Preserving The Bay Area
By Erin Boudreaux
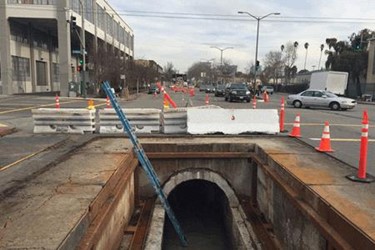
With any aging system, inspection, cleaning, rehabilitation, and repair is essential to maintaining the systems integrity. The City of Oakland, CA, the largest city in the East Bay region, certainly has its share of utilities to maintain. The City of Oakland’s sanitary sewer system encompasses over 930 miles of sanitary sewer pipes and includes 31,000 structures and seven pump/lift stations.
The City of Oakland is responsible for the public sanitary sewer main pipes that carry waste to the treatment plant while East Bay Municipal Utility District (EBMUD) is responsible for sanitary sewer treatment and disposal. In 2014, an agreement was reached in the form of a Federal Consent Decree (CD) between the U.S. EPA and EBMUD along with the cities of Oakland, Alameda, Albany, Berkeley, Emeryville, Piedmont, and the Stege Sanitary District to protect San Francisco Bay from sewage spills. This settlement gives the cities and districts until 2036 to repair and replace sewer lines; reduce the amount of inflow and infiltration, and reduce discharges into San Francisco Bay during heavy storms.
The City of Oakland had already spent millions upgrading their system when the consent decree was announced in 2014. The City agreed to upgrade 13 miles of sewers annually and are already ahead of schedule. Oakland has spent over $300 million since the early ’80s to improve its collections system and reduce flows.
Largest Trunk Sewer in Oakland
A recent project is the Rehabilitation of the West Grand Sanitary Sewer: West Grand Avenue and 20th Street. Constructed over 90 years ago, this trunk sewer is non-circular and is the largest-diameter trunk sewer operating in the City of Oakland. The 72 x 78-inch and 60 x 66-inch system carries wastewater from downtown Oakland to EBMUD’s 105-inch Wood Street Sewer Tunnel to the Wastewater Treatment Plant (WWTP) in the Port of Oakland. After the assessment and design phase, permits were issued to rehabilitate roughly 4,000 feet of the non-circular system by sliplining and 4,300 feet of circular RCP was also included with either slipline or CIPP rehab options.
After the assessment and design phase, permits were issued to rehabilitate roughly 8,000 feet of the West Grand Sanitary Sewer.
The $6.5 million project was awarded to Andes Construction, Inc., of Oakland, CA. The City of Oakland specified fiberglass pipe and CIPP for this rehab and Andes chose to bid the entire project with centrifugally cast, fiberglass reinforced, polymer mortar (CCFRPM) pipe. Slipline was chosen as the rehabilitation method due to the projects location in a downtown and industrial area, and because it also ranged in depth from 8 to 18 feet.
“The base bid required FRPM for the non-circular sections. The rest, although suitable for CIPP, required a considerable amount of water for the cleaning and curing process of the pipe that at the time was not a good option as we were going through a critical drought so we decided to bid the entire project with fiberglass pipe,” said Cynthia Orozco, project manager, Andes Construction.
Hobas manufactured approximately 1,656 feet of 63-inch and 1,072 feet of 51-inch for the non-circular portion of the project; over 1,800 feet of 44-inch and 1,267 feet of 54-inch was also supplied for the circular portion. This would be the first large diameter slipline project for the City of Oakland and Andes Construction. The project began in October 2015 and was completed in June 2016.
Maintaining Capacity with Sliplining
The existing circular RCP was 48 and 60 inches in diameter. Even though there was a reduction in diameter for the entire project, the smooth interior of the CCFRPM pipe did not lead to a decrease in flow. Hydraulics is an important consideration when planning pipeline rehabilitation. Sliplining always results in a slight decrease in the pipe’s inside diameter; however, because of the much better flow characteristics of CCFRPM liner pipe, the rehabilitated line's hydraulics are improved relative to its existing condition. Understanding hydraulics can help owners decide what pipe-flow rates related to size and material are necessary to transport water in an efficient manner.
The pipe was transported to the site from the manufacturing facility in Houston, TX.
Rapid Installation
Andes Construction was able to push 1,800 feet of 44-inch CCFRPM pipe into the existing 48-inch pipe in less than eight hours. Andes also installed approximately 1,100 feet of 51-inch in about 10 hours and 1,200 feet of 54-inch in 18 hours. Extensive planning, cleaning prior to installation, and a pushing frame built by Andes contributed to the ease of installation.
The majority of the pipe was supplied in 20-foot sections, but shorter 10-foot sections were manufactured for the curved portions. Original plans did not show any curves in the alignment of the existing sewer. After an inspection, it was decided to use 10-foot sections to navigate these changes in alignment.
“The first phase of the project was along West Grand Avenue; there we encountered the first curve. At this location we had narrow streets and heavy traffic. Here a smaller pit was excavated and 460 feet of 10-foot sections were pushed upstream without delay,” said Orozco. “The second phase was in the busiest downtown area, Harrison Street; here the curve was located at a busy intersection where the amount of underground utilities did not allow for a pit excavation. The curve was at the beginning of the last downstream sections of the 60- by 66-inch trunk line. Roughly 220 feet of 10-foot sections were pushed into place, followed by 610 feet of 20-foot sections without interruptions. We switched gears and pushed another 250 feet of 20-foot sections upstream to the beginning of the trunk line; all 64 pipes were pushed within 10 hours. The use of the shorter sections helped us to avoid ground disruption at these busy downtown streets. We used the flush bell-spigot joint and it worked perfectly; there was no need for any additional equipment to keep the pipe aligned and follow through the curvature of the existing system.”
The flush bell-spigot joint consists of an integral straight bell fixed to one pipe end that seals to the spigot end of another pipe by compressing an elastomeric gasket contained in the groove on the spigot. The joint has approximately the same outside diameter as the pipe, so when assembled, the joint is essentially flush with the pipe’s outside surface.
Completed in the summer of 2016, the new pipe has been performing well. It is currently running at 30 to 50 percent capacity, as the City installed this size pipe to allow for growth. Sliplining rehabilitation of sewers with CCFRPM pipes provides many benefits. Not only is the flow capacity frequently increased, but the host pipe is structurally reinforced, corrosion is stopped, and leakage is eliminated.
Erin Boudreaux is the marketing manager for Hobas Pipe USA.