The Value Of Continuous Instrumentation To The Operator & Why Manufacturers Should Listen To Their Needs
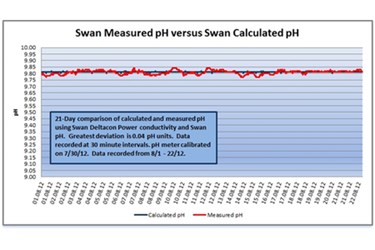
By Randy C. Turner, Technical Director, Swan Analytical USA
When I began my career as a power plant chemist most continuous analyzers were trending devices at best. Conductivity was the most reliable analyzer and the temperature compensation algorithms were marginal. Sample conditioning with respect to sample temperature control was not very good as well. Therefore chemistry control was primarily based on manual bench testing. This lead to extended periods of time when the chemistry was not monitored and control was not optimal. In the 1990’s continuous analyzers became much more accurate and reliable. Conductivity temperature compensation algorithms became much more accurate. This allowed the operator to rely on the analyzers to monitor and control their processes. Operators often provide feedback to analyzer manufacturer’s regarding the features they want such as easy grab sample analysis capability, accuracy, and reliability. During the design and development of continuous analyzers manufacturers often incorporate operator feedback into their designs to varying degrees.
Get unlimited access to:
Enter your credentials below to log in. Not yet a member of Water Online? Subscribe today.