Retractable Odor-Control Covers Improve Access To Wastewater Tanks At San Francisco Bay Sanitation Plant
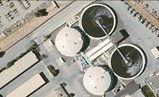
Retractable, structurally-supported geomembrane cover system provides odor control and ease of access for maintenance to wastewater treatment aeration basins at the Vallejo Sanitation & Flood Control District.
By Jim McMahon
The Vallejo Sanitation & Flood Control District, in the San Francisco Bay area, has been engaged in a program to scrub off-gas odors from all aspects of its wastewater treatment plant. Early in the project, the district had covered all of the facilities in its headworks and primary treatment steps to control off-gas. Later, it developed a novel approach for the management and disposal of its biosolids, including designing a specialized hopper for storage of the plant's dewatered solids and an automated truck-fill process for transportation of the solids to a district-owned landfill – Tubbs Island – again minimizing off-gas release. Recently, the wastewater plant has focused on scrubbing off-gas odors from its secondary treatment processes, and specifically its two open aeration basins. To contain these odors, the district opted to use a retractable, structurally-supported geomembrane cover system from Geomembrane Technologies Inc. (GTI), which has not only proved effective for the collection of off-gas, but has also provided an unprecedented level of flexibility and ease-of-access for tank monitoring, maintenance and repairs.
The Vallejo Sanitation District
The Vallejo Sanitation & Flood Control District is an independent special district created by the State of California to collect and treat wastewater, and to protect the Vallejo community from flooding. Since 1952, the District has protected public health and the San Francisco Bay by collecting and treating the wastewater generated by more than 115,000 residents of Vallejo and the surrounding area.
The district has a tradition of innovative use of technology in wastewater handling. It has been recognized by the EPA and awarded the National First Place Award as the most outstanding project involving land application of biosolids in the United States. The plant disposes of 20,000 cubic yards of biosolids per year, where it is used as a soil amendment to improve farmland. The plant differs from most in that it uses no digesters in its process.
The Vallejo facility is permitted to treat 15.5 million gallons per day (mgd), but has the capacity to provide full secondary treatment of 35 mgd. During wet weather, the plant is capable of processing 25 mgd primary treatment, combined with the 35 mgd secondary treatment for a total of 60 mgd.
Vallejo's Wastewater Treatment Process
Passing through Vallejo's primary water treatment units – its headworks, grit chamber and primary clarifiers – where the solids are separated out, the liquid part of the waste stream flows to the plant's secondary treatment for biological processing.
Vallejo's secondary treatment process is a trickling filter/solids contact process, consisting of four main treatment steps – biotowers, contact aeration basins, secondary clarifiers and disinfection.
The trickling filter part of the process is provided by two biotowers, which receive effluent from the primary clarifiers. The wastewater is sprayed down over plastic media in the filter providing a surface for bacteria to grow and consume the organic material in the effluent. The water is run through the biotowers twice, essentially removing 99 percent of the organic material running through the secondary treatment.
After biofiltration, the wastewater is pumped into two aeration basins. The aeration tanks condition the solids particles discharged from the biotowers, so they settle more readily in the downstream secondary clarifiers. Blowers and fine-bubble diffusers mounted on the floor of the basins introduce air that is necessary for the flocculation of particles, converting the organic solids into heavier clumps that settle and are removed by sedimentation in the secondary clarifiers.
Leaving the contact aeration tanks, the flow continues to the secondary clarifiers, where bacteria and fine organic substances settle out of the wastewater. The wastewater then enters contact basins where it is mixed with sodium hypochlorite, followed by sodium bisulfite to remove residual chlorination, before it is pumped into Mare Island Strait via a 2.5-mile-long pipeline.
Streamlined Aeration Basin Covers
The Vallejo plant's two secondary process aeration basins were originally built in 1988, and are each 15 feet deep, 15 feet wide and 110 feet long. Every few weeks, the Vallejo operators conduct a visual inspection into the aeration tanks from the top. Once a year they drain the tanks, go down inside to conduct a physical inspection of the blowers and diffusers at the bottom, and hose down the sides of the basins.
For almost 20 years the basins remained uncovered, but as part of the plant's odor control upgrade, the district looked into options of how to cover them. Carollo Engineers, an environmental engineering firm specializing in the planning, design and construction of water and wastewater facilities, was retained by Vallejo to handle the design and construction management for the plant odor control upgrade, and began reviewing different cover options for enclosing the basins.
"We wanted the covers first for odor control, so they needed to be corrosion resistant," says Tim Tekippe, Carollo Project Manager handling the Vallejo project. "But we also needed the covers to be easy to open and close for access to the tanks for sampling, scheduled maintenance and repairs. We felt structurally-supported covers would be the best system for the plant's needs because of the better access they provide over other systems, like floating covers. We first looked at rigid type covers such as aluminum and fiberglass, but both of these proved more labor intensive for operators to gain access to the basins."
Depending on their size, aluminum panels can be heavy, and both aluminum and fiberglass covers being rigid, can be bulky and difficult to maneuver for workers while perched above an open tank. This tricky maneuver requires a fair amount of labor – both to take the aluminum panels off, place the covers aside and later put the covers back on – but also poses a potentially significant safety hazard for the workers.
"Along with our engineering firm, Carollo, we looked at a number of other wastewater plants, and what they were using to cover their aeration tanks," says Barry Pomeroy, Director of Operations and Maintenance at the Vallejo Sanitation & Flood Control District. "The aluminum and fiberglass covers we looked at were big plates, and seemed hard to handle and remove. Then we went to a water treatment plant in Colorado that was using retractable, structurally-supported covers made with a geomembrane fabric. They looked like they would be very easy to remove for maintenance, and watched how easy they were to open and close. We even walked on them while they were in place over the tank, to see how strong and durable they were. Based on that trip, we decided to design these retractable covers into our aeration basins."
Vallejo's new retractable, structurally-supported geomembrane cover system – designed, engineered and built by GTI – consists of a composite sheet of high-strength, UV-protected, coated fabric tensioned across a series of low-profile aluminum arches which span the tank's opening. Intermediate aluminum walkways spanning the tank are used to divide the fabric cover sections into appropriate lengths for easy retractability.
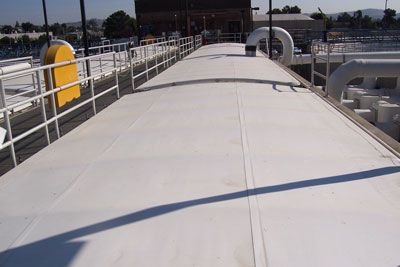
The geomembrane cover fabric used by GTI is made up of a laminated sheet of 40 mil specialty PVC (Ethylene Interpolymer Alloy) that acts as a gastight barrier to keep the off-gas from passing through. It incorporates a highly specialized weave design that provides maximum strength-to-weight ratios. Since this topsheet is exposed to the sun, it is also equipped with advanced UV inhibitors. The material can withstand temperatures to minus 30 degrees F. This cover has exceptional seam strength, extreme puncture and tear resistance, low thermal expansion and contraction properties, a wide range of chemical resistance, high flexibility, and dimensional stability under high loads and temperature fluctuations, making it ideal for wastewater cover applications.
Not all geomembrane cover designs work this efficiently, however. Polyethylene topsheets, for example, typically have a poor coefficient of expansion and contraction. The material expands in warm temperatures and contracts as it cools down. Over time, this growing and shrinking contorts the shape of the cover, creating a series of hills and valleys that retain rainwater. GTI's cover system has overcome these deficiencies.
Vallejo's covers are gas-tight, operating under negative air pressure. A ventilation system draws air through the tank and underneath the covers, and pulls along with it the off-gas from the aeration process. Off-gas removal piping is connected directly to the cover system and out to a soil filter for odor scrubbing.
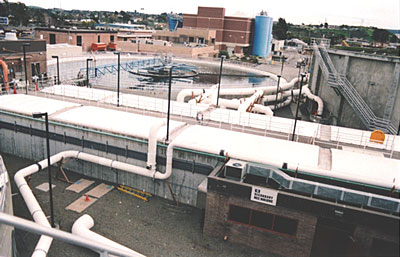
Although the membrane covers are gas-tight, they can be quickly detached and easily rolled up along the frame. This gives operators access to inspect and maintain internal components of the basins. Reattaching the membrane covers is quick and easy, making for a time-efficient and safe process. Additional hatches in the intermediate aluminum walkways allow access by plant operators without retracting the covers.
Attractive Option for Municipal Wastewater and Drinking Water Plants
"The expected life of these retractable covers is about 15 years," explains Tekippe. "And the cost is very attractive compared to other cover systems. If a cover did have to be replaced it would be easy to change out, and could be done in minimal time. These retractable covers are very well-suited for both municipal wastewater and drinking water plants. We have since specified them for use in other public water and wastewater projects."
Municipalities are looking for more efficient tank cover systems to contain off-gases, reduce algae growth, simplify maintenance and repairs, and cut expenses. Retractable, structurally-supported geomembrane covers have become an increasingly attractive option for streamlining wastewater plant operations.
About Geomembrane Technologies:
Geomembrane Technologies Inc. (GTI) is a world leader in providing innovative and reliable tank and lagoon cover systems. GTI designs, engineers, fabricates, installs and maintains complete odor control systems worldwide. Projects include liners, floating and structurally supported covers, and gas-handling cover systems for municipal and industrial wastewater treatment plants, as well as for the agricultural sector. In addition to floating and structurally supported covers, GTI also offers potable water covers.
For more information on Geomembrane Technologies Inc., please contact Brennan Sisk; Phone 506-452-7304; 1133 Regent Street, Suite 300, Fredericton, New Brunswick, Canada E3B 3Z2; email bms@gticovers.com; www.gticovers.com.
To find out about Carollo Engineers, contact Tim Tekippe, P.E., Vallejo Project Manager; Phone 512-453-5383; 8911 Capital of Texas Highway, Suite 2200, Austin, Texas 78759; email ttekippe@carollo.com; www.carollo.com.
Vallejo Sanitation & Flood Control District can be reached by contacting Barry Pomeroy, Director of Operations and Maintenance; Phone 707-644-8949, ext 251; 450 Ryder Street, Vallejo, California 94590; bpomeroy@vsfcd.com; www.vsfcd.com.
SOURCE: Zebra Communications