6 Steps To Improving Energy Efficiency In Water And Wastewater Operations
By James Chalmers
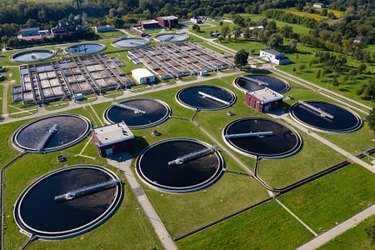
The water and wastewater industries play a vital role in meeting the needs of a growing global population and increasing industrial demand. On a basic level, clean water is essential for human survival, as well as for a diverse range of industrial applications, while effective wastewater treatment is critical to ensuring a sustainable water cycle.
Yet this vital resource comes with a substantial energy output. According to the World Energy Outlook (WEO), water and wastewater utilities account for nearly 4% of the world’s energy consumption — the equivalent of the entire energy demand of Australia.
With emissions targets looming and pressures building around water tariffs that frequently fall short of covering costs, there’s an urgent need to reduce energy usage. This means tackling inefficient processes, such as mechanical flow control and the use of oversized equipment.
Non-revenue water losses caused by leakages are another significant challenge. These leaks are more than just lost water; they represent a significant amount of wasted energy invested in treating and transporting water that never reaches consumers.
Estimates from the WEO suggest that with proper energy-efficient practices and recovery measures in place, consumption could be cut by as much as 15% by 2040.
To achieve this requires a mix of knowledge, technology, and a cooperative, proactive approach. A good place to start is the checklist below, which outlines six key steps for achieving greater energy efficiency in the sector.
Develop A Baseline
Forging a path towards energy efficiency for water and wastewater facilities must first involve collecting accurate, time-stamped energy use data to use as a baseline against future operations. By examining the resources that correspond with plant production — like millions of gallons per day (MGD) or biochemical oxygen demand (BOD) treated — a baseline can be established. Engaging with supervisory, operational, and maintenance staff will then validate this data, while also revealing insights on energy consumption patterns, potential energy-saving approaches, and likely obstacles. A precise walkthrough to assess the size, capacity, and working status of key assets brings even greater accuracy and helps to set a rigorous foundation for future comparisons.
Understand The Savings
The extraction and delivery of water is particularly energy-intensive in a clean water plant. Optimizing this process largely lies in employing efficient pumping systems and blowers. Making incremental improvements, such as adopting modern pump technology or incorporating variable speed drives (VSDs) — also referred to as variable frequency drives (VFDs) or simply drives — and high-efficiency motors can result in energy savings ranging from 3% to 30% or more.
As an example, shifting to advanced technologies like ABB’s IE5 synchronous reluctance (SynRM) motors will significantly increase energy efficiency when paired with a drive. It’s crucial to bring in best practices such as energy-monitoring techniques, power cycling non-essential equipment, and improved maintenance. Understanding the fundamental advantages of applying drives such as the ACQ580 water and wastewater drive with built-in water pumping features such as multi-pump control, pump priority, and sleep boost can lead to a huge boost in both efficiency and profits.
Identify And Assess Areas For Improvement
Zeroing in on system-specific energy-saving opportunities should begin with creating a detailed facility assessment plan, including a complete system walkthrough and focused application identification. These assessments will help to identify the applications to prioritize for the highest return on investment (ROI). Water and wastewater businesses also need to build a capable team to analyse these opportunities and construct a tailored action plan.
Efficiency improvements may involve changes both in equipment and operational procedures, with each modification aimed at reducing the plant’s energy consumption or power demands. Where the expertise doesn’t exist in-house, expert consultants from an organization can help by recommending a list of priorities and an implementation plan.
Implement Improvements
A thorough plan for implementing changes should involve all stakeholders. This means coordinating project timelines, budget allocations, and task management to achieve the desired outcomes. This procedural roadmap should detail how existing processes or schedules might change and highlight potential shutdowns.
The value of the changes must be shown in energy performance metrics, which should fall in line with designated key performance indicators (KPIs). By measuring returns against the KPIs, the accuracy and efficiency of the project can be validated.
Track And Report Progress
Monitoring and reporting are crucial for ensuring the delivered improvements are sustainable. Upon installation, businesses should focus on the previously identified KPIs and performance metrics, including installation statuses, impacts on facility energy use, operations and productivity impacts, process performance, and employee engagement.
Share these insights with stakeholders, including anyone who's been involved in the energy plan, as well as operations and maintenance staff. Remember: tracking and reporting is a vital step for the success of the energy efficiency plan.
Continually Update The Plan
Once changes have been made to improve facility efficiency, complacency is not an option. Continuous reviews of the energy plan should be held to ensure consistent improvements. As the plan progresses towards the goals, lessons will naturally be learned from past successes and failures, and businesses will need to change strategies accordingly.
The energy-efficiency plan will also come up against evolving industry standards and economic or legal landscapes, which might require future changes. This iterative process should remind stakeholders that moving towards a more efficient future isn’t a one-off process, but one that’s constantly evolving.
Energy-Intensive Processes To Focus On
The reduction of energy consumption should be everyone’s goal. But with no consistent global regulation, and with many countries continuing to adopt low-efficiency systems, it’s clearly a goal that will take time to achieve. It’s likely that movements will be made gradually, with certain processes the first to be optimized.
When it comes to clean water production, systems like lake and river pumping, as well as groundwater abstraction — all critical to an adequate clean water supply — are clear candidates to be made more efficient. One example is to substitute flow control by traditional throttle valves with drives that help the motor speed to match the required output, enabling pumps to operate at their Best Efficiency Point. This can reduce both the operating costs and environmental impact of a clean water plant.
For example, in Vietnam's thriving Kim Dong district, access to clean water has been a mounting challenge amidst rapid economic growth. The newly established Kim Dong surface water treatment plant, powered by ABB’s variable speed drive technology, is addressing this issue. By deploying 28 ABB ACQ580 water industry drives, the plant has realized a 20% to 30% increase in energy efficiency compared to traditional fixed-speed control systems.
For wastewater facilities, aeration processes account for around 53% of energy demand. There are a number of reasons for this, including the variations in the loading of the treatment plant and differing time scales, making it a challenge to optimize the plant at the time of installation.
But this energy-intensive process can benefit hugely from the use of drives. These drives can mitigate the overuse of pumps and aeration systems that adjust for fluctuating loads, achieving energy savings of up to 70% by directly controlling motor speed and dissolved oxygen levels.
In Denmark, Knabstrup Vandværk, which provides water to over 500 consumers and the Nordvestsjælland Water Community, has successfully integrated ABB ACQ580 drives in its water and wastewater facilities, leading to energy savings and stable water pressure. These drives optimized the operation of five water pumps, resulting in a 20% reduction in energy consumption and minimizing the wear and tear on the water distribution infrastructure.
The end result was not only cost savings, but also the prevention of contaminants from entering the water supply, as the even pressure negates the shocks that can dislodge ocher into consumer taps. The ease of setup, facilitated by Bluetooth connectivity, and intelligent multi-pump control features in the ACQ580 drives, has also offered seamless management, ensuring a consistent and efficient water flow.
Driving Towards A Sustainable Future For Water And Wastewater
Adhering to the six steps laid out here can lead the water and wastewater industries towards a more sustainable and cost-effective future. First, it is essential to establish a baseline for energy usage, which sets the foundation for designing an energy plan. This plan should identify potential areas for improvement and outline strategies for integrating water and wastewater drives into existing processes. These changes will achieve significant energy savings, quickly.
As we navigate an era marked by environmental and financial pressures, it’s clear that refining energy efficiency isn't merely beneficial — it’s crucial for the longevity and resilience of water and wastewater facilities.
For further information: https://new.abb.com/drives/segments/water-and-wastewater
James Chalmers is Vice President, Water and Wastewater Sales, at ABB.