PFAS Filtration: Designing For Smaller OPEX And Footprint
By Conrad Hopp
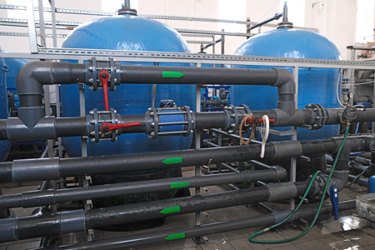
In April of 2024, the U.S. EPA announced two regulatory actions targeting PFAS (per- and polyfluoroalkyl substances), also known as “forever chemicals” due to their persistence in the environment and associated health risks. The first of the two, published on April 10, outlines drinking water standards for six individual PFAS and combinations therein. Nine days later, the EPA announced its rule designating two PFAS compounds, perfluorooctanoic acid (PFOA) and perfluorooctane sulfonic (PFOS), as hazardous substances under the Comprehensive Environmental Response, Compensation, and Liability Act (CERCLA). These rulings will require the installation and operation of PFAS treatment technologies at municipal drinking water utilities as well as federal and industrial sites that utilized or manufactured PFAS.
The EPA has designated three technologies as best in class for PFAS treatment: granular activated carbon (GAC), ion exchange (IX), and reverse osmosis. Of the three technologies, GAC and IX, often collectively referred to as media filtration, are considered the gold standard for PFAS treatment due to cost advantages and performance reliability. When designing a media filtration system, there are two components that impact capital and operating costs:
- Media selection
- Mechanical design.
With thousands of systems due to come on-line in the years ahead, minimizing cost is essential to ensuring public money is used efficiently. While multiple factors must be considered in the design of filtration systems — including media selection — mechanical design is a centerpiece of cost and performance optimization.
Get unlimited access to:
Enter your credentials below to log in. Not yet a member of Water Online? Subscribe today.