When Density Is Desirable
By Leon Downing, Eric Redmond, and Isaac Avila
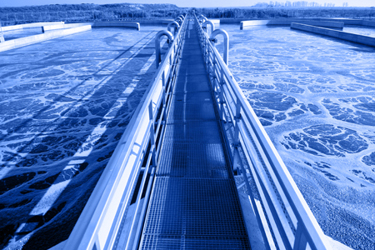
Infrastructure intensification through densification and granulation can help utilities meet nutrient management goals with minimal investment through retrofit.
The Clean Water Act of 1972 called for the cleanup of U.S. waterways. Over the past 50 years, regulatory focus has shifted from the removal of pollutants to recovery of water and embedded resources such as phosphorus and energy. When water sector stakeholders who participated in “Black & Veatch’s 2022 Water Report”1 were asked to select all expected reasons for adding new technology, “new regulation” was the most common response, followed by “nutrient removal.”
Solutions and specific technologies that help utility managers simultaneously meet multiple needs, such as regulatory compliance and performance optimization for nutrient management, are especially valuable. Mixed liquor densification and granulation has become attractive to utility managers because this technology enables managers to easily retrofit upgrades into existing infrastructure.
Water resource recovery facilities (WRRFs) with fixed or limited infrastructure are challenged to manage increasing nutrient loads while meeting stringent effluent requirements. Often, new effluent requirements dictate modifications to the activated sludge process, such as adding unaerated zones, increasing sludge retention times (SRTs), and addressing higher energy demands due to increased aeration requirements. These changes can result in the need for new tanks — particularly final clarifiers — when using traditional approaches to achieve nutrient removal.
Why Consider Densification And Granulation?
The main benefit of densification and granulation is that improved settling rates of mixed liquor suspended solids (MLSS) increase the overall capacity of the activated sludge system without the addition of new tank volume. Facility owners can achieve more rapid settling of sludge through MLSS densification and granulation.
Granulation is a descriptive word for large flocs in an activated sludge system. These large flocs settle rapidly in final clarifiers and provide stratified growth environments to improve biological nutrient removal. Facilitating the formation of granules in the MLSS intensifies the activated sludge process and minimizes additional capital investment in infrastructure.
Densification is the overall process that results in closely compacted activated sludge flocs. It is indicative of a continuous flow activated sludge system with granules making up the majority of the MLSS. Mixed liquor densification and granulation has become attractive to utility managers to easily retrofit existing infrastructure with performance enhancements that expanded capacity and improved effluent quality with reduced capital investment.
Facilities that have applied granulation and densification have observed faster settling rates that have increased the capacity of their activated sludge systems by 20 to 40%. Increasing the available capacity enables WRRFs to comply with new nutrient management regulations, which would typically require large infrastructure investment, with relatively minor investment.
The second benefit is nutrient removal. Improving settleability decreases effluent total suspended solids (TSS). This reduction in TSS reduces the effluent’s total phosphorus and total nitrogen concentration. In addition, the larger granules lead to simultaneous biological nutrient removal (BNR), further reducing the soluble phosphorus and nitrogen concentration in the effluent from the activated sludge facility. In the north central U.S., densification resulted in an additional 10 mg/L of net nitrogen removal and an additional 0.5 mg/L of total phosphorus removal in one facility’s BNR configuration.
As the water sector looks to intensify the activated sludge process at WRRFs to avoid the capitally intensive addition of new tanks, the rate at which MLSS settle in final clarifiers has become a focal point. The capacity of an activated sludge system rarely is limited by the hydraulic retention time of the aeration basin or the surface area of the final clarifiers. It more often is limited by how quickly the solids in the MLSS settle in the final clarifiers.
As facility operators increase SRTs to manage increasing nutrient loads — and more volume is converted to unaerated rather than aerated volume — the concentration of MLSS in the activated sludge process increases. If the MLSS do not settle at a rate that allows the solids to be removed in the existing clarifiers, new tanks or substantial retrofits to existing infrastructure are required. One retrofit option would be to increase the volume of the aeration tanks to reduce the MLSS concentration. The other option would be to increase the surface area of the final clarifiers to increase settling time for the MLSS. These retrofit options carry a high cost for utilities.
To avoid costly infrastructure retrofits and expansions, engineers, operators, and researchers have been refining the approach to activated sludge settleability. Since the first publications related to activated sludge design by Ardern and Locket in 1914, designers and operators of WRRFs have focused on consistent settling of the MLSS created in the activated sludge process. Given the financial pressure to optimize capital investment, the focus now extends beyond consistent settling to rapid settling.
When granules can be formed in a continuous-flow activated sludge system, the densified activated sludge process has been demonstrated to: (1) increase capacity by improving sludge settleability without the need for costly system modification or expansion; (2) increase biomass inventory, thus increasing the ability to handle higher loads and operate at higher SRTs; and (3) potentially improve biological nitrogen and phosphorus removal and improve solids removal.
