The Contractor's Song: Communication Breakdown — Managing Project Data During Construction
By Jeremy Holland
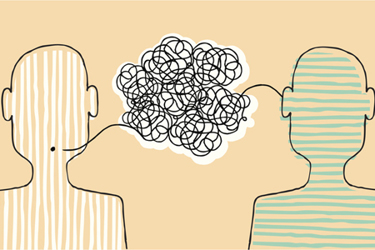
“Communication breakdown
It's always the same
Having a nervous breakdown
Drive me insane”
- Led Zeppelin
I’ve been playing Wordle recently and sharing results with various family members on our group text. It’s been interesting and funny to look at the green, yellow, and black (or grey? Why are they different?!?) squares and try to imagine another’s thought process and make guesses as to what words were chosen leading up to the successful outcome. Just last week my son and I had a revelation that we started with the same word for an initial guess, and we both guessed correctly on the second try. Great minds think alike; heaven help him if that’s the case!
That experience of guessing what others are thinking when it comes to Wordle reminded me of communication successes and failures (breakdowns) that happen in all water infrastructure construction projects. It reinforced for me how important it is to clearly document decisions and project history so that it is easy to understand why decisions were made and the history, assumptions, and agreements that went into those decisions. It is also important to store that information in a location and format that allows for easy access so that if something comes up that could impact the project based on a past decision, there is a clear history that all parties can rely upon for how to handle the impact.
As far as documentation is concerned, there are many different tools that exist in construction. Whether it is through submittals, requests for information, meeting minutes, work change directives, or change orders, there are a variety of ways that information about the project gets communicated. The same goes for design, where technical memos, basis of design reports, design document milestones, construction documents, addendum, and conformed documents are part of the routine. Another tool that bridges the gap between design and construction that we use on all our projects is a risk register. A risk register allows the project team to track any item that might be a risk to the project, allocate that risk to the team member best suited to manage that risk, identify the impact of the risk, and how to mitigate or accept the risk. We use the risk register as a communication tool that allows us to identify issues early in a project and provides appropriate attention to the risk so that it is minimized. Ultimately, it is the goal of everyone involved to identify, plan for, manage, and minimize risk, so having a visual and living document that everyone can access and understand is critical to achieving success.
In addition to what we use for communication, there is also the topic of where we keep that communication record. There are many tools available in construction these days that allow contractors, engineers, and owners to collaborate, store, and access project documentation. At Mortenson, we use Procore, and it is an invaluable tool for managing project documentation. I’ve also used in my career several other web-based document management tools, such as e-Builder, EADOC, ProjectWise, and others. Each has strengths and weaknesses and associated fans and critics. I’m not here to offer up an endorsement of one over the other, but the key is that the project documentation is readily available, easy to organize, searchable, and the interface is intuitive to use.
Another big benefit of a well-organized documentation platform is the reality that there is a steady transition of employment on projects. Across the board, there is increased mobility in owners, engineers, and contractors. Having good documentation allows for new team members to get up to speed on projects quickly and have access to that historical record so that they understand not just what we are doing on a project, but also understand why, even if they weren’t involved in the original decision.
As an example of the benefit of that historical record, a few years ago I was working on resolving an issue at a facility that had some problems with water pressure to a piece of equipment. The owner was concerned that water demands were not correctly accounted for in the design, and the supply system was not adequate for the equipment needs. Having good records, we were able to track down the submittals and the technical specifications of the equipment installed to verify its operating requirements, particularly water demand. By having that information readily available and easy to find, we were able to confirm that the water provided to the equipment was adequate but that the control of the equipment was not set up correctly such that more than one component was calling for water at the same time. Once that was fixed, the existing supply system functioned correctly, and the facility was able to resolve its issues.
Jeremy Holland is a Market Executive in the Water Infrastructure Market in Mortenson Seattle’s Operating Group. With 23 years of engineering experience, Jeremy has served as project principal, technical advisor, project manager, and design engineer. His industry knowledge spans a wide variety of projects, clients, disciplines, and engineering problems. A licensed Professional Engineer in Oregon, WA, and Puerto Rico, Jeremy received a Bachelor of Science in Chemical Engineering and a Bachelor of Arts in English from the University of Notre Dame, and a master’s degree in Business Administration from Portland State University. He is a board member of the Oregon Association of Clean Water Agencies and is the Co-Chair of the Water Quality Committee.