Taking Care Of Morgan City – With New Lakeside Headworks Package
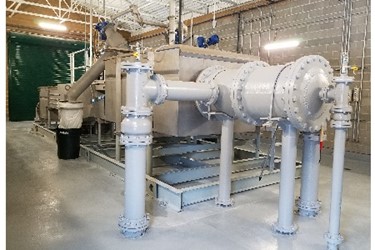
The need to upgrade an aging lagoon system in Utah has presented a growing community with an ideal opening to futureproof its wastewater treatment plant.
For Morgan City, settled in 1868 and built on pioneer dreams approximately 50 miles northeast of Salt Lake City, its four hard-working lagoons – created a century later – finally asked for some respite when they went septic in 2015.
The City had already been looking long and hard at designs for mechanical treatment systems prior to a dredging operation that saw over seven million gallons of sludge pumped out of the laden lagoons.
“Naturally, we needed to comply with existing regulations”, said Morgan City’s Senior Water/Wastewater Operator, Jamie Grandpre, “but we also wanted to accommodate anticipated growth. This included compliance with the Phosphorus Rule, which was enacted by Utah Division of Water Quality (DWQ) in 2015”
The Phosphorus Rule implements technology-based phosphorus effluent limits (TBPEL) for mechanical treatment facilities (TP < 1mg/l) and a nutrient load cap for discharging lagoons.
Jamie, who has worked at Morgan City’s treatment plant for more than decade, added: “We anticipate that our lagoons will exceed their phosphorus load in approximately five years, so when we were weighing up the options for mechanical treatment systems, we decided to work with J-U-B Engineers to move forward with a phased solution”.
‘Long-lasting mechanical fine screen and grit removal system’
As well as helping the lagoons (450’ by 250’) maintain compliance for the Utah Pollutant Discharge Elimination System (UPDES) permit, Morgan City would also be prepared for a future Phase 2 nutrient removal project. All improvements implemented in Phase 1 are to set to be utilized in Phase 2.
Gary Vance, Project Engineer at J-U-B takes up the story:
“We agreed that we needed a long-lasting mechanical fine screen and grit removal system, so joined forces in doing our homework and visiting other wastewater treatment facilities in
Utah to speak to operators. Jamie is one in a team of just three at Morgan City, so they have a huge responsibility and workload in looking after the wastewater as well as the water supply. Finding reliable, low maintenance equipment that can truly stand the test of time is a must”.
Jamie Grandpre added: “Along the way we’d heard some horror stories about lengthy downtimes, plus lack of back-up – and in the end, narrowed down our choice to a list of four manufacturers”.
Lowest bid didn’t win.
The system procured by the City and assigned to the contractor for installation was an all stainless-steel, corrosion-resistant, complete headworks package from Lakeside Equipment Corporation of Illinois (via its representative in Utah, Goble Sampson).
This compact Headworks Packaged System (H-PAC) combines Lakeside’s 6mm Raptor mechanical fine screen with a bypass bar rack, plus its SpiraGrit Vortex Grit Chamber in an elevated pre-engineered headworks system (that reduces engineering costs). The system was provided with tanks for the screen and grit removal, as well as platforms and a trough to connect the two.
The headworks was deliberately oversized to accommodate a peak hour flow of 4.0 MGD, which exceeds the anticipated 20-year peak hour flow rate of 1.986 MGD. There are two lift stations feeding the headworks, each having two pumps. The design basis for this higher flow rate was based on the need to be able to accommodate the absolute worst-case scenario of all four pumps operating simultaneously. It is highly unlikely that this would ever occur, unless there was very severe flooding. Generally, the flows are expected to be far less than four MGD.
Lift-station pumps at the City’s New Island Road discharge 700 gpm, whilst the existing Northwest lift-station pumps discharge 632 gpm. Lower flows and less frequent cycling are set to extend the operational life of the headworks equipment. In addition, the added cost to accommodate the higher flow rate of four MGD was minimal.
The temperature-controlled headworks/administration building, which provides considerable protection against the elements, includes the screening and grit removal room, storage room, motor control center (MCC) room (sized for potential future mechanical facility including conduit stubs), office/control room, laboratory (sized for potential future mechanical facility), bathroom, and mechanical/janitor room.
Since its installation, Lakeside’s Raptor Fine Screen has been busy removing inorganic solids that would otherwise head straight to Morgan City’s lagoons. The screen’s high removal efficiency and low head-loss is achieved with a unique inclined cylindrical screenings basket design that has varied screen bar heights. The screen’s rotating rake teeth fully penetrate the screen bars to positively remove captured debris and prevent grease from blinding or plugging the screenings basket. The heavy-duty design provides durability and long life in the most severe conditions. Captured screenings are compacted, dewatered and washed free of most organics to approximately 40 percent solids. Volume is reduced by 50 percent and weight by 67 percent, thereby reducing disposal cost.
Operating over a wide range of daily flow rates, the high-performance Lakeside SpiraGrit Vortex Removal System effectively removes inorganic grit from treatment plant influent in a mechanically induced vortex environment. Rotating paddles maintain the flow velocity in the vortex chamber, keeping organics in suspension while allowing heavier grit to settle to the chamber floor. This settled grit is moved across the stationary floor plate toward the center opening and into the lower grit hopper – and then removed from the lower hopper by an air lift or recessed impeller pump to a Grit Classifier.
‘We couldn’t believe how much grit was being collected’
Jamie Grandpre continued: “We’ve really grown in the past year – and this investment has brought about a considerable positive change for the plant. Collecting all the garbage and grit before it goes to the lagoons has made them so much cleaner. We now have more capacity, whereas before you could see the build-up of scum in the corners.
“Locally, we have an industrial park with some small-scale manufacturing, but immediately after the Lakeside installation, we couldn’t believe how much grit was being collected – that previously would have gone into our lagoons.
“Upstream we have a dairy, which due to the washing down of their floors – straight to sewer, was, upon investigation, causing us a major issue. We were also receiving silage, which was far worse than just normal grit – but now with such a strong and reliable screen and grit removal system, the negative impact on the plant has been solved”.
He concluded: “We haven’t had any issues at all with the Lakeside equipment. It is very easy to maintain and allows us to get on with our job of taking care of Morgan City”.
For more information,visit www.lakeside-equipment.com
Source: Lakeside Equipment Corporation