Water purification and reuse at a pulp and paper mill
The selected technology to obtain high-quality water for reuse was the High Efficiency Reverse Osmosis (HERO) process. This will produce a clean water stream (permeate) for reuse within the plant, and a concentrated brine (reject) containing the organics and total dissolved solids (TDS) present in the raw feed.
The HERO process pretreats water with a special ion exchange resin to remove hardness and metals. The water is then degassed to remove the alkalinity. After the hardness and alkalinity are removed, the pH of the water is increased above 9 and fed to a reverse osmosis unit. In conventional reverse osmosis systems, membranes foul with scale (divalent cation precipitates such as hardness, especially at high pH), organics (oil and hydrocarbons) and microbiological growth. The HERO process eliminates these problems by removing the divalent cations, and then operating the RO at a high pH where oils are emulsified and biological growth does not occur.
A HERO process bench test was performed at Hydrometrics' laboratory using filtered water from the client. Bench test objectives were focused on producing water containing a low TDS concentration, while operating the RO system at maximum recovery and flux. Recovery is the percentage of clean water recovered from the feed and flux is the gallons of permeate produced per square feet of membrane per day (gfd). Increasing the recovery reduces the volume of reject requiring evaporation or disposal. Increasing the flux results in lower capital costs and better effluent quality.
The objectives of using the HERO process to obtain high-quality water at high recovery were clearly met. Approximately 140 gallons of water was treated through reverse osmosis (RO), yielding 136 gallons of product water (permeate) and 4 gallons of waste water (reject) for a recovery of approximately 97 percent. Water quality results are shown in Table 1.
Hardness in the filtered water was removed in the HERO bench test using weak acid cation exchange resin. A more cost-effective method for removing high levels of hardness from large flows is addition of lime and soda ash. It is planned to implement lime-soda softening at the client's facility, then follow it with the HERO process.
All concentrations are in mg/L.
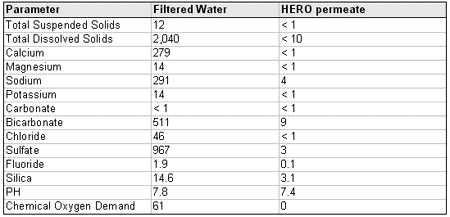
Hydrometrics evaluated lime-soda softening in bench-scale tests using untreated water (raw feed) from the client. These tests identified the most cost-effective conditions for lime-soda softening, and identified an effective coagulant dose. Water quality results from these tests are shown in Table 2. Nearly all of the hardness (calcium and magnesium) was removed and replaced with sodium.
All concentrations are in mg/L.
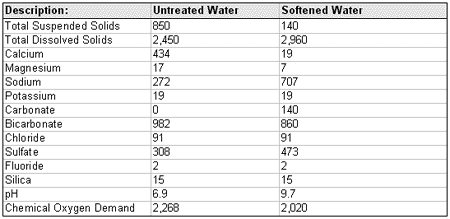
It is planned to implement the HERO process at this facility as shown below in Figure 1. Lime-soda softening will be added to the existing clarifier. Weak acid cation exchange will be used to remove residual hardness after lime-soda softening, followed by degassification and reverse osmosis. The high-quality RO permeate will be available for reuse within the plant.
To implement the water reuse option as quickly as possible, Hydrometrics has been contracted to:
- Design and oversee construction of a full-scale lime-soda softening addition onto the existing water treatment system. Design is currently underway.
- Assist with starting up the lime-soda softening system.
- Pilot-test the HERO process at the client's facility, using a side stream of approximately 15 gpm.
- After successful pilot testing, design and oversee construction of a full-scale HERO system.
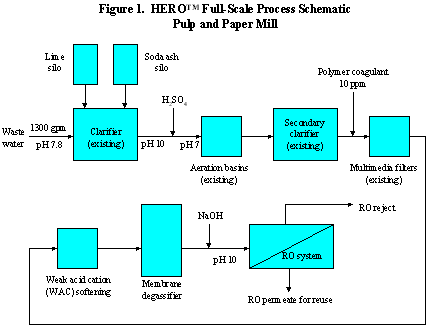
For more information on this system or application, visit the <%=company1%> storefront, or contact the company at 2727 Airport Road; Helena, MT 59601; Phone 406-443-4150.
Source: Hydrometrics Inc.
Subscribe to our free e-mail newsletter.