4 Treatment Plant Budget Busters To Avoid
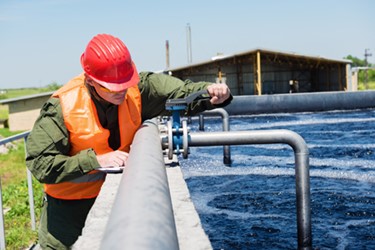
Municipalities work diligently to produce quality drinking water and meet strict wastewater treatment regulatory standards while judiciously managing expenses. Despite the efforts, many of their plants have operational weaknesses where money is quietly being lost.
Water managers may have limited resources to meet every challenge, so getting a handle on these issues is important to the municipality.
Advanced technologies provide an opportunity for utilities to gather actionable information and strategically offset deficiencies. Here are four applications that offer the potential for significant savings when factored over multiple years.
Pay Less For Power
Large blowers used to aerate the massive aeration basins at wastewater treatment facilities — and drive the biological process — can account for as much as 60 percent of a plant’s energy costs. The rate at which those blowers run is typically linked to what has been determined as the ideal level for dissolved oxygen (DO) in the basins.
It is possible to reduce blower usage, and cut energy costs, by adding a sensor and transmitter that monitors ammonium and nitrate levels in addition to the DO transmitter. Process engineers and operators can then work together using the data to fine-tune the DO levels in the basins, taking them as low as possible, while still maintaining optimal nitrification and denitrification.
To illustrate the business case to stakeholders, consider the following example: It would cost a midsize wastewater plant (5 MGD) with two basins about $25,000 to purchase and install the new hardware. If that allows the plant to shave 7 percent off a $130,000 annual electric bill, the investment will pay for itself in less than three years. Additionally, the improved process control means the municipality will likely produce a higher-quality effluent.
Trim Waste In Chemical Dosing
Inaccurate chemical dosing at both water treatment and wastewater treatment plants can impact quality and compliance goals while posing a significant drain on financial resources.
For example, a wastewater plant that should be injecting 400 gallons of chlorine per day into effluent, but actually adds 430 gallons daily because of an inaccurate flow meter, will waste nearly 11,000 gallons of the chemical over the course of a year.
Meters that are highly accurate and repeatable over the long term — such as Endress+Hauser electromagnetic or Coriolis flow meters, which contain no moving parts to degrade — would help water managers avoid inaccurate dosing problems. However, water managers may shy away from these meters because they are costlier than the paddle wheel or turbine products typically used for dosing applications.
A true cost comparison of the technologies would account for losses resulting from the less expensive meters that drift from their original settings. Significant operational savings could more than offset the capital costs over time.
Reverse Water Loss
The production of clean and safe drinking water comes with a significant cost, but virtually every municipality is spending more than necessary because of leaks in aging infrastructure.
Ideally, plant operators would know how much source water they are drawing, which should match the volume being pumped into the distribution system and then billed to consumers. However, the lack of highly accurate flow meters at strategic points makes it nearly impossible to balance out that equation.
Progressive municipalities are getting a better handle on water losses — also known as non-revenue water, or NRW — by strategically placing flow meters across the process for continuous monitoring. This makes it much easier to search for, and fix, leaks in the system.
While the addition of flow meters can represent a significant capital investment, the long-term payoff comes from a combination of lower production costs and a better ability to plan for growth. When less finished water is wasted, less source water is needed.
The bottom line is that ensuring that every drop of water leaving the treatment plant is paid for is critical to the fiscal health of every utility.
Reduce Unnecessary Calibrations
Traditionally, a significant amount of labor in water operations has gone toward sending technicians to check instruments as well as perform verifications and calibrations. As some operations grow to hundreds of instruments, staying on top of those preventative maintenance tasks can be overwhelming.
The good news is that the tools are getting better and smarter, so there’s no need to inspect or service instruments simply because a certain amount of time has passed. Advanced instruments feature onboard diagnostics that can tell users when they are drifting out of range. For example, Endress+Hauser equipment includes Heartbeat Technology.
By relying on the data, and only servicing instruments when necessary, water managers can free up large blocks of labor for better use.