UVC LEDs For Biofilm Prevention
By Hari Venugopalan, Director of Global Product Management, Crystal IS
Biofilm has adverse effects on all types of instruments, sensors, and equipment used in power plants, food and beverage production plants, desalination facilities, paper mills, and marine environments. This includes growth on pipelines, tanks, heat exchangers, reverse osmosis (RO) membranes, and other equipment. Biofilms can cause reduction of heat transfer, increased pressure drop and corrosion of metallic surfaces, and many forms of contamination. In marine monitoring instruments, biofilm can affect the quality of measurements and significantly limit the length of deployment. Biofilms have also shown resilience to treatment, making it an ongoing challenge for industrial engineers and instrument designers. The productivity loss coupled with increased costs of equipment cleaning and replacement have made biofilm and biofouling prevention a serious problem across industries.
The process of biofilm formation begins with the attachment of a conditioning film on a surface followed by the initial microbial attachment. This progresses into an irreversible adhesion where the microbe cells become attached not only to the surface, but to each other to form a biofilm matrix. In favorable conditions, the biofilm growth will continue with some cells detaching over time. (Figure 1)
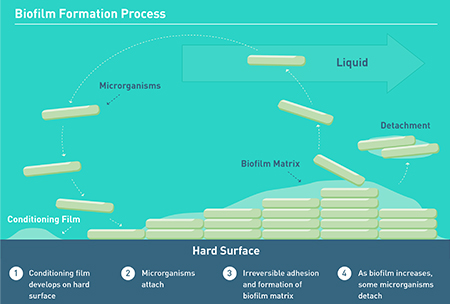
There are a variety of traditional means of biofilm prevention and control, including both chemical treatment and mechanical removal of films. The water treatment industry has traditionally relied on the use of chemicals to reduce microbial counts. Many protocols include the removal of loose debris with water followed by the use of chemical agents, rinsing, and disinfection. Mechanical methods have also been used in water treatment — including water turbulence and scrubbing — to free surfaces of microbial growth. However, these films are difficult to fully remove with these methods as the bacteria are not killed, and thus can redeposit in other locations in the system, possibly to reform a new biofilm matrix.
In the case of marine sensors used for environmental monitoring, the impact of biofilms leads to biofouling where larger, multi-cell organisms attach to the instrument. Instruments can be adversely affected by biofouling within a week of deployment. Instrument manufacturers traditionally use biocides and coatings to combat biofoul, however these are being regulated out due to their environmental impact. Mechanical options such as wipers, while effective, have a higher failure rate, need to be customized for each surface, and require precious power resources.
Because of the limitations and ineffectiveness of chemical and mechanical methods, as well as a desire to reduce costs, industries across the board are seeking alternative methods to prevent the formation of biofilm. One promising disinfection technology that may pose a solution, used for drinking water disinfection for decades, is UV irradiation.
How UV Irradiation Works
Many municipal water treatment plants use mercury lamps that emit in the UV wavelengths for disinfection. Light in the UVC wavelengths, from 250 to 280 nanometers (nm), deactivates bacteria, viruses, and other microbes by destroying the genetic information inside the DNA. UVC irradiation offers a better method than the existing biofilm prevention options as it is non-contact, non-chemical, and can be used on a variety of materials and surface geometries. UV light is effective in preventing biofilm formation by deactivating the DNA in microorganisms at the early stages of attachment to prevent the formation of a biofilm matrix.
Although the potential of UV irradiation for biofilm prevention has been known for some time, traditional UV lamps containing mercury are not a feasible option due to their bulk, fragility, high power consumption, and the toxic nature of mercury. These lamps are also difficult to operate in cold environments. LEDs that emit UVC light offer a more suitable solution that overcomes the limitations of mercury lamps. They consume less power, have a smaller footprint for more design flexibility, and high brightness in the necessary germicidal wavelengths. Additionally, as a solid-state light source, UVC LEDs can be operated with a duty cycle to maximize the disinfection while optimizing power consumption and lifetime.
The amount of UVC radiation needed to prevent biofilm on any given surface is referred to as the required UV dose. Some microorganisms are more susceptible than others to UVC radiation and require less exposure, while others require more light for complete deactivation. The effective UV dose is comprised of two factors — the intensity of the light and the length of exposure time. Industrial engineers and instrument designers use the relationship between these two parameters to develop an effective system. The following example illustrates the design parameters to prevent biofilm formation with UVC LEDs on a flat two-dimensional surface that is 10 mm x 10 mm.
The intensity distribution on the surface depends on the distance between the UVC LED and the surface to be irradiated, the light output of the LED, and the light emission pattern. Figure 2a shows the light intensity distribution on a surface at a distance of 10 mm from a UVC LED emitting 2.5 milliwatts (mW) in a radiation pattern of 100 degrees. As LEDs are point sources, the intensity on the surface is highest directly below the center of the LED and steeply drops off as the distance from the center increases (Figure 2b).
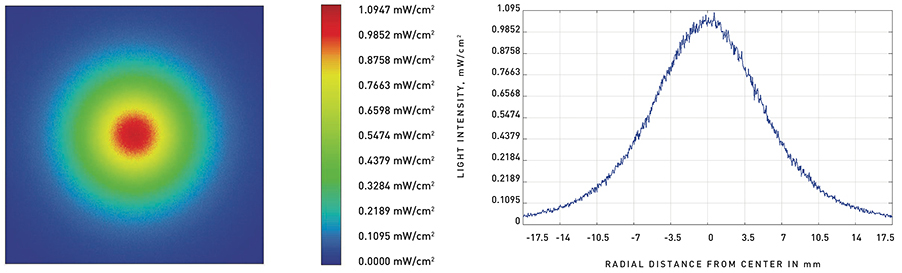
This relationship between the light intensity and distance from the center is also shown in Table 1. The table compares data for two different distances from the light source to the surface. For the LED located at 10 mm from the surface, the minimum UV intensity at the edge of the surface (i.e., at 10 mm from the center) is 0.20 mW/cm2.
|
Distance from center (x) for a 10 mm x 10 mm surface |
||
Distance from LED to surface |
0 mm |
5 mm |
10 mm |
10 mm |
1.09 mW/cm2 |
0.60 mW/cm2 |
0.20 mW/cm2 |
20 mm |
0.30 mW/cm2 |
0.22 mW/cm2 |
0.17 mW/cm2 |
Numerous microbial studies indicate that a reasonable minimum UV dose for prevention of bacteria accumulation on a surface is 40 millijoules (mJ)/cm2. As dosage is a function of intensity multiplied by time, the calculated minimum required time for UV irradiation in the above example would be 200 seconds, or approximately 3 minutes. This amount of irradiation would be needed periodically as water flows across the 10 mm x 10 mm surface. If this target area for prevention were increased, the system would require longer exposure times and/or the use of multiple LEDs for protection.
The problem of biofilms and biofouling is a vast one — overall the cost to industry has been estimated at $200 billion in the U.S. alone. With environmental regulations doing away with biocides and the relative ineffectiveness of other mechanical methods, the industry is investigating new, more effective methods of prevention. The small footprint and high brightness of UVC LEDs enables use in a variety of industrial applications. By controlling biofilm growth, UVC LEDs allow manufacturers to reduce operation and maintenance costs and increase the productivity of industrial systems.