Understanding The Dynamics Of Reverse Osmosis: Fluctuations In Flow, Rejection, And Pressure

By Harold Fravel, executive director, American Membrane Technology Association
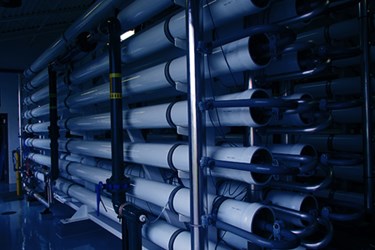
What you don’t know about your reverse osmosis membrane feedwater may surprise you — and hurt your system’s performance.
By Harold Fravel Jr., executive director, AMTA and Karen Lindsey, executive member, AMTA board, VP and co-founder, Avista Technologies
A well-designed reverse osmosis (RO) system is truly an innovative marvel, expected to produce a consistent water quality and quantity under feed conditions that may be in constant flux. Innovative technical developments continue to benefit the industry with improvements in RO membrane elements, system design, energy recovery, and specialty chemicals, which have all contributed to the global acceptance and widespread use of membrane systems for water treatment.
The RO process requires pressure to drive incoming feedwater through a membrane barrier layer to produce a higher-quality permeate. The semipermeable membrane allows water molecules to pass through while rejecting dissolved ions present in the stream. The percentage of rejection of these ions varies, with some membranes rejecting sodium at more than 99 percent but boron at only 60 percent. Constituents rejected by the membrane remain in the stream that then feeds the next element in the series. At the same time, a volume of permeate water has been removed from the feed, further adding to the concentration factor. These two actions combine to produce feedwater that becomes more and more concentrated as it passes through the membrane series.
In spiral-wound elements, the permeate water is collected in a central product water tube. A pressure vessel typically contains 3 to 7 RO elements in series, connected via these product tubes where the permeate produced by each element is blended. The quality profile of this blended permeate will vary based on the sample collection point.
Overlooked O&M Considerations
The interesting caveat in predicting RO system performance and membrane cleaning cycles is that we typically rely on an ion analysis of the source feedwater. However, this analysis only truly reflects the quality of water that will feed the first membrane in the series. As soon as the feedwater passes through that initial element, ions have become concentrated, and the permeate volume has been removed. So the next elements in the series may be fed with a water quality much different from that of the initial source.
Meanwhile, the osmotic pressure of the feedwater is also changing throughout the RO process, as it’s directly related to the concentration of dissolved ions present in the water. As permeate water is removed from the feed volume, the salts become more and more concentrated, with a corresponding increase in the osmotic pressure. As a result, the pressure necessary to force water through subsequent membranes must be increased to overcome the increasing osmotic pressure.
In addition to osmotic pressure, the RO system must overcome pressure losses resulting from the various barriers in the element construction, including the feed channel spacer (vexar), the membrane surface area, and any other restrictions in the flow path. In a pressure vessel housing multiple membranes, the lead element is subject to the initial design pressure, but subsequent membranes must overcome the incremental loss of pressure resulting from these barriers.
Design For Feedwater Variation
A well-designed RO system must address continual variations in ionic concentration and feed pressure in order to meet expectations in permeate volume and quality. Salt passage through a membrane barrier layer is constant and is not influenced by pressure. But it is related to the salt concentration in the feed and is also proportional to permeate flow, meaning that salt rejection increases with permeate flow and, conversely, decreases as the permeate flow decreases. This means that downstream elements will have a slightly higher salt passage than the preceding elements, since the feed is more concentrated as permeate is removed. Likewise, since the volume and pressure of feed to the downstream elements are lower, the membranes will produce less permeate.
The feed volume, concentration, and driving pressure of the last element in a vessel can be very different from the conditions addressed by the lead element. Pressure drop within a pressure vessel can be as high as 60 psi (4 bar), and the amount of water fed to the last element can be half the volume fed to the first element in the series.
Fortunately, there is now a wide range of RO system design software available that combines complex calculations with decades of process knowledge to help predict and interpret RO system performance. Operators who understand the complex operational fundamentals of RO systems will be better prepared to interpret the output of these specialty programs and effectively address performance issues.
About The Authors
Harold Fravel Jr. accepted the position of executive director for the American Membrane Technology Association (AMTA) after working for Dow Chemical/ FilmTec Corp. for 36 years. Fravel has a Ph.D. in organic chemistry from the University of North Carolina and a B.S. in chemistry from Florida State University.
Karen Lindsey is an executive member of the AMTA board of directors. She is the VP and co-founder of Avista Technologies and has 30 years of experience in the water treatment industry, working with companies that cast cellulose acetate membrane, produce polyamide elements, and formulate specialty chemicals.