SWAN Corner: How Artificial Intelligence Can Mitigate Water Workforce Issues
By Dave Bennett
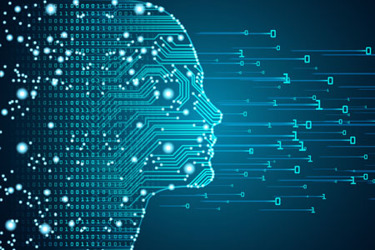
The loss of expert know-how, already a problem for years, has been made worse due to the pandemic. A network of expertise, optimized by artificial intelligence, may be the way to get ahead of the problem.
Companies for years have been dealing with an aging workforce, losing talent and know-how to retirement. Now the pandemic has accelerated this, particularly in water treatment. How do you replace the 20-year service or maintenance veterans and the know-how that is in their heads? Right now, your best techs are super busy supporting customers and newer techs. One of them calls you tomorrow and says they are suddenly retiring. How can you make up for their knowledge once they walk out the door?
The Boomer generation of workers didn’t job-hop too much. One study says the average job tenure for Boomers is 8 years. That’s a lot of time to build up expertise. On the other hand, the same study says Millennials’ average job tenure is 2.4 years. So the Boomers are retiring, and it’s likely their replacements won’t stay around as long. What is your plan?
Due to the pandemic, end users of equipment are wanting to do more problem resolution themselves without having to rely on support and a potential site visit from an engineer. And for field service organizations, sending a service tech onsite has always been the last resort. How can you upskill the operators at your water treatment plants so they can resolve more issues themselves?
The pandemic has seen a rise in solutions such as augmented reality (AR)/mixed reality (MR), as well as other remote service tools. For these solutions to work, you still need an expert on one end or the other. And they don’t upskill anyone. AR/MR, knowledge bases, chatbots… none of these solutions improve skill levels. It’s like having someone drive you to an unfamiliar destination in a car. If you’re a passenger, how much do you remember afterwards about how to get to that destination? Research shows that humans forget 50 percent of what they learn within an hour. So it would seem that current remote service solutions aren’t the answer.
What if you had a way to upskill your own techs as well as your customers, and enable them to retain and grow their new skill sets? In water treatment, what if you could upskill not only your technicians but the engineers and others who operate your treatment plants and associated equipment?
What if there was an on-demand network of expertise that workers could access onsite to help resolve issues with all of the major machines and components at the plant? What if that network was automatically enriched and optimized based on the success and experience of its users everywhere?
In water treatment, our customers face the following challenges:
- Experts are stretched thin, and spend too much of their time helping lesser skilled workers with simpler issues;
- Plant managers often lack the skills to troubleshoot an issue without outside support;
- Many workers cannot interpret alarms or identify the root cause of a problem on their own;
- When there is an issue, it is often a third-party component that is the source of the problem, which means long wait times for a service engineer to come to repair it. Or the local operator is left to using Google to find a troubleshooting manual so they can fix it themselves.
InSkill captures your most experienced workers’ expertise and builds a network of this know-how that we call the InSkill Network. OEMs and factories who build or supply you with equipment also contribute their expertise to the Network. Using artificial intelligence (AI), users access the Network to optimally diagnose and resolve problems and perform tasks. As usage of the AI increases, more people add to the AI’s knowledge through experts entering their own input and enhancing the AI’s solutions.
A tech in Atlanta teaches the AI a new fix, and the tech in Singapore working on the same problem instantly benefits. And all of this is available through the InSkill Network.
The benefits are valuable, innovative, and can apply to service, maintenance, installations, calibrations, training, and others:
- Enable your plant operators to resolve more issues themselves, improving plant productivity.
- Upskill your own techs so that they can perform tasks above their paygrade and not always rely on the experts.
- Capture unwritten knowledge gained over decades of experience. (“The way to fix it isn’t in the manual.”)
- Shorten onboarding time for new hires, enabling them to perform most tasks in weeks instead of months or longer.
- Reduce the burden on your experts so that they can spend more of their time on the less common, super-complex issues.
- Your experts’ “know-how” may be your most important IP. Keep your IP for the long term.
- Improve organizational learning so your team can do their jobs better.
Dave Bennett, VP Sales for InSkill, has been helping service organizations utilize IoT solutions for 20 years. He joined Axeda in 2001 and helped establish Axeda as the market leader in IoT Platforms, which led to them being acquired by PTC in 2014. Subsequently, Dave helped build IoT programs at Oracle and Wind River/Intel prior to joining InSkill, where he has responsibility for building the company's AI customer base worldwide. InSkill (www.inskill.ai) captures your best workers’ expertise and builds a network of this know-how. Using AI, users access the network to optimally diagnose and resolve problems, perform tasks, and more.