5 Ways To Use Flow Meters In Biopharmaceutical Processing

By Emily Newton
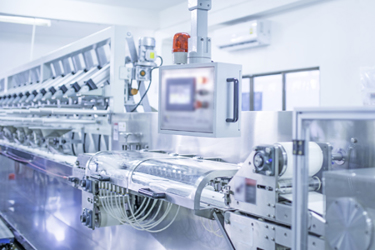
Biopharmaceutical processing is highly precise, and people must rely on various measuring devices to control costs, maintain quality, and avoid accidents. They often use flow meters to accomplish many of those aims. Here are some specific ways professionals working in pharmaceutical processing use these devices, making them so instrumental in successful outcomes.
1. The Biopharmaceutical Processing of Coated Pills
Many pills feature external coatings, which serve numerous purposes. One of the most common is to make them easier for people to swallow. However, they can also give pills a longer shelf life or cause a shielding effect so tablets with a crumbly or powdery consistency don’t break down too soon in someone’s mouth.
Pill coating can also be important for brand identity, helping people confirm they have genuine medications rather than clever counterfeits. Some researchers have found creatively unconventional ways to coat pills. Take the example of a bioengineering professor who used nonpareil candies as a tasty and anti-counterfeiting type of pill coating. The more typical ways to coat pills are to put them into drum or pan coaters to thoroughly distribute the material comprising the outermost layer.
However, some pharmaceutical processing efforts rely on flow meters, which often give better results than traditional methods. One option that allows manufacturers to coat small pill batches in less time involves using a low-momentum spray nozzle, along with a pressurized fluid delivery tank and a flow controller. The controller also has a metering function that lets users verify how much coating is distributed onto each pill.
This particular solution provides accurate flow measurements regardless of the fluid passing through it. That versatility allows manufacturers to consider using a similar setup for other needs in a biopharmaceutical processing plant.
2. Control and Oversight in Pharmaceutical Processing
Productive biopharmaceutical processing requires various combined factors working together to provide the desired outcomes. That’s why many pharmaceutical plant managers use flow meters to control what’s happening in a facility better. Ultrasonic flow meters are commonly chosen options for such applications.
These varieties are highly accurate, especially if people choose insertion or inline flow meters for their pharmaceutical processing needs. Individuals must follow the manufacturer’s instructions, checking that the measuring device is firmly mounted and installed according to the recommendations.
Many flow meters have Internet of Things (IoT) technology. Their associated sensors can give users real-time information about what’s happening in a biopharmaceutical processing facility. The gathered data usually goes to the cloud, where it remains available for later reference. People can then pull up the information on any internet-connected device, such as tablets and smartphones. This cloud computing application and others like it supports better collaboration among parties, helping people give insights from wherever they are located.
Since flow meters measure the speed and volume of substances passing through pipes or similar channels, people can use them to establish baselines for normal activity. That makes it easier for them to detect if something’s wrong and get the appropriate parties to take a closer look.
This increased visibility helps leaders verify that everything in a pharmaceutical processing plant is running as intended. When flow meters and other measuring devices show it isn’t, the increased data collection and availability allows people to take action sooner rather than later. That’s critical since biopharmaceutical processing is so heavily regulated.
3. Avoidance of Contamination
Pharmaceutical manufacturing professionals must follow tightly controlled best practices and procedures to prevent catastrophic problems. These products have a global reach, and employees must do everything possible to keep quality levels high. Having specialized equipment, including flow meters, is also essential for this aim.
The proper utilization of flow meters can also prevent issues that could otherwise have ripple effects within the processing plant. Consider a particularly egregious example where workers at a Dr. Reddy’s facility tried to fix a leak with zip ties. This was uncovered during a federal investigation that resulted in regulators finding eight faults.
Flow meters aren’t enough to stop contamination, but they can become part of an overarching prevention strategy. For example, contamination control efforts at some pharmaceutical plants include using remote visual inspection (RVI) equipment, such as videoscopes and borescopes, to see inside tubes and other difficult-to-access vessels. Those approaches improve monitoring methods to prevent the growth of microbiological colonies.
Many decision-makers invest in hygienic flow meters when contamination management is a priority. Such designs feature sensors that never come in direct contact with the fluid they measure, which supports cleanliness requirements. The equipment is also easy to set up, letting people finish the process in less than a minute.
4. Facilitating Faster Manufacturing Turnaround Times
Another common reason to use flow meters in biopharmaceutical processing is to make manufacturing lines more versatile when producers work with various biosimilar processes in their plants. They choose single-use flow meters in such instances.
Despite their names, many suppliers make products in this category that users can rely on more than once. They simply switch out the components that came in contact with liquid and continue using the other parts.
Making those quick and nearly seamless swaps allows manufacturing brands to maintain consistently high output in their plants. This pleases existing clients, and people thinking about doing business with a manufacturer feel more confident.
Instances may also arise where manufacturers want to make short-term production changes to see if those alterations raise output or help a company meet other productivity goals. Portable flow meters are likely the best options in such cases. Their clamp-on designs make them easy to install on equipment as needed.
Users can then get valuable flow data associated with new processes. That information could help them make more informed decisions about whether to make the different techniques permanent.
5. Sustainability Management
Many corporate leaders are thinking more seriously about sustainability. They realize that improvements in this area don’t just make a company look better to stakeholders. Such progress also makes good business sense because it can save money and prevent resource wastage.
Leaders have various avenues to pursue as they investigate the best ways to have a sustainable business. Their efforts could include using smart thermostats, installing LED bulbs and utilizing sensors that turn off the lights after certain periods of inactivity. Industries increasingly use electromagnetic flow meters to pinpoint water leaks, which also supports a sustainable business.
Many solutions on the market are highly accurate, providing ±0.4% or better uncertainty rates to help people feel confident in the results. That makes it easier for people to differentiate normal water usage from potential leaks.
Many modern flow meters have IoT connectivity to help people monitor statistics from anywhere. That ease of access reduces the chances that issues go unnoticed for too long, wasting money for a biopharmaceutical processing company and contributing to the unnecessary usage of a precious resource.
Use Flow Meters to Pursue Manufacturing Excellence
Biopharmaceutical processors who want to stand out in the field must have outstanding attention to detail and be responsive to unusual and unexpected events. People that use flow meters have more information to help them react correctly as things develop in their industrial facility. Such proactiveness is vital in biopharmaceuticals, particularly since many of the products created are lifesaving for the people who need them.
Emily Newton is an industrial journalist. She regularly covers stories for the utilities and energy sectors. Emily is also editor-in-chief of Revolutionized (revolutionized.com).