Why It's Time To View Plastic Pipe In A Whole New Light
Recent advances in plastic materials and processing have led to a new generation of plastic piping systems to handle challenging water and chemical environments. So, it is important to revisit this topic and see why some older piping choices might no longer be the best bet. Here are some big-picture and narrow-focus reasons to consider plastic-piping choices for municipal water/wastewater, food processing, pharmaceutical, chemical, and industrial process-water/wastewater applications in a whole new light.
Why Old Perspectives Are Not Always Valid
In the early days of plastic piping, corrosion resistance was a primary consideration. Plastic (typically PVC) offered a lower-cost alternative than stainless-steel piping for handling caustic, corrosive materials. Today, the considerations are not simply either/or — plastic pipe vs. metal pipe — but a whole progression of opportunities and considerations afforded by today’s highly engineered plastic-piping-system solutions. Here are four major considerations to account for when looking at new piping alternatives:
- Pipe vs. Piping System. Aside from chemical resistance, there are many reasons to consider plastic piping — or more accurately, specific compositions of plastic piping — for certain installations. Those include weight, fittings options, pressure rating, thermal expansion, and convenient assembly methods for the specific type of plastic within acceptable limits of structural strength. That is why it is important to evaluate not only piping materials but the entire piping system solution, including the joining technology, structural support systems, and other compatible components.
- Metal vs. PVC vs. Alternate Plastics. First, do not let legacy specifications dictate pipe material choices. In some cases, the qualities of today’s plastic piping options might not have been available at the time they were written. Also, even if the primary assessment is between metal and PVC, do not limit the search to that single comparison. Start with a broad review of different plastic performance characteristics with regard to the main application requirements — PVC, clear PVC, chlorinated PVC (CPVC), polypropylene (PP), polyvinylidene fluoride (PVDF), high-density polyethylene (HDPE), acrylonitrile butadiene styrene (ABS), and even double-containment designs for visible leak detection (Figure 1).
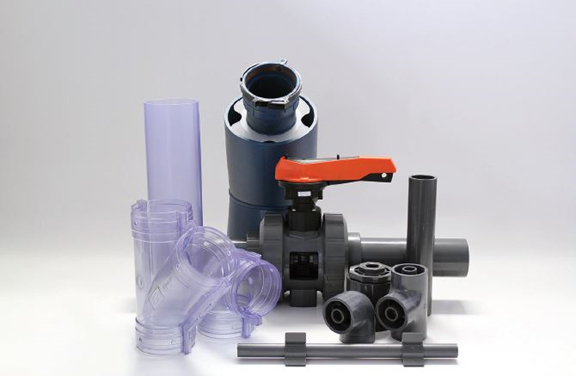
Photo courtesy of GF Piping
Figure 1. Specialized plastic piping system designs can be matched to the unique needs of many applications, such as the see-through design of this double-containment solution for aggressive chemicals.
As this physical performance chart of engineered plastic piping systems indicates, not all plastic pipe is interchangeable across all applications. For example, these photographic comparisons of PP, PVDF, and CPVC piping show the difference between success and failure in a special waste application.
- Chemical vs. Structural Performance. Granted, some plastic piping systems will require a different design approach — from support structures to construction methods — but learning how to adapt to differences that make plastic piping so attractive is a one-time investment that can pay a lifetime of dividends.
- Purchase Cost vs. Total Cost Of Ownership (TCO). The cost of ownership for any piping system is not the bottom line on the piping invoice. It also includes installation labor hours and costs for equipment and special designs. The total system solution that provides the best balance of material cost, installation cost and convenience, and greatest influence on performance longevity is typically the one to choose. (For example, HDPE will maintain the same friction-loss effect 50 years from now as it does today, while cast iron will get more expensive to operate over time due to material buildup and friction on the interior of the pipe.) TCO can be a particularly eye-opening consideration when comparing a specific plastic piping system option vs. metal or other types of plastic pipe (Figure 2).
Photo courtesy of GF Piping
Figure 2. Matched pipe materials and joining technologies that can speed installation for water and chemical applications should be considered as part of a total cost of ownership evaluation.
What’s In A Name?
With all the different operating environments and chemical properties experienced in water-treatment, industrial process, laboratory, pharmaceutical, or chemical production environments, it is important to differentiate among the major types and sub-classes of plastic piping appropriate for each unique application. Even within the common classification of ‘PVC pipe,’ there can be physical performance differences among pipes and fittings from different manufacturers. Here are just a few of the reasons why not all commonly labeled PVC pipes and fittings share the same performance characteristics.
- Stabilizer Blends. Not every compound bearing the PVC label is identical. Different stabilizers used for different balances of ductility and impact resistance, or compounds optimized for extrusion vs. injection molding, can all affect the performance of finished installations in real-world applications.
- Mechanical Stresses. Even when the chemical composition and additives are virtually the same, differences in production processes can impact the mechanical stresses on the pipe walls. For example, running pipe extrusions at a very high rate can reduce manufacturing costs but at the trade-off of increasing stresses on the pipe walls. That can contribute to premature mechanical or chemical failures over time in an end-use application.
