Maximizing Value In WWTP Equipment, Parts, And Services
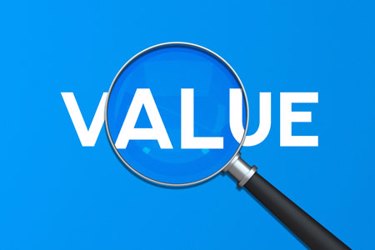
In the demanding environments of industrial and municipal wastewater treatment plants (WWTPs), even the best equipment needs some TLC every now and then. Still, recommended maintenance needs may be overlooked until a problem arises. Here is how planning ahead to evaluate the full range of options and the best choices for the task at hand can make a tremendous difference in both lifecycle cost and long-term equipment performance.
Repair vs. Replace – A Structured Decision
When the time comes to service or replace aging equipment, what questions should go into the repair vs. replace decision? After all, the options are not typically a binary choice but more like a decision tree where answers to the initial question might depend on different options in second, third, and fourth-tier considerations. For example:
- Is the equipment designed to be repaired/refurbished? In today’s world, many pieces of equipment are designed to be disposable. In an effort to minimize the up-front capital cost, many suppliers will not design and manufacture equipment that is robust enough to be refurbished after multiple years of service. Equipment designed with refurbishment in mind is likely to be built to higher standards that allow for long-term cost savings and a low total lifecycle cost.
- Is it worth repairing or refurbishing? Depending on equipment age and the issues involved, refurbishing the wearable parts could extend the effective lifespan of the original equipment by many years. A practical guideline is that equipment can be restored to its original anticipated lifespan for about 60 percent of the investment required for a new unit. An equipment supplier’s skilled service technicians can evaluate the equipment and propose refurbish/replace alternatives.
- If we choose to refurbish, what’s the best way to do it? Multiple options for equipment repair/refurbishment each come with their own advantages and limitations. Considering all the pros, cons, costs, and operational impacts can lead WWTPs to the right answer for each situation.
- In-House Refurbishment. Tackling a project with in-house employees can work if they have the experience and the time to accomplish it. Just remember that first-time repair efforts can result in unexpected delays that might conflict with normal maintenance or operational activities. Depending on complexity, WWTPs choosing this route should ask their equipment supplier about a ‘supervised rebuild’ with an experienced technician providing oversight and guidance to in-house workers.
- Factory Refurbishment. If backup systems and time permit, equipment can be sent back to the original manufacturer for repair or refurbishment. This approach offers the advantages of a complete disassembly and rebuild by OEM factory-experienced personnel (Figure 1).
- Onsite Turnkey Refurbishment. The option of a complete onsite retrofit performed by a skilled, factory-certified service team typically offers the quickest turnaround, minimizing out-of-service disruptions. Coordinating closely with the supplier before taking equipment off-line for service can further reduce disruptive impacts on process continuity.
Photos courtesy of Parkson
Figure 1. Rebuilding the wear surfaces of critical parts can extend the service life of existing equipment for a fraction of the cost of new equipment. Using experienced, factory-trained personnel and replacement parts generated from the original design blueprints will typically minimize project delays.
Solidifying Investments In Equipment Longevity
WWTP operators and maintenance teams can take additional key steps to maximize the value of their equipment investments. These include making maintenance, repair, and customer support issues part of initial capital equipment evaluations and comparing multiple options once refurbishment or repair is needed. Many of the key aspects of potential repair/refurbishment partners are outlined below.
- OEM Factory-Certified Replacement Parts. Properly specified parts are critical for dimensional compatibility and smooth operation. Factory-certified parts that are compatible with existing equipment will minimize schedule disruptions, downtime, and sourcing efforts when repairing older equipment — even if component manufacturers for commodity parts like bearings, motors, drive chains, etc. no longer supply the original SKUs (Figure 2). Single-source convenience for both commodity components (bearings, etc.) and proprietary parts means all refurbishment parts can be acquired with a single order without having to worry if they will fit.
Photos courtesy of Parkson
Figure 2. There can be a big difference between ‘factory-certified’ parts vs. aftermarket parts sold as ‘equivalent’, as anyone who has needed to replace generic sheaths prematurely can attest. Identifying wastewater equipment suppliers who offer one-stop shopping for a full range of aftermarket services — from factory-certified parts all the way to turnkey equipment installation, refurbishment, and repair services — helps to maximize the value of currently installed equipment.
- Continuity Of Equipment Coverage. One of the pitfalls in equipment maintenance is the disruption caused by mergers and acquisitions. Organizations that historically maintain their commitment to supporting the brands they acquire offer greater confidence for continuity long after the acquisition. For example, Parkson Corporation still offers all the services described here for each type of equipment in their family of brands — including American Bulk Conveying, Great Lakes Environmental, Hycor®, Lanco Environmental™, Meurer Research and Schreiber.
- Turnkey Installation And Repair Services. Not every wastewater treatment facility has the available time, staffing, and expertise to install or repair every piece of equipment in their plant. And not every installation contractor has the intimate knowledge of wastewater equipment or processes needed to assure flawless installation, repair, and operation on the first try. Suppliers who offer equipment, installation, commissioning, warranties, and repair services with single-source responsibility make it easier to minimize downtime and assure optimal operation without finger-pointing or delay.
- Service Maintenance Programs. For the maintenance of particularly critical high-wear equipment, consider the value of factory-trained field service teams who can provide onsite assessment of equipment performance and deliver periodic maintenance services, parts replacement, and repairs. Utilizing such services can provide better insight into operations, extend the life of equipment investments, and reduce risks of unplanned downtime or costly repairs.
Addressing Non-Mechanical Considerations As Well
Beyond OEM parts and installation services, look for other supplier capabilities that can help wastewater treatment equipment operate more smoothly and efficiently.
- Inventory Investments. Ask about the supplier’s investment in replacement parts and materials (Figure 3). The more comprehensive that capability, the greater the likelihood of quicker delivery once parts are needed.
- Operator Retraining. Even if equipment is working well mechanically, employee turnover might necessitate training for new hires. Equipment suppliers who offer aftermarket services for operations and maintenance training can help keep existing WWTP processes running efficiently.
- Process Equipment Evaluation. Having a dedicated Water Research Facility to bench and pilot-test equipment performance can help in identifying the best alternatives for changing processes or understanding performance capabilities of existing equipment.
- Geographic Coverage. Manufacturer service organizations with multiple regionally situated service offices can provide timely response and service (Figure 4).
Photo courtesy of Parkson
Figure 3. Sourcing OEM replacement parts for existing equipment can be difficult for brands that were absorbed by a larger company, unless the acquiring company makes a dedicated commitment to providing ongoing support. Parkson Corporation, for example, maintains a multimillion-dollar inventory of factory-certified parts for its original Parkson-branded products as well as acquired American Bulk Conveying, Great Lakes Environmental, Hycor®, Lanco Environmental™, MRI, and Schreiber product lines.
Graphic courtesy of Parkson
Figure 4. An equipment and service provider with dozens of skilled personnel stationed from coast to coast can provide more responsive coverage for onsite services such as inspections, maintenance, repairs, refurbishment, and retraining.
To Evaluate The Best Answers, Ask The Right Questions
For WWTPs with questions about the opportunities, costs, and advantages of evaluating aftermarket equipment and service options for any brand under the Parkson umbrella, complete information on the best options is available from aftermarket@parkson.com.