Tackling 'Flushable' Wipes The Intelligent Way
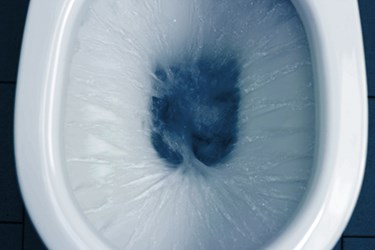
Wet wipes labeled as “flushable” create costly pump clogs and time wasted for collection system operators. But the problem can be resolved before it starts.
By Graham McIvor, founder, Clearwater Controls Ltd
Most utilities believe that the problem of wet wipes building up on the pump impellers can only be tackled by mechanical means. This may be through adding cutter pumps or screens, or by changing impeller types. These methods can come with high capital expenditure or operational costs but can be a great fix if a full rag ball hits the cutters and is chopped perfectly. However, as the blades dull over time, the wipes may get caught between cutting surfaces — like trying to cut a wet wipe with a blunt pair of scissors. The chopping effect can also shred the wipes so small that they pass through the inlet screens at the treatment works and affect the treatment process.
Get Smart
There are new, intelligent ways to tackle the wipes issue without having to change pump type. These may be in the form of new variable-frequency drives (VFDs) or smaller, purpose-built intelligent controllers. VFDs tend to perform pump reversals on a time basis, while intelligent controllers do it when the blockage reaches a certain level. The latter is much more successful — however, the key to using this type of technology is not only in the reversal but also in the detection method (everyone knows reversing a “tripped,” or fully blocked, pump can sometimes dislodge the rag ball). Detecting the blockage early enough will always dislodge it. With that in mind, perhaps it’s best to first look at and understand how blockages form in wastewater pumps.
Running ragged: Clogged pumps are an expensive nuisance.
Pre-empt The Problem
It is important to note that typically the wet wipes do not enter the well as “rag balls”; instead, they arrive somewhat separatly, in small numbers. Over time, the wipes catch on the impeller blades. This can happen from a small buildup of fats, oils, and grease (FOG) or simply from chips on the impeller itself. Once one wipe is caught, more will gradually knit together and form the typical rag ball that causes the motor thermal overload to trip. It is the rag ball itself that trips (blocks) the pumps; or in some cases when the pump stops, the rag ball may detach itself due to gravity and fall back into the well. This results in multiple balls of wipes, looking similar to mop-heads, floating in the well. These mop-heads can then plug the inlet of the pumps.
As the wipes begin to build up, a few things happen. First, the pump’s flow rate can drop by as much as 30 percent. This increases pump speeds (constant flow/level) and cycle time (“fill” and “draw”) and may cause assist pumps to run — significantly increasing the power consumption of the pumping station. Second, the motor requires more power to turn the motor shaft as the rag ball builds, increasing power consumption by an additional 5 to 15 percent. All of this will happen without the pump actually tripping; therefore, the plant operator may not see that any problem exists.
If the intelligent controller monitors the pumps in real time and detects the build-up of FOG or these initial one or two wipes, it can then trigger the starter to reverse the pump. This agitation in the pump will dislodge the one or two wipes and allow them to pass through the pump every time. Another benefit of this is that a rag ball is not allowed to form, thereby maintaining a cleaner well. The key, however, is detecting the buildup — and this is not guaranteed by a timed clean.
The energy savings of this solution can reach 50 percent, just by keeping the pump at its maximum designed efficiency all the time.
About The Author
Graham McIvor is the founder of Clearwater Controls Ltd. and inventor of the Deragger II, a small electronic device that sits alongside the existing pump controls and detects the build-up of wipes in real time, triggering reversal cycles to keep the pump clean. For more information, go to www.clearwatercontrols.co.uk or e-mail mail@clearwatercontrols.co.uk.