10 Tips To Save Energy On Pumping Systems

By Kevin Westerling,
@KevinOnWater
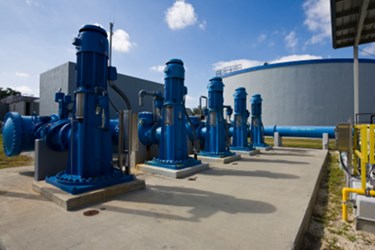
Whatever your business in water, if you’re moving it, you need pumps. Unfortunately, at 8.34 pounds per gallon (and 62.4 pounds per cubic foot), water is not so easily moved. To do so requires tremendous energy. According to the U.S. Department of Energy (DOE), 16 percent of a typical facility’s electricity costs are for its pumping systems. Moreover, the Water Research Foundation states that pumps for drinking water systems, in particular, account for up to 80 percent of the total energy required for treatment and distribution.
The organization that is perhaps most equipped to talk about pumps and energy is the Hydraulic Institute (HI), which specializes in pump-system energy management and performance optimization. HI’s 501(c)3 educational subsidiary, Pump Systems Matter (PSM), delivers training on these topics via webinars and live, in-person courses.
To get a quick course on lessening the energy burden of pumps, I contacted HI’s technical director, Gregg Romanyshyn, who shared with me HI’s “10 Ways To Save Energy” — so recently updated that they have yet to be published by the organization itself. They appear here, as follows, with full credit (and thanks) to HI for the exclusive preview.
“10 Ways To Save Energy”
- Select the most efficient pump type for the application
A Finnish research study shows that the average pump efficiency is below 40 percent and that 10 percent of pumps are 10 percent efficient or less. Oversizing often comes in the design phase, since the practice for adding multiple safety factors is quite common. This means that both pressure and flow parameters for the pump design may be 25 percent more than the actual system operation. The specifying engineer may need to work closely with the pump manufacturer or distributor to optimally select the pump, in addition to its size, speed, power requirements, and type of drive, as well as the mechanical seal and ancillary equipment.
- Right-size the pump
Right-sizing the pump represents a significant economic opportunity to reduce energy consumption. This is important because centrifugal pumps can consume up to 60 percent of motor energy in a facility, and also have the highest process equipment maintenance cost. When engineers add too much of a safety factor during the design phase, the pump can be oversized, resulting in higher energy and maintenance costs.
- Trim the impeller
The impeller should not be trimmed any smaller than the minimum diameter shown on the manufacturer’s pump curve. This is typically about 75 percent of a pump’s maximum impeller diameter. Pump curves and affinity rules (which are valid for a maximum of approximately 5 percent change in diameter) can both provide information on impeller trim changes and the affected performance. In practice, impeller trimming is typically used to avoid throttling losses associated with control valves.
- Minimize system pressure drop
A key way to reduce pressure drop is through pipe-sizing optimization. Hydraulic friction loss creates a reduction in pressure from one end of a straight pipe to another. Factors such as the flow rate, pipe size (diameter), overall pipe length, pipe characteristics (surface roughness, material, etc.), and properties of the fluid being pumped all influence the system pressure drop.
- Implement proper control valves
Control valves are typically used to control flow and/or pressure. They can help to reduce energy losses over non-controlled systems such as irrigation systems with a fixed-speed pump and multiple locations with different distances and elevations. The main functions of control valves are throttling flow or for bypassing flow. Throttling reduces the flow but increases the pressure. You can minimize excess pressure by bypassing excess flow back to the reservoir or another location.
- Implement variable speed drives (VSDs)
Drivers are used for either fixed-speed or variable-speed operation. For many applications, you can save energy by implementing variable speed drives. With a variable speed drive, the rotational speed of the pump is adjusted to achieve the desired head and flow necessary for the process application. A VSD can often be added to an existing pump motor system to slow the pump down to meet the actual requirements verses the theoretical requirements that were calculated at the start of the project. Once installed, the VSD can accommodate changing system demands, including many potential future expansion plans. This method often results in the highest energy efficiency with lowest life cycle costs.
- Maintain pumping systems effectively
Effective pump maintenance allows facilities to keep their pumps operating efficiently. Regular maintenance may reveal deteriorations in efficiency and capacity, which can occur long before a pump fails. Wear ring and rotor erosion, for example, can be costly problems that reduce efficiency by 10 percent or more. Most maintenance activities can be classified as either preventive or predictive. Preventive maintenance addresses routine system needs such as lubrication, periodic adjustments, and removal of contaminants. Predictive maintenance focuses on tests and inspections that detect deteriorating conditions. Sometimes called “condition assessment” or “condition monitoring,” it has become easier to conduct with modern testing methods and equipment. This can help minimize unplanned equipment outages, which can be very costly.
- Use higher efficiency/proper pump seals
Sealing systems impact efficiency, and mechanical friction losses are only the beginning. Leaks from static and dynamic seals waste fluid and can contaminate the environment. Leaks between the pump suction to the pump discharge reduce pump volumetric efficiency. Dynamic seals consume energy from the mechanical friction between the static and moving parts. Potential sealing system savings can exceed the energy savings obtained from switching to variable frequency drives, trimming impellers, or re-sizing pumps in many applications.
- Use multiple pumps
When multiple pumps operate as part of a parallel pumping system, there are opportunities for significant energy savings. A multiple pump parallel system works best when each pump is run individually, not concurrently, most or all of the time. Running multiple pumps simultaneously is appropriate as dictated by the flow requirements specific to the application and duty cycle.
- Eliminate unnecessary uses
One of the most simple, but often overlooked, measures to save energy is to eliminate unnecessary use. Pumping system efficiency measures include shutting down unnecessary pumps and using pressure switches to control the number of pumps in service when flow-rate requirements vary. Each pump system is different and there are many opportunities to save energy. Don’t forget to look for the obvious.
For more information from the Hydraulic Institute, including pump standards, best practices, and events, visit www.Pumps.org. For educational and training information, visit www.PumpSystemsMatter.org.
What energy-saving tips or trade secrets can you offer to save energy and/or money on pumps? Can you vouch for the effectiveness of HI’s recommendations? Help your peers by sharing your knowledge and experience in the comments section below…