in an environment where electricity will be conducted. With a full understanding of product composition, its application, and underlying chemistry, operators can make wise choices that extend equipment life and save significant money.
Michelle McNish is President of Walker Process Equipment, a Division of McNish Corporation, and a member of the Water and Wastewater Equipment Manufacturers Association (WWEMA) Board of Directors. WWEMA is a non-profit trade association formed in 1908 to represent water and wastewater technology manufacturers and related service providers. WWEMA is made up of many of the most prominent and influential companies in the industry who are working together to shape the future of water and wastewater technology in the U.S. and around the world. For more information about WWEMA, go to www.wwema.org. Interested in becoming a WWEMA member? Contact WWEMA Executive Director, Vanessa Leiby at vanessa@wwema.org.