Research And Application Revelations
The key question is how to actively induce granules and promote densification in activated sludge facilities. Decades of research at pilot and full-scale facilities has shown that the combination of selector zones, feast-and-famine conditions, and physical selection are key contributors to the formation of granules in activated sludge systems.
Selector zones. Promotion of biomass growth in unaerated zones, called biological selector zones or selector zones, is a critical element of densification and granulation. These selector zones located at the influent of aeration basins provide biological selective pressure that enables the formation of granules. Growth pressure for granular sludge requires high food-to-microorganism (F:M) loadings in the selector zone at the head of an aeration basin to create large flocs. This is a feast condition, where a high amount of food (represented at WRRFs by biochemical oxygen demand) is available relative to the microorganisms present in the MLSS of an activated sludge system. The high F:M loading provides the growth pressure required to diffuse BOD into a larger floc and form beneficial extracellular polymeric substance (EPS) in the floc. This EPS is the “glue” required to form stable granules.
Selector zones are typically designed and operated to achieve anaerobic conditions. Anaerobic conditions have been studied more than aerobic selector zones, but research also has documented the impacts of aerobic selector zones on the formation of granules and densified activated sludge.
Key contributors to induce mixed liquor densification and granulation in a continuous flow activated sludge system (Credit: Black & Veatch)
Feast-and-famine conditions. It is important to create a famine period in plug-flow aeration basins after exposing the MLSS to a high F:M loading in a selector zone. Famine conditions, where a low F:M is present, encourage the biomass in the granules that make up the MLSS to consume any stored food in their cells. This ensures that they are essentially “hungry” when they return to the selector zones of the aeration basin after being settled and recycled in the final clarifiers with the return activated sludge (RAS).
A hydrocyclone facility like this one is used for physical selection in combination with selector zones to induce granulation and promote densification in a continuous-flow system. (Credit: Black & Veatch)
Incorporation of selector zones often requires the addition of a baffle wall and mixers at the influent of an aeration basin, as shown here in operation at Trinity River Authority’s granulated activated sludge process. (Credit: Black & Veatch)
Physical selection. Physical selection involves selectively wasting lighter, smaller flocs out of the activated sludge system while retaining the heavier, denser flocs and granules. Although not required to induce granule formation, physical selection increases the fraction of granules in the activated sludge process and ultimately facilitates shifting to a densified activated sludge system. This process has been documented to occur in surface wasting facilities, where waste activated sludge (WAS) is wasted from the top of aeration tanks rather than from RAS. This non-proprietary process removes lighter flocs but requires a much larger flow rate of WAS due to the lower concentration of MLSS compared to RAS.
More recently, hydrocyclones have been used to gravimetrically separate dense granules and light flocs from RAS. The dense granules are returned to the aeration basins in the underflow of the hydrocyclones, while the lighter flocs leave in the overflow from the hydrocyclones. The overflow from the hydrocyclones typically replaces traditional wasting of WAS from the clarifier. This physical selection approach ensures retention of any granules formed in the system.
The Bottom Line
Given the benefits of densification, it is important to understand the investments that are required. Densification will avoid the need for new tanks, but there will likely need to be several lower-cost improvements. To add selector zones and ensure feast-and-famine conditions, some aeration basins may require the addition of interior baffle walls and mixers. For physical selection, facility owners can incorporate surface wasting into new activated sludge facilities. For retrofit applications, which is the typical use of intensification, adding hydrocyclones to RAS/WAS lines is essential. Use of a hydrocyclone system, combined with modifications to pumps and piping, is necessary for such retrofits. Given the cost of new tanks, the addition of baffle walls, mixing, and selective wasting can typically be accomplished at 20 to 30% of the cost of a typical expansion.
Densification can help WRRFs increase capacity and improve performance through biological and physical selection. Existing facilities, including continuous flow systems, can be retrofitted to form granular sludge, which makes densified activated sludge a comparatively cost-effective way to do more with less investment. Understanding the benefits, necessary conditions, and options is crucial to the successful application of this technology.
References:
About The Authors
Leon Downing, Ph.D, PE, is the global practice and technology leader for nutrient removal and recovery with Black & Veatch. He provides technology leadership in support of Black & Veatch process engineering and applied research projects globally.
Eric Redmond, PE, is a wastewater process engineer with Black & Veatch. His specific expertise includes design and operational optimization of low-energy nutrient removal and granulation facilities.
Isaac Avila, PE, CWP, is a wastewater process engineer with Black & Veatch. He specializes in aerobic granular sludge and mixed liquor densification. Isaac has firsthand operational experience in inducing granulation in a 12-MGD continuous flow activated sludge system.