Sulzer's HSTs Deliver Decades Of Savings
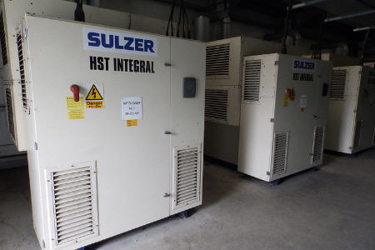
High speed turbocompressor technology helps water companies reduce costs for aeration systems
In demanding water treatment applications, utilities need equipment that provides excellent reliability as well as high efficiency and availability throughout its working life. Those attributes are leading a growing number of water companies to specify Sulzer’s HSTTM turbocompressors in new build and upgrade projects.
Aeration systems are a critical element in many water and wastewater treatment systems. To keep the processes running, operators need high volumes of compressed air from a reliable source. At the same time, the energy consumed by pumps and compressors is the largest driver of operating costs in waste water treatment, so the equipment needs to operate as efficiently as possible.
Life cycle costs
Owners need to maintain tight control over capital project spend and this requires careful analysis of the through-life costs of an asset, considering its upfront cost, projected energy consumption and the need for periodic maintenance.
Total lifecycle cost analyses have become part of good procurement practice, but in some cases the reality doesn’t always match up with the projected figures. Efficiency estimates, for example, are usually based on the “as new” performance of a machine. If the efficiency of the chosen compressor declines as key components wear, its real-world energy consumption will rise over time, until the offending parts are replaced or repaired.
Then there is the issue of unscheduled maintenance. It only takes a few expensive emergency repairs to ruin the financial case for a machine. At one UK sewage treatment works, maintenance costs for aging blowers reached GBP 900’000 over a five-year period.
Improving reliability
Resolving the aforementioned through-life issues for customers was a key driver for Sulzer when developing the High Speed Turbocompressor (HST). To that end, the HST uses a single main moving part: the electrical motor rotor that spins at very high speed on magnetic bearings. This design means there is no moving metal-to-metal contact within the compressor, and hence no mechanical wear. As a further benefit, the high rotational speed allows a smaller motor for a given output.
Since their introduction, the HSTs have logged an admirable record for performance and reliability in water industry applications world-wide. Take the example of Anglian Water’s Basildon Sewage Treatment Works in Essex, UK. As part of an upgrade of its aeration lanes, the facility installed three HSTs in 2007, and added a fourth in 2012.
By November 2020, machine one at Basildon STW had been energized for 11 years and 288 days, and had supplied air for a total of six years and 320 days. That’s a running time of more than 60’000 hours. Every one of the four machines at the site is still working as efficiently as they were when first installed, and the only maintenance they have needed in all that time has been annual filter changes and a replacement battery. During a recent visit, the site manager described the HST units as “One of the best pieces of equipment running on this site.”
Reducing maintenance spend
Basildon is not an exceptional case. A treatment works with a considerable maintenance bill has since replaced its old compressors with Sulzer’s HSTs, and has seen annual maintenance costs drop by 95 percent as a result. At another water treatment works in Scotland, the installation of HSTs led to a 30 percent reduction in energy costs in its aeration lanes.
On the basis of real-world examples like these, it is becoming increasingly common for utilities to specify HST turbo blowers in new builds and upgrade programs, even when their main contractors have suggested another type of machine.
Sulzer can supply HSTs on their own, or as a complete turnkey package including pipework, diffusers and ancillary equipment. After installation, Sulzer offers a comprehensive support package, including remote monitoring if required and the option to upgrade with new technologies as they become available.
Source: Sulzer Pumps Solutions Inc.