Lean Techniques Can Help Improve Water and Wastewater Operations
By Emily Newton
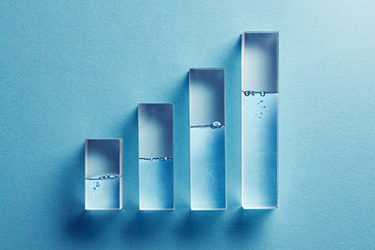
All the rage in the private sector, ‘lean’ principles — smoothing out processes to remove non-value-add parts — can also bring greater efficiency to utility operations.
Lean techniques, inspired by lean manufacturing, can help improve inefficiencies, reduce waste, and speed up output if the core principles are met. When they first entered the scene in the 1980s, they were very much tailored for the manufacturing industry alone. The concept has evolved over time, and many businesses now use it across a vast array of industries.
An area where it can really make a difference — yet is rarely implemented — is in utilities. Water and wastewater facilities can implement lean techniques to improve operations. Moreover, the paradigm is an excellent way to reduce operating costs, considering that water maintenance and management operations can be extremely expensive.
Breaking Down Lean
As presented by the Lean Enterprise Institute (LEI), a renowned purveyor of the concept, five key principles1 make up the entire strategy. Those are value, value stream, flow, pull, and perfection, and they often progress in that order.
- Define Value: Value is best described as what the customer is willing to pay for, and how you achieve that synchronization. Use qualitative and quantitative measures to discover and understand that value.
- Map the Value Stream: Mapping out the value stream includes identifying every factor that adds value. Anything that does not is considered waste. The idea is to identify nonessential waste, which can be avoided or reduced, and necessary waste, which is a natural byproduct of the value stream.
- Create Flow: You must create a reliable, mitigated flow, which becomes the general operation. Continue to focus on value-adding activities most of all, adapting your operation to prioritize a smooth process.
- Manage Pull: Managing or establishing pull involves limiting inventory, resources, and other items that often contribute to greater waste, like work-in-process (WIP) items. The pull system is specifically designed to empower just-in-time delivery and applications.
- Perfect the Process: The entire team must work together to eliminate waste and strive for complete perfection through consistent improvements.
You’ll need to develop a data collection and audit process2 to better understand these key principles and how they’re applied within your operation.
Of course, another pertinent question arises while reading these key factors. How does this apply to water and wastewater facilities?
Implementing Lean Techniques In Water And Wastewater
The overarching goal for any utilities provider or plant is to create as much value as possible while expending fewer resources. You’re trying to achieve maximum output with zero waste.
Work your way through your current operations, studying your business purpose, active processes, people, and performance. The key principles of lean can be implemented at each of these stages to improve the entire organization.
What is the purpose of the business? The company may be focused on revenue by providing a service or product, but what about the core values, mission, and vision? What else is the organization trying to achieve?
That purpose can be applied throughout the lean implementation to achieve more specific goals. Are you trying to make active processes simpler while using fewer resources? Would you like to see better output?
Taking that a step further, what existing conditions or applications affect the operation? For example, industrial water treatment is incredibly vital to manufacturing processes3 and any organization that utilizes a clean water supply. Could scale or corrosion buildup be interfering with your purpose and performance? What new policies can you enable to mitigate that problem? How can you do it without expending an inordinate number of resources and creating a host of new responsibilities and roles?
Concentrate on the people your operation serves, along with team members who create that value. Start collecting feedback that can be used to further improve activities. What inefficiencies have they identified? How can you remove those modifiers from the equation?
Finally, study and work to improve performance. Don’t just measure things in terms of output, but also consider your active goals, like waste levels, resource usage, and people’s demands. The focus during this phase would be community involvement4 and how the surrounding landscape can be improved to help the operation while reducing waste.
Parsing Lean Techniques To Improve Operations In Water And Wastewater
Anything that does not bring value to the operation or the people you serve should be immediately removed from the general process. That is the inherent goal of lean manufacturing. You can then focus on improving existing applications to further boost output, efficiency, and consumption.
In wastewater, this would entail taking a closer look at the entire business, from how and where water is collected to how it’s processed and beyond. What can be changed to improve that output and make the work far less costly and time-consuming?
The mean time to make repairs and confront failures plays a huge role in output and performance as well. When something goes wrong, what is the process for identifying and remedying the situation? That could be hundreds, if not thousands, of dollars of resources going to waste from spilled water during a pipe or system leak. The longer and more convoluted your maintenance process is, the more that goes to waste. That also applies to how your team administers support.
Getting a lean system in place means perfecting those smaller tasks to reduce completion time, improve success, and further bolster budgets. It’s not just about vague implementations across the board. It’s about really digging in to understand the entire operation and what can be done better and leaner.
References:
- https://www.lean.org/lexicon-terms/lean-thinking-and-practice
- https://www.jett.dormaj.com/docs/Volume8/Issue 4/Using Lean Principles in Water Maintenance Operations with Application to Water Treatment Plant.pdf
- https://www.chardonlabs.com/industries/manufacturing/
- https://revolutionized.com/sustainable-groundwater-management-guide/
About The Author
Emily Newton is an industrial journalist. She regularly covers stