WWEMA Window: The Retrofit Challenge — A New Solution To An Old And Growing Problem
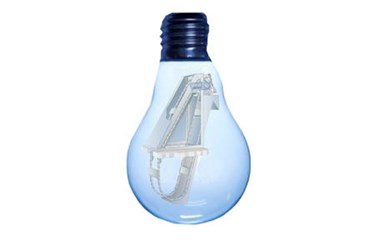
By Michelle McNish, president, E&I Corporation
A major challenge for contractors and equipment suppliers with projects that involve retrofitting existing concrete with new equipment in water and wastewater treatment plants involves the confirmation of existing concrete configurations and dimensions.
Treatment plants for the most part use concrete tanks, structures, or channels for unit processes. The interface between the concrete and the equipment is critical as there may be very little adjustment of the equipment possible to account for variations in the concrete — for example, a catenary bar screen constructed to a specific dimension to fit in a concrete channel. The walls of the channel must be true and consistent with the bar rack and dead plate. Clarifiers exhibit similar issues regarding existing elevations and the degree to which the tanks are true to the given dimensions indicated in bid documents.
Most treatment plant work now involves replacement of equipment in existing concrete. As with all projects, equipment suppliers and the installing contractor must work to a fixed completion date in order to complete the project on time.
Prior to bid, the equipment supplier’s only choice is to base the price and schedule for the equipment on the limited dimensional information for the existing concrete provided within the project bid documents. This presents an interface issue. The installing contractor is not responsible for the condition of the existing concrete, which may have dimensions or configurations that vary considerably from the general dimensions indicated in the bid documents, and the equipment supplier cannot know beforehand what variations if any exist. Ultimately the issue is: Who is responsible for dimensional compatibility between the new equipment to be fabricated and the existing structures?
Certainly all parties involved in the project have an interest in making sure the equipment is sized for the existing tankage prior to fabrication, because once fabricated, very limited adjustment of the equipment is possible.
Project specifications may state that the contractor must provide equipment suppliers with verified concrete dimensions prior to the submittal, or in some cases may be silent on the issue of existing concrete dimensions, or may even leave it up to the equipment supplier to verify existing dimensions. However, since the contractor is not known at the time of bid, the verification process cannot take place until after the prices and schedules have been committed to and without consideration for potential costly revisions if problems are found with dimensional variations in the existing concrete.
The process of obtaining verified concrete dimensions after a contract is awarded is a common source of delay in the schedule for both equipment suppliers and the installing contractor. The usual problem is restricted access to the tanks that must be surveyed. This creates a situation in which the equipment supplier and the contractor have committed to a schedule but neither can proceed because the critical dimensions of the existing tanks cannot be verified. The equipment supplier could proceed to fabricate equipment based on the general dimensions stated in the project specifications; however, there will be a question of responsibility if it is later discovered that there are flat areas of tank walls or floor slopes and other elevations are not what they should be, all of which could result in equipment that does not fit with the existing structure.
The problem is further complicated when new mechanisms are specified for multiple tanks that are described with identical general dimensions (diameter, length, width, depth, floor slope, etc.). The total price for the multiple and presumably identical mechanisms is based on the risky assumption that each tank is identical to any of the others. The price and schedule given by the equipment supplier does not include the additional costs and possible extension to the schedule if, upon verification of the actual tank dimensions, there are variances that result in dimensionally unique sets of equipment for tanks that are only of similar size. As equipment suppliers, we have encountered this problem numerous times, at great cost and disappointment to all involved in the project.
A new solution to the old and growing problem of new equipment being installed into existing concrete channels or tanks is the idea that verification of dimensions could be completed prior to bid and included in bid documents so that costs and schedules can be more accurately established by both suppliers and installers.
Michelle McNish is President of E&I Corporation, a Division of McNish Corporation, and is a member of the Board of Directors of the Water and Wastewater Equipment Manufacturers Association.