Port Jefferson Power Station Lands FiberSystems FRP Fish-Friendly Solution
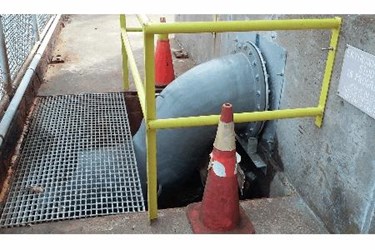
When National Grid installed fish-friendly intake screens at its’ Port Jefferson Power Station; it needed a new discharge piping assembly with a small footprint that could capture water from a fish and debris trough, and funnel it to a harbor return pipe. Port Jefferson Harbor waters hold an SA classification which is given to areas with outstanding natural resources for swimming, fishing and shellfish harvesting. FiberSystems’ Fiber Reinforced Plastic one-piece, contoured composite solution won the competitive bid over conventional materials.
Specifications for the discharge pipe spool called for close dimensions, corrosion resistance, a smooth interior and water-tight connections. “We looked at several designs including flanged or mitered sections that could be fastened into the approximate shape we needed,” says Matthew Gaskin, lead engineer for National Grid. “But the FiberSystems FRP product offered a lightweight alternative that precisely conformed to our dimensions. Corrosion was also a concern for us, because salt water is very aggressive. FiberSystems’ contoured design and high-performance epoxy vinylester interior finish was fish-friendly, non-corrodible, and gave us a longer life cycle. We were able to justify the project’s cost.”
With an outside diameter of 22 inches, the 69-inch long flanged by beveled end spool was fabricated with a custom-made smooth-radius foam tool to contact mold piping with epoxy vinylester fish-friendly resin. The flanged end was custom drilled to match the existing aluminum flange. Handles were custom molded into the pipe structure for easy lifting and installation.
“The FRP solution was attractive because it was the best fit,” explains Bob Houston, environmental manager for the Port Jefferson Power Station. “We needed a product with performance characteristics that complied with our mission to complete a fish-friendly harbor return pipe. Fish are collected on screens specially modified for enhanced survival. The discharge pipe collects and carries them back to the source waterbody. The FRP product was exactly what I asked for.”
“And it fit like a glove,” adds Gaskin of the recent FRP pipe assembly installation. “The connection to the fish and debris trough is watertight. We’re able to move every drop of water from the trough to the harbor return pipe without spillage. The pipe’s compact size also allowed us to install the remaining section of walkway grate to maintain continued access to the area.”
About FiberSystems
FiberSystems leads the industry as a custom manufacturer of Fiberglass Reinforced Plastic composite parts in a wide range of sizes for structurally demanding applications and corrosive environments. With nearly 70 years of fabrication and engineering expertise, FiberSystems combines specialized resins knowledge, innovative design and materials, manufacturing technology and restoration services to support a diverse product lineup that includes pipe, fittings, duct, containment systems, tanks, pipe supports and items like pultruded structural shapes, flooring systems, grating and coatings.
For more information, visit http://www.ifs-frp.com/
Source: FiberSystems