- Differing Sources Of Information. Even when technical references are provided for a pipe material’s chemical compatibility, it is important to know how they were derived. If ratings are provided by the raw material supplier before any production processing, the applicability of those ratings could be impacted by subsequent production processes. The most reliable results are obtained from chemical testing and pressure testing conducted after the manufactured parts have been joined into a complete piping assembly.
- Cell Classification: The ASTM D1784 specification covers thermoplastic compounds for use in extruded or molded form such as pipe and fitting applications. Identifications/comparisons of materials are rated according to base resin, impact resistance under notch, tensile strength, modulus of elasticity in tension, deflection temperature under load, and flammability.
The key takeaway is that it is extremely important to communicate with the plastic pipe and fitting manufacturer to ensure the appropriate field performance criteria for the specific products being evaluated (Figure 3).
Chart courtesy of GF Piping
Figure 3. Work closely with plastic piping system suppliers who can identify material compatibility by chemistry, operating temperature, and joining technology within the intended application.
New Design/Installation Opportunities And Accommodations
Whether or not chemical-resistance considerations are significant in a given application, properly designed installations of lightweight, easy-to-install, and cost-effective piping systems offer advantages for any application.
Skid-mounted, modular wastewater treatment systems are an excellent example. Weight-saving plastic piping, fittings, valves, and actuators are just the start. Equally important, compatible instruments — such as plastic full-bore mag meters that deliver + 1 percent reading accuracy even with minimal straight pipe length requirements after valves, elbows, or injection ports — can maintain performance accuracy while reducing skid size, assembly time, and shipping costs.
When taking advantage of the opportunity to switch from metal to plastic piping materials in any application, be sure to account for these important design considerations:
- Support Spacing. While the very structure of metal piping and fittings provides a certain degree of self-support — at the expense of added weight — plastic piping requires a slightly different mind-set. For example, the open spaces between support points might need to be closer together. Plastic piping might also require direct support under manually operated valves to prevent stresses from being transferred to adjacent pipe and fittings, especially in installations subject to vibration or water hammer.
- Support Flexibility. Because some styles of plastic piping experience more flex or thermal expansion than others, be sure to use appropriately designed mounting hardware that provides the best support while still allowing for natural movement. That requires accounting for the temperature ranges of both the operating environment and the materials being conveyed, appropriate span lengths between supports, and versatility in mounting components to accommodate dynamic operation (Figure 4).
Photo courtesy of GF Piping
Figure 4. As shown by the graphic image on the right, a close-fitting, metal squeeze-clamp can pinch the pipe, exerting uneven stresses on it. By contrast, plastic support and containment mounting systems (inset image) matched to the specific pipe size will provide evenly distributed support plus room for expansion or flexing without undue pressure on the plastic pipe.
- Installation Advantages. Piping-system attributes that can simplify design requirements, save weight and space, and speed installation — all with attendant cost benefits — are important factors in installation labor and TCO. The lighter weight of plastic piping can make overhead installation easier, requiring fewer workers and less equipment. Various joining techniques provide secure connections with easy assembly requirements.
- Easy joining procedures using solvent cement simplify building more complex bends or manifolds in tight quarters as compared to threaded pipe. Ensure proper preparation, proper fit, and proper cure time to maximize performance reliability.
- Deep-bell insertion fittings with integral restraints that allow + 5 degrees of deflection in any direction speed installation and simplify alignment in less than perfect trench conditions.
- Piping systems that accommodate both electrofusion and mechanical leakproof joints can provide equal convenience for shop floor and field assembly.
- Other Special Considerations. In order to maintain ample safety ratings, be sure to account for special trade-offs when using plastic piping under exceptional circumstances.
- Stay within the material, temperature, and wall-thickness design ratings for the fluids being conveyed.
- For more extreme requirements, be sure to consult the manufacturer on how to de-rate the design for safe performance. For example, if threaded connections are used with Schedule-80 PVC piping, be sure to reduce the pressure rating of the pipe by 50 percent from the rating for plain-end pipe at 73 degrees.
Choose A Complete Package Solution
Choosing comprehensive piping solutions that offer chemical and thermal compatibility throughout the entire cast of supporting devices — including valves, instruments, support systems, and other components — minimizes the potential for problems in the final installation.
- Insist on job-matched mounting systems that relieve potential stresses of thermal expansion/contraction or seismic events and provide sound yet flexible support for lightweight pipe across long distances.
- Complement any plastic piping design with process-compatible valves and actuators suited to the application, including manually, electrically, or pneumatically controlled ball, butterfly, or diaphragm designs.
- Ensure precise monitoring and control with compatible plastic instruments and sensors that can satisfy both process conditions and control requirements for measuring flow, level, turbidity, chlorine, pH, oxidation reduction potential (ORP), and conductivity.
- Finally, look for vendor support that can enhance the longevity of installed systems through training programs for pipe fusion, instrumentation, and actuation practices.