Myths We've Heard About Lead Service Line Inventory, Replacement, And Funding
By Nya Dreyfuss
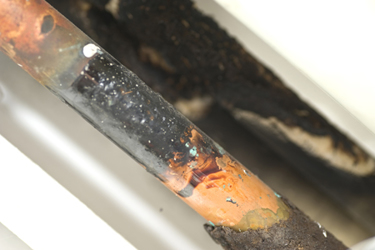
The U.S. EPA’s Lead and Copper Rule Revision requires that utilities report their Service Line Materials Inventory and prepare Lead Service Line Replacement Plans by October 16, 2024. At the same time, the Bipartisan Infrastructure Law will allocate $15 billion for pipe replacement over the next five years. As communities across the country work toward compliance and position themselves for funding, some common questions and some misperceptions are surfacing. Here are some of the top myths we are hearing about lead service line inventory (LSLI) and lead service line replacement (LSLR).
Myth: October 2024 is Far Away, Plenty of Time!
Fact: Record Gathering and Organization Takes Time
Paper utility records
If utilities had accurate, digitized records on service line materials, 24 months might be enough time. Service line records, if they exist, reside in multiple parts of the utility (e.g., billing and operations).
In our work with over 50 communities, we have seen illegible and waterlogged records. Just digitizing the paper as-built records or tap cards will take time. Some of these records are out of date, and many records are missing entirely.
Gathering records will be time-consuming, and it won’t be clear at the outset what is missing. Utilities need time to understand what is there and to fill in the gaps.
Fact: Getting Funding in Place Takes Time
Lead service line inventories and lead service line replacement takes funds. Applying for and obtaining funding, such as state SRF grant funds, takes preparation and time. Unfortunately, as current funding is not enough to replace every lead service line, getting organized to apply for funding sooner will help your utility obtain needed funds. Each state has application deadlines, as well.
Recommendation: Don’t Wait to Get Started!
We have heard some utilities delaying until they get more guidance from regulators, such as the Lead and Copper Rule Improvements (LCRI). While there may be more clarifications, the list of improvements for the LCRI is not focused on the inventory aspect of LCR compliance.
While there are many reasons to get started inventorying lead pipes, the most important reason is, of course, to find and remove lead from our drinking water infrastructure.
Myth: Water Samples without Lead Confirm the Absence of Lead in the Service Line
Fact: Corrosion control and sampling methods can prevent lead in service lines from showing up in tap water samples
Corrosion control is intended to prevent lead from getting into drinking water from lead pipes. This is a great outcome for drinking water quality. It means, however, that tap sampling cannot tell us the pipe material if the corrosion control is working properly or if the water sample does not allow for enough stagnation time.
Recommendation: Use Tap Sampling Data with Caution
Yes, pull all the data you have together as you begin your inventory process. No, don’t just take absence of lead in tap samples as absence of lead in the service line. The best information here is, of course, field verification, through a hydrovac or other device.
Myth: Inventory Delays or Competes with Replacement
Fact: An Accurate Inventory Increases LSLR Schedule and Cost Efficiency
The cost of digging in the wrong place to replace lead service lines is between $5K and $25K — and can delay actual replacements. Digging for lead and finding copper yields an expensive and useless hole, while someone with a lead line continues to live with the risk of lead exposure. Starting with an inventory of what’s where decreases the time to replacement for likely lead lines and the cost per successful replacement.
Fact: Inventory Work Does Not Need to Delay Replacement
Needing an inventory should not prevent a utility from getting started replacing lead. The inventory work (data organization and sampling at a representative set of homes) can occur in parallel with removing lead lines at locations expected to have lead.
Fact: Inventory and Replacement Plans are both Required by the LCRR
The service line inventory and the lead service line replacement plan are both due in October 2024. Neither is skippable.
Recommendation: Approach LSLI and LSLR as Interconnected and Iterative
While it may be simple to envision a materials inventory preceding replacement, in fact inventory is not just the first phase of a replacement plan. The inventory is a dynamic document: an inventory should reflect the current status of all service lines in the area, including those that have been replaced. In the same way, information gained from the inventory can be used to reprioritize the remaining locations in the community. Instead of a waterfall process — first inventory, then replacement — both are iterative and interconnected.
How To Prep And Conduct LSLI And LSLR
Don’t wait. The earlier you get started, the better off you will be for planning and funding. Use the data you have, but don’t trust your tap samples to give you the full picture. And treat both inventory and replacement as iterative, incremental processes.
These are a few of the myths and misconceptions we have heard. We are collecting more of these and will continue to bust them in future articles on our website. Keep an eye out.
Here are some key resources for utilities to get started on accurate and useful LSLI and efficient LSLR.
Inventory Resources
- The EPA’s August 2022 Guidance for Developing and Maintaining a Service Line Inventory provides best practices for data organization (PDF).
- The EPA Guidance references the 2020 ASDWA-BlueConduit whitepaper, “Principles of Data Science for Lead Service Line Inventories and Replacement Programs” (download link).
Funding Resources
- EPA page on Drinking Water State Revolving Funds
- For those utilities that do not have experience getting SRF grant funds, there are organizations in many states that help. One example is the Water Navigator program from the Michigan Municipal League Foundation.
Nya Dreyfuss is VP of Customer Success at BlueConduit (https://blueconduit.com/).