Perfecting Plastics Through Welding
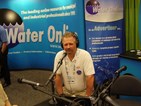
Jim Leary of Widos Welding talks about the benefits of plastic over metals, and offers the products and services needed to help carry out the plastic pipe customer.
Todd Schnick: And we’re coming to you live from Dallas, Texas. This is day four of AWWA ACE 2012 and Water Online Radio. I’m your host Todd Schnick, joined by my friend and colleague Todd Youngblood. Todd, I cannot believe this is our final interview, and of all people.
Todd Youngblood: I thought we were going to dodge this bullet, but it’s just not meant to be, it’s just not meant to be.
Todd Schnick: Well, I’m really excited to welcome our good friend and our neighbor here at AWWA, Jim Leary, who is the national business development manager at Widos Welding. Welcome to the show, Jim.
Jim Leary: Thank you, guys. Thank you very much for having me here and, like they say, you can pick your friends but you can’t pick your neighbors, so...
Todd Youngblood: That is true. I want to hear, do you think you can hum the theme song. I mean he’s heard it 64 times in the last three days.
Jim Leary: I do want to thank you, because I’ll have this running in my head for the next two weeks.
Todd Schnick: Now you’re a fan of funk music, that’s just great. We are going to be hoping that Jim’s colleague will be joining us. He had to take an important customer opportunity phone call, so we may get lucky with his presence, but let’s go ahead and get rolling with you, Jim. Before we get started, take a second and tell us a little bit about you and your background.
Jim Leary: I’ve been in the piping industries about 25 years now, both in metals and plastics. I’ve been focusing on plastic welding for about the last 13 years. So this is new and innovative things and changing technologies in the world, so I’m glad to be a part of it.
Todd Schnick: Well, we are glad you are a part of it as well. Tell us all about Widos Welding. What do you guys do, and how do you service your market?
Jim Leary: Well, what we do is we manufacture plastic welding machines and provide machines to weld thermoplastic piping systems, which are being used more and more around the world in a multitude of different industries in everything from pharmaceutical, wastewater, water industries, mining, automotive, everything in a wide array.
So it is something that is emerging more and more. It’s used throughout the world and it’s catching on here in North America as well.
Todd Youngblood: Now, Jim, I got to tell you my experience of putting pipe together is limited to PVC for sprinkler systems and you put the little epoxy stuff on and slap them together. Welding sounds maybe a tad more sophisticated than that. Can you give us 101 on plastic welding. What the heck is it?
Jim Leary: Sure can, a lot of people say that when you talk about a welding machine for welding plastics and they look at you like that’s not the right way to say it, but basic welding or fusion is a process of time, temperature, and pressure.
It’s that simple, and depending on what type of material it is that varies the formula and what kind of time or what kind of temperature is used. Basically, you are just using pressure and heat to fuse together molten material and it makes it stronger and its pressure-rated and able to be just as strong as the material is itself.
You don’t end up with any of the solvent cements all over your hands so your hands look purple when you go to eat dinner at the end of the night, any of that kind of stuff that comes from the sprinkler stuff. That’s what I end up with anyways when I’m doing it. So it’s a very simple process.
Todd Youngblood: Me too.
Todd Schnick: Help me understand or help all of us understand exactly what industries you guys serve.
Jim Leary: Well, like I said it’s a broad scope, and right here inside the AWWA ACE show, we are focusing on the water and wastewater industries. Water has to transfer and be transferred from tanks and into municipalities, chemicals that are used to treat these wastewater effluents, and drinking water itself — all has to be used, and metals aren’t often compatible for that.
So plastic piping is used and they need to — it’s pressure-rated material, so they need a strong bond and that assurance that that works, and we provide machines that make that type of weld. There are a lot of different encounters that an installer may have and our machines are able to meet that type of installation challenges by being able to do that, and that’s where our innovation comes in as a company, in making machines that meet those challenges.
Todd Youngblood: I am wondering. I am making an assumption that plastic pipe is not used as much as traditional materials are. Do you have to do missionary work, so to speak, to get folks — I mean, in order to buy the machine they have to be using plastic pipes to begin with.
Jim Leary: That’s an excellent question, and that’s very true. To start this off, we are a German company. We manufacture everything in Germany, in house, so we get to travel the world a little bit more and see how plastics are being used.
Throughout the rest of the world plastics are used predominately as a main source for piping stuff, and here in the United States we’ve always been more based on metals.
So there is a challenge in getting people to use and look and accept plastic as an innovative alternative to what they are trying to do. It is becoming more prevalent now because the costs of metals have gone up so much and the cost of mining, the ecological impact that metals are having on the earth and that being more of a focus now in the business community as well as ecologically.
So plastics are something that’s being opened up to people and you do have to educate them to say, “Yes, this will work.” It’s not the old school plastic that we are all familiar with here as we’re doing our sprinkler systems in the front yard.
These changing resins and plastics can now handle quite acidic and aggressive chemicals and be able to use and last for 50 to 100 years and not damage the ecology while manufacturing this kind of stuff.
Todd Schnick: It really has been a pleasure to share a corner in the hall with you here at ACE12 but how…
Todd Youngblood: Except when he peaks his head through the curtains. It spooked the daylights out of me.
Todd Schnick: Well, I have a theory as to why he was doing that, but we won’t go into that. How has the show gone for you? What were your goals and objectives coming into ACE12?
Jim Leary: A lot of it was exposure, to let people know who we are, because we are a very well-known company throughout the rest of the world, and yet the North American market is something that we’re challenged to open up as a business opportunity and let people know who we are and the experience that we bring.
We are, as a company, we are one of the original innovators of plastic welding, so we’ve been around for 65 years and this is, as I was just saying, we were talking about trying to educate people and bring them on board to using the alternative of using plastic piping and fusing, and we have that technology and it’s tried and true and used, so it’s not something that someone is going to have to take a leap of faith on and try and use.
The intent to come here was to show more people how we could do that. The features and benefits that we can show them and allow the contractors to install these types of things, and it’s been very successful. We’ve had a lot of interest in the booth and a lot of people coming by.
Todd Youngblood: Jim, money is one of my favorite topics and we really haven’t talked about the economic impact, the financial impact. I would think plastic is lighter, easier to transport, maybe less expensive. Talk about the economic, the financial impact of using plastic pipe and plastic welding.
Jim Leary: Todd, that’s an excellent question because that really goes to the heart of everything, because what that’s going to do is it shows — metals have just skyrocketed over the last few years and plastics are less expensive to use, they are less expensive to install, they are safer in a lot of different ways.
So it saves the end users and the installers and contractors money. It takes less of a carbon footprint to dig out the trenches and to do all kinds of things like that.
So there is a multitude of levels that using plastic pipes has its advantages that works out in a number of ways and economically is one of them, the cost factor is a big one, as it is less expensive to use that.
Todd Schnick: Jim, I hate to say it but we are out of time. Before we let you go, how can people get in touch with you and, more importantly, where can I get more information of the good works at Widos Welding?
Jim Leary: Thank you very much for giving me the opportunity, guys, and you can contact us by going to our website at www.widoswelding.com and you will find a multitude of information and types of machines and services that we offer. And any type of questions you can go ahead and write on the website, you can query us and we will see those questions and we’ll reach back to you and get in touch.
Todd Schnick: Outstanding. Jim Leary, national business development manager for Widos Welding, it was great to have you. Thanks so much for making the time to join us.
Jim Leary: Thank you guys, and I appreciate the opportunity. You’ve been good neighbors. A little bit noisy sometimes. I thought I had some noise abatement going on, but you’ve been alright.
Todd Schnick: Well, we appreciate that. Alright, that wraps our final segment. On behalf of our guest Jim Leary, my cohost Todd Youngblood, all of us at Water Online radio, I am Todd Schnick.
It has been an absolute, sincere joy and a pleasure to broadcast to you here from Dallas and ACE 2012. We look forward to seeing you at ACE 2013 in the fine city of Denver. This is Todd and Todd, signing off.