Process Factors Affecting Proper Aeration Basin Control
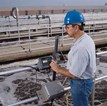
For a plant control scheme to provide accurate and efficient control, many process factors must be considered. One such factor—the heart of the activated sludge process—is located in the aeration basin.
By Jim Klauer, GLI International
Contents
Biomass is the activated sludge plant's most important component
Understanding the variations in oxygen demand
Installing a dissolved oxygen sensor to monitor, control air addition
Other factors influencing proper aeration basin control
There are many components involved in the delicate balance of the micro-universe contained in an aeration basin. Some of these components are part of the original system design and are not controllable or changeable. However, there are other, controllable components of the system that must be balanced.
Examples of these controllable components include:
- Biomass: a blend of beneficial microscopic organisms, bacteria, and solids that convert non-settleable solids (dissolved and colloidal matter) into settleable solids, carbon dioxide, water, and energy.
- Air: typically pumped from pure oxygen tanks or generated by blowers, fed into basin through bubble diffusers, and controlled by dissolved oxygen measurement.
- Return Activated Sludge (RAS): most plants choose to keep mixed liquor suspended solids (MLSS) concentration in RAS line within a specific concentration range by monitoring suspended solids concentration in RAS line or sludge blanket level in secondary clarifier.
- Waste Activated Sludge (WAS): how efficiently RAS concentration is controlled, directly effects amount of sludge being wasted. Regulating WAS is the most dramatic way to change the sludge and effluent quality.
- Throughput: the amount of wastewater that is passed through plant in specific time period.
Biomass is the activated sludge plant's most important component (top)
The most important component of any activated sludge plant is the biomass, or microscopic bugs. In very simplified terms, the bugs attach themselves to the waste, and digest the waste as a food supply, resulting in relatively clean water as the by-product.
In an aeration basin there are several types of bugs that can be categorized into two main groups: carbonaceous (carbon eaters) and nitrogenous (chemical eaters like ammonia). Both groups have different duties, but as living organisms, they all need oxygen to sustain life and reproduce.
Understanding the variations in oxygen demand (top)
To understand the variations in oxygen demand, you first need to know how the bugs get into the aeration basin. Effluent from the primary clarifier is mixed with the return activated sludge (RAS) from the secondary clarifier as it enters the aeration basin. This mixture, known as "mixed liquor," contains all the bugs the system needs to efficiently treat the wastewater. The hydraulic load, the amount of wastewater entering the aeration basin, determines the amount of RAS needed to maintain the proper bug population. With more wastewater entering the basin, more biological material and food exist for the bugs to eat, which increases their growth rate and demand for oxygen.
After a few hours in the aeration basin (depending on the throughput of the plant), the mixed liquor is moved to the secondary clarifier. The mixed liquor settles there and a portion of the settled sludge is returned to the beginning of the aeration basin via RAS pumps. The excess sludge, known as waste activated sludge (WAS), is removed from the clarifier via WAS pumps and sent to the biosolids stages of the plant for further treatment.
The greatest amount of oxygen is used near the intake portion of the aeration basin. In the secondary clarifier, the bugs have been starved for oxygen because it was not added in this stage. Consequently, when the bugs return to the aeration basin, via the RAS line, they need to take a "deep breath." Also, the bugs use more oxygen when attaching themselves to the non-settleable solids (dissolved and colloidal matter) upon reaching the aeration basin. As the flow passes through the basin, the demand for oxygen decreases. This is known as tapered aeration or step aeration.
In a typical aeration basin, 40% of the oxygen demand occurs in the first quarter portion of the basin, 25% in the second quarter, 20% in the third, and 15% in last quarter portion.
Installing a dissolved oxygen sensor to monitor, control air addition (top)
To obtain an "average" reading for monitoring and controlling the air addition, a dissolved oxygen sensor is normally installed about 2/3 of the length of the aeration basin from its intake. Some aeration plants use two dissolved oxygen sensors per basin to insure that there is enough oxygen in the first quarter of the basin to "wake-up" the bugs, without wasting energy by over-aerating the last quarter of the basin. Too much oxygen is not a problem for the bugs, but the cost to generate oxygen is one of the largest operating expenses of a wastewater treatment plant. If the supply of oxygen can be more tightly controlled, just enough to keep the bugs alive, then large amounts of money can be saved by generating only the amount of oxygen necessary. For this reason, multi-stage dissolved oxygen control is often used in large aeration basins.
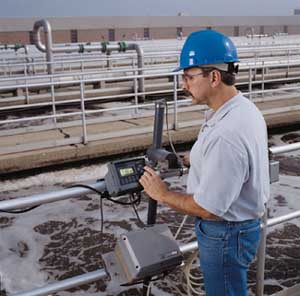
As seen here, this operator is using a dissolved oxygen system to control an aeration basin in a wastewater treatment plant. The system shown above is manufactured by N/A.
Other factors influencing proper aeration basin control (top)
We have discussed how hydraulic loading, RAS control, and how the type and quantity of bugs present can influence the oxygen demand in an aeration basin. There are also several other factors that can influence proper control of the aeration basin:
- Temperature -- All chemical reactions are affected by temperature. This is also true for waste consumption by the bugs, and the rate they multiply. When temperature increases, the rate at which the bugs eat and reproduce also increases. In fact, every 10°C increase doubles the bug reproduction rate, up to a limiting temperature. With an increase of bugs, the demand for oxygen increases dramatically. Most of the bugs achieve optimum efficiency between 10° and 40°C.
- pH -- As with temperature, the pH has a considerable influence on the ability of the bugs to work efficiently. When the pH is too low or too high, the bugs lose the ability to convert the food to energy and raw materials. The aeration basin pH for most systems should be kept between 6.5 pH and 8.5 pH.
- Toxicity -- Some organic materials and heavy metals are toxic to the bugs, reducing their efficiency or even destroying them. If the bugs get sick or the weaker strains die, the micro-universe suffers, reducing the plant efficiency and increasing the potential of untreated waste.
There are many factors to consider for proper aeration basin control. If one or more of these factors are out of balance, the whole system suffers and becomes inefficient. Plant operators may see several symptoms such as oxygen level spiking, an increase in the BOD level in the secondary clarifier, or improper settling of the mixed liquor when the system is out of balance.
References:
Simplified Wastewater Treatment Plant Operations, Edward J. Haller, 1995
Basic Activated Sludge Process Control; Water Environment Federation, 1994
This is one of several documents pertaining to dissolved oxygen measurement in wastewater treatment prepared by N/A. To obtain other application notes on this subject, contact the company at the address listed below.
About the Author:
Jim Klauer is product manager with GLI International, 9020 West Dean Road, Milwaukee, WI 53224; phone 414-355-3601, fax 414-355-8346.