What Are The Latest Innovations In Corrosion Prevention For Water Infrastructure?
By Ellie Gabel
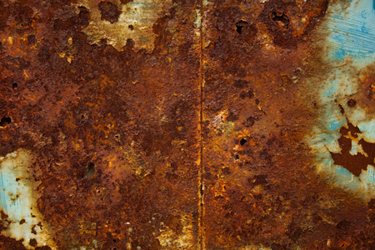
Corrosion prevention is a pressing concern for wastewater professionals in the U.S. and elsewhere. Corroded infrastructure can fail prematurely and cause other costly complications that disrupt operations and negatively impact providers’ reputations. What progress has occurred in tackling the problem and giving decision-makers new solutions to consider?
Improving Dosing Control Measures
Hydrogen sulfide is a top cause of corrosion, and it can also make water smell unpleasant, making wastewater professionals eager to mitigate it. Chemical dosing is one of the most widespread ways to do so. However, an extensive project in Australia showed how professionals within and outside the country might improve their methods.
The project involved more than a decade of research made possible with funding from a research council and 17 water industry partners. The group explored how to improve the chemical interventions used to control hydrogen sulfide. Incorrect applications increase waste and pose safety risks since excessive quantities release toxins into the atmosphere.
A new approach has saved $400 million for the Australian water industry so far. It uses online control algorithms and modeling techniques to determine the chemical quantities necessary to prevent corrosion. Designed for single sewer pipes, this system relies on data from autoregressive models built on flow measurement information. Those suggest the amount of ferrous salt to control sulfide without wasting supplies or money.
The results of real-life experiments showed wastewater professionals could reduce chemical applications by 15–45%, making this option worth pursuing. After developing the first-generation system and seeing those promising results, the researchers developed an improvement that was more applicable to industrial applications. It monitors entire networks instead of single pipes.
These enhanced algorithms can also manipulate sewage pumping stations and dosing applications, allowing wastewater workers to use 40–50% fewer chemicals to control corrosion. This example shows how improved visibility and tighter control can make internal processes more effective while reducing waste.
Using Biomineralization As A Microbial Corrosion Safeguard
People choosing materials for industrial applications must consider the surrounding environment to prevent premature damage. For example, duplex stainless steel withstands pitting and crevice corrosion. It also holds up well in high-chloride environments.
Researchers from The Hong Kong Polytechnic University focused on protective measures for concrete at risk of microbially induced corrosion. Although their work centered around the material used in marine environments, that type of deterioration also occurs in harsh environments — including wastewater treatment plants — characterized by corrosive microorganisms. These can cause concrete infrastructure to crack, resulting in significant repair costs and potential service disruptions.
The group recognized that biomineralized films could be effective protective measures once they form on at-risk surfaces. They developed an eco-friendly coating that uses carbon dioxide to make mineral precipitates and increase concrete’s durability. Tests indicated it positively impacted the total and relative abundance of hydrogen sulfide-producing bacteria. Additionally, this coating-controlled sulfate diffusion and made the concrete last longer.
It may also be a relatively low-maintenance measure. The researchers found no need to reapply the substance if the original coating remained intact. That benefit minimized the associated costs and carbon footprint burdens.
Exploring A Sprayable Material To Prevent Corrosion
Many innovations occur when people investigate applications for known materials. Such was the case with poly(phenylene methylene), a multifunctional polymer that doubles as a fluorescent coating that protects against corrosion. More commonly known as PPM, it has recently attracted attention from scientists who want to find the most feasible use cases.
Tests showed PPM protects metals — especially aluminum — against corrosion, making it a potentially viable safeguard for the wastewater treatment industry. Application layers can be up to 10 times thinner than epoxy resin coatings and retain the necessary durability.
Additionally, the research showed wastewater professionals could apply PPM as a sprayable protectant that would repair itself if damage occurred. Most coatings do not naturally have that characteristic and need additives to demonstrate it. Those extras have downsides because they can move within the coating over time and enter the environment. However, PPM repairs itself without additives.
Another environmental benefit is that people can remove and recycle the coating. Although these processes sacrifice some polymer material, the overall recycling rate is 95%. Tests showed researchers could reuse the PPM coating up to five times. They clarified that no PPM product is harmless to the environment, but a thoughtful approach could significantly reduce negative impacts.
The coating is a patent-pending innovation and is not yet commercially available. However, if the coating becomes widely accessible, it could significantly change how wastewater professionals treat their infrastructure to prevent complications and increase resilience.
Active And Ongoing Corrosion Prevention Successes
Although these innovations occurred outside the U.S., industry professionals within the country will undoubtedly find them interesting and applicable. Corrosion is an urgent matter and global issue for those overseeing critical infrastructure.
Ellie Gabel is a writer specializing in environmental science and innovative technologies. She can be reached at ellie@revolutionized.com.