Matching Flowmeter Liners To Application
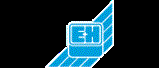
Increased process demands, both abrasive and corrosive, coupled with the increasingly harsh requirements of cleaning and sterilisation in the food and pharmaceutical industries, have given rise to a number of new electro-magnetic flowmeter liners and liner technologies. Liners in metal pipes electrically insulate the fluid from the pipe, allowing accurate flow measurement.
No single liner technology can be used for the entire range of nominal diameters from DN2 to DN2000, and each customer application is unique. Endress+Hauser has therefore adapted four different liner materials: rubber, polyurethane (PU) and two different fluoro plastics - polytetrafluoro ethylene (PTFE) and perfluoroalkoxy (PFA).
Historically, rubber has been the liner of choice and Endress+Hauser has decades of field experience with installing this type of liner. The process includes sand-blasting the metal pipe, applying a bonding agent and then the liner, inserting caoutchouc (natural rubber obtained from latex) matting, and then placing the measuring pipes in an autoclave, where the caoutchouc is vulcanised (at 145°C for three hours) into rubber. Rubber liner exhibits good chemical resistance against water and alkaline solutions, but is not suited to oils or acids and fails to meet the hygienic requirements of the food and pharmaceutical industries.
The most recent liner technology to be introduced by Endress+Hauser is the fabrication of PU liners with the aid of a rotational casting process. Casting moulds are mounted on the flanges, followed by the injection of the two basic components - isocyanate and polyhydric alcohol - into the rotating measuring pipe. Once these components set, the liner is poured through a nozzle. PU liner is particularly suited to the fresh water and wastewater industries.
To manufacture a PTFE liner, PTFE tubes are drawn into the steel pipes - with the exterior diameter of the PTFE tube being slightly larger than the interior diameter of the pipe. The range of applications for this liner is limited by the lack of a mechanical bond between the liner and the pipe wall. At large nominal widths, even small vacuum pressure puts an unbonded liner at risk of collapse. Conversely, the expansion of excessively high-temperature fluids could cause the liner to tear due to excessive tension. Nevertheless, PTFE liner exhibits good resistance to chemicals and high temperatures (-40°C to 130°C) and meets Cleaning in Place (CIP) requirements of the food industry.
One of the problems of PTFE liners is that during fabrication tiny micropores are generated in the liner material. If the fluid enters a steam phase, steam can diffuse through the pores and condense on cooling. If the fluid is re-heated the condensed water will expand into steam, causing the micropores to stretch. It is therefore preferable to opt for a PFA liner if a process involves both steam phases and frequent variations in temperature.
To manufacture a PFA liner, liquid PFA at 400°C is isothermically injected into the pre-heated mould. A pre-defined cooling temperature ensures that no micropores are present in the material. To reduce tension in the liner, the pipes are tempered in an oven for 24 hours. PFA liner is resistant to chemical and high temperatures (up to 180°C), meets CIP and Sterilisation in Place (SIP) requirements, and has received sanitary approval for Endress+Hauser's hygienic flowmeter Promag H.
With this variety of liners, Endress+Hauser can offer customers the most cost-effective and tested liner for each specific application. Where more than one liner material is potentially suitable, tests are carried out to determine the optimum choice.
Source: Endress + Hauser