Treatment Plant Operator Training
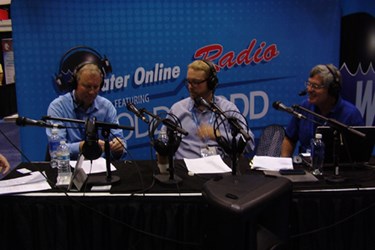
Steve Walker, Principal Operations Specialist and Jeff Berlin, Senior Project Engineer with Carollo, discuss their WEFTEC presentation “Lessons Learned From Training Today’s Operator: Perspectives For The Engineer.”
The following is an excerpt from a Q&A with Water Online Radio. Click on the Radio Player above to hear the full interview.
Water Online Radio: Why do I need more trained people if I can automate?
Steve: Automation can only operate something when the electricity is on. There's many times when there's a power outage. There might be an instrument problem. There might be something in there that a human being must analyze and evaluate, make an assessment, make a decision, and then implement that change to make sure that the water quality matches the permanent standards that are being established by the EPA.
If you miss on a permit standard, it can cost you up to $37,500 per occurrence. The human element is the one that makes sure that the automation is truly doing its job and coming in and making that response when that is needed. On top of that, instruments and equipment must be maintained to be able to do the work that you're expecting out of that automation.
If the human being that used to be just an equipment operator becomes more of a process evaluator, where he's evaluating what's going on, trying to make sense of the data, trying to make sure his equipment and his instrumentation are continuing to be maintained, he’s going to have a reliable product with a reliable output from that plant.
Water Online Radio: Jeff, I have a two-part question. Having interacted and dealt with all these operators, what knowledge gaps need to be filled? And two, virtually everybody we've sat down with on this show has said, “Well, I've been in the industry for 25 – 35 years.” They're pretty set in their ways. “What kind of thinking do we need to change?”
Jeff: Yes. You have two issues. We have a lot of broader perspectives that are necessary today. We have new technology and tighter permit limits. And we have a workforce that came into the industry, similar to Steve in the late 70s, early 80s, that came into the industry from a mechanical aptitude background. Keeping equipment operational and running, that's their forte. We certainly have a demand for that and a need for that in our industry.
At the same time, if you're operating a more complicated process, and you're trying to keep biology serving the very tight limits that we need to meet, there is this process control and instrumentation understanding that Steve spoke of earlier. You need to train these technology students, who have this understanding of, “I'm used to looking at data. I'm used to evaluating information at the tips of my fingers every day,” to help them understand what it is that wastewater treatment is and how do they keep the process operational?
Water Online Radio: I'd like to pose this question to each of you individually, and I'll start with you Jeff. If you were king, what's the one thing that you would change first, to change the whole training process for operators?
Jeff: The first thing I would do is focus on the trainers. The folks who are giving this training. Engineers need to understand that we're speaking to experienced adults, and use some of these approaches that are the way to communicate with an experienced adult.
Make sure that we provide them with a clear purpose, and define the context of what they're speaking and talking about. Relate what we're training to their daily usage of this information, and then really encourage participation and have more participatory training, so that it increases the retention of what we're conveying.
That's about how to train. At the same time, we have an industry that tends to just train on, “Hey, we have this information. Let's just convey it,” but we need to focus more on the direct and immediate needs that the operations staff need, and respond to what they need and provide it.
Water Online Radio: Steve, same question for you. Let's make you king now.
Steve: Where I see training going – and Jeff alluded to it – we've got adults. They want to know what they need to know to make themselves successful in this job. They want to know how to apply it, but I look at it in a slightly different way. The iPad came around in 2010. It's been online for about three years now.
Gaming systems have been out there since the early 80s. Let's use those technologies to integrate this young modern worker that grew up with these things in his hands, and let's figure out how to apply them to the training environment. For instance, I could build a developmental console of the treatment process that we're working.
They could play with it offline and understand how to optimize that system without interfering with the actual process. I learn offline, I make these adjustments, I can make these improvements in our process and save this kind of money.
Then I can apply those lessons that I've learned offline to the real process, without interrupting, without interfering it, without threatening our discharge permits. If I can use that technology to help the operator understand the treatment plan he's operating, we've helped our rate payers, we've helped the environment.
We also have now engaged that person into, “Gee, this is just like what I do at home in my spare time. I'm doing it at work now.” It's just a natural transition for these people into the workforce of the future. While I’m babbling along here, these technologies are growing really, really fast.
Jeff and I have spent an awful lot of time trying to figure out how we can integrate what we're doing into these technologies, and we continue to do it. But I truly think that utilizing this electronic media to do our training, to retain that training, to make it readily available to anybody at any time is one of the keys to moving forward successfully…
Click on the Radio Player above to hear the full interview.