Membrane Filters Save on Separating Mixed Water-Chemical Wastes
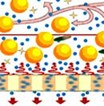
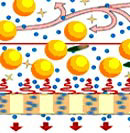
New Logic's VSEP filters generate very high shear forces on the surface membrane.
Recycling Centers of America, Inc. (RCAI, Lake Forest, CA), is getting its chemical separation act together and taking it on the road. The company says that switching to a new type of membrane filter slashed processing costs at its Portland, OR, re-refining plant by more than 50%. It has now begun to offer the same technology to chemical producers and recyclers.
"Our Aquadynamic Technologies subsidiary has two refineries in Oregon that recycle used motor oil and antifreeze," says RCAI VP Mike Davies. "We've been running the filters there and we know they work. They've cut our costs by more than half."
The filters, Davies explain, dewater the recycle stream prior to processing. "Take glycol," he says, referring to ethylene glycol, which is mixed with water to make antifreeze. "Recyclers ordinarily use distillation to separate water from glycol. That takes a lot of energy. Our new filters will knock out a majority of the water. They can then use the distillation unit for polishing only."
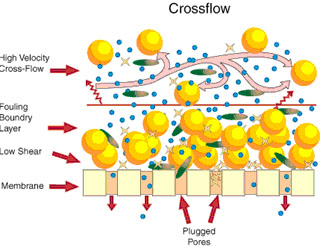
For recyclers, that means lower energy costs and, depending on the size of the filter, greater potential capacity. Chemical processors can use the technology to reduce waste water discharge, separate byproducts and sidestreams, or recycle valuable materials.
"What we want to do," says Davies, "is reduce the cost of waste disposal and recycling for our customers. We'll set a long-term contract, put up all the money, install equipment, teach them how to use it, reduce the amount of material we have to take away, and share in the savings.
"We'll take purified products and either resell them or recycle them to the customer. We're in brokerage business and we'll find a home for them. The customer has no risk," Davies concludes. He says the cost of the filters ranges from $200,000 to $2 million. Annual savings could range from $100,000 and $500,000.
RCAI uses VSEP (for vibratory shear enhanced processing) membrane filters developed by New Logic International (Emeryville, CA). "Historically," says Davies, "membranes have been the solution but you couldn't get enough volume through them. An industrial plant would need a football field of membrane filters. That's what different about the VSEP. They're self-cleaning."
Conventional membrane filters foul because of boundary-layer buildup on the membrane surface. Fouling reduces throughput and selectivity, and limits membrane systems to low-solids streams. Engineers circumvent the problem using tangential or cross-flow filtration, which pumps high-velocity liquid across the membrane surface to prevent boundary formation. This works for low-viscosity fluids. Unfortunately, it causes pressure to drop significant near the filter outlet, which allows fouling. Eventually, the fouling spreads towards the front of the filter.
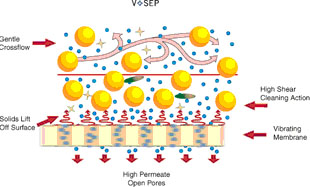
Instead of tangential flow, New Logic uses shear waves to solve the problem. Rather than blast feedstock through the filter, it moves slowly between leaves of parallel membranes vibrating in a direction tangent to the faces of the membranes. This produces intense shear waves that lift solids and foulants off the membrane surface and remix them with feedstock. The result, says New Logic, is a membrane with three to 10 times the throughput of conventional cross-flow systems. VSEP filter packs contain membrane leaves stacked like records on a record changer. A torsion spring works like the agitator on a washing machine to move the stack back and forth 0.75-1.25 in. peak to peak.
Operating at speeds too fast for the human eye to perceive, the oscillation creates shear forces of 150,000 inverse seconds (equivalent to over 200 G's) at the membrane surface. This is roughly 10 times the shear rate of the best conventional cross-flow systems, says New Logic.
More importantly, VSEP focuses its shear forces on the membrane surface, where it does the most good, rather than in the bulk fluid coursing through the filter cartridge. This allows VSEP filters to dewater high-viscosity liquids and slurries. The filters extrude concentrate between vibrating disc elements, expelling it once it reaches the desired concentration. This allows VSEP systems to treat a broad range of material in a single pass without additional working tanks, ancillary equipment, or associated valving.
According to New Logic, VSEP filters may eliminate prefiltration. They handle slurries with up to 70% solids (depending on fluid rheology); reduce power consumption by 90% compared to crossflow designs; use self-healing membranes that prevent breakthrough contamination; operate at temperatures to 175 F (to improve throughput) and over a wide range of pH; and have small footprints (a 500,000 g/d system fits on a 5 ft x 5 ft square).
According to Davies, New Logic and its licensee, Pall Corp. (East Hills, NY) have installed more than 200 units, mostly in waste water, pulp and paper, food processing, boiler water treatment, and industrial laundry. "They're saving customers lots of money," he says.
RCAI has begun to offer VSEP system services under an agreement with another New Logic licensee. "We've working with them to integrate this technology into our customers' operations," says Davies.
For more information: Mike Davies, VP, Recycling Centers of America, Inc, 23832 Rockfield Blvd., Ste. 275, Lake Forest, CA 92630. Phone: 949-609-0590. Fax: 949-609-0594.
Or: New Logic International, 1295 Sixty-Seventh Street, Emeryville, CA 94608. Phone: 510-655-7305. Fax: 510-655-7307.