WWEMA Window: Increasing Efficiency Of Sludge Handling, Transport, And Storage Using Shaftless Spiral Conveyor Technology
By Fritz Egger
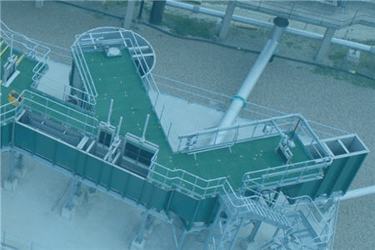
Customizable and durable conveying equipment is essential for today's sludge systems. An array of equipment can help make that goal a reality, but at the peak of efficiency lie shaftless spiral conveyors with expected system life of 20 to 25 years.
Sludge Transport
For many facilities, space is at a premium, which is why the shaftless spiral conveyor is designed to integrate into many configurations, both greenfield and retrofit. Maintenance is dramatically reduced when compared to traditional conveying methods. Over the long term, this reduced need for maintenance means plants can instead focus on improving other operations areas instead of carrying out frequent repairs.
The elimination of a central shaft allows a much higher fill rate, resulting in greater efficiency, smaller spiral diameters, and consequently less wear and power usage.
Material handling can place a lot of pressure on equipment, and many applications require handling of harmful or possibly corrosive substances. Sewage sludge can vary significantly between sites, although very abrasive sludge can normally be identified due to its effect on other equipment. For example, an abrasive sludge will reduce the life of the scroll in a centrifuge and the rotor/stator in a progressive cavity pump. Fitting a suitable conveyor trough liner is crucial to reduce wear. Composite liners constructed out of a hard-wearing, two-colored material, indicating wear and providing and a specific determination (color change) that liner replacement is due, are ideal.
Reliability often comes from simplicity, and shaftless spiral conveying systems operate at very low revolutions per minute (RPM), meaning there's a long-life expectancy for components. This low RPM also results in low power usage — key for more significant energy savings.
Horizontal and inclined conveying can efficiently be accomplished using U-trough type spiral housings that can be employed for inclines up to 30 degrees (Figure 1). Octagonal troughs can be utilized for inclines from 30 to 90 degrees (Figure 2). Both trough types are fully enclosed, eliminating odors and spillage. Single horizontal runs can exceed 150 ft. on a single motor/gearbox. Vertical conveyors can lift sludge 40 ft. per stage and up to three stages.
Figure 1: U through
Figure 2: Octagonal OK trough with split casing
Shaftless spiral technology is extremely practical and efficient when connections between multidirectional conveyors are required for horizontal, inclined, and vertical sludge transfers (Figure 3).
Figure 3
Sludge Storage And Outloading
Sludge storage silos and outloading systems are increasing in use and popularity and can be configured as ground-level or raised bins, either rectangular (Figure 4a) or cylindrical (Figure 4b).
Figure 4a: Rectangular live-bottom silo
Figure 4b: Cylindrical live-bottom silo
Outloading from silos can be accomplished through live bottoms (Figure 5) or sliding frame systems (Figure 6). Discharge rates are controlled via conveyor speed along with motorized slide gates (Figure 7).
Live bottoms consist of multiple spiral conveyors that form a rectangular bed of moving spirals to eliminate bridging or blockage of the stickiest sludges. Spirals are designed with a reversing section to prevent material from building up at the end of the spiral. Speed is controlled to provide outloading rates suitable for desired discharge, either for rapid truck-filling or pump feed. While the silos follow standardized design features, sizes, and orientations can be customized to suit most requirements. These silos are top-loaded, typically by shaftless spiral incline or vertical/horizontal conveyors, and outloaded by large diameter/large pitch live-bottom shaftless screws. These live-bottom systems ensure the elimination of arching, rat-holing, or any bottleneck-type losses in flowability, even for the stickiest or driest of sludges.
Very low RPM ensures that trough liners will rarely need replacing (perhaps once per decade). Simple operation, direct drive, and few moving parts ensure that maintenance is near zero. Inspection of the interiors of these silos is not required, except at perhaps 5- to 10-year intervals.
Figure 5: Live-bottom silo
Sliding frame bottoms feature a slowly reciprocating, hydraulically driven steel frame that pushes or pulls sludge toward a central extraction screw. The action of the hydraulically driven sliding frame breaks any bridges that may form over the extraction screw and pushes/pulls the material toward the center of the silo for discharge. Speed is again controlled to provide outloading rates suitable for rapid truck-filling or pump feed.
For round silos, the sliding frame is built as an elliptical frame, made of solid steel bars profiled to a wedge shape. This elliptical framework, with its wedge profile, pushes under the sludge in one direction and draws it toward the discharge opening in the other, thereby allowing near total emptying of a flat-bottom silo. The rectangular sliding frame silos are constructed as a rectangular "ladder" shape, transferring material from one wedge-shaped "step" of the "ladder" to the next as it oscillates back and forth. This design is suitable for steel or concrete silos or bunkers.
Figure 6: Round and rectangular sliding frame
Figure 7: Motorized slide gates
Other Applications For Shaftless Spiral Conveyors
This technology is also highly suitable for many other applications in water and wastewater systems as well as industrial applications. These include efficient handling and transport of pump station and headworks screenings transport and grit transportation, including submerged applications.
When designing a conveyor system, a combination of factors needs to be considered when sizing the trough, spiral, and drive motor/gearbox. A reliable shaftless spiral conveying system for waste water treatment plants starts with selecting the right size conveyor and a high-quality manufacturer.
Fritz Egger is General Manager – SPIRAC (USA) Inc. He is a member of the Water and Wastewater Equipment Manufacturers Association (WWEMA) Board of Directors and serves on the Association’s Investment Committee. WWEMA is a non-profit trade association that has been representing water and wastewater technology and service providers since 1908. WWEMA’s members supply the most sophisticated leading-edge technologies and services, offering solutions to every water-related environmental problem and need facing today’s society. For more information about WWEMA go to www.wwema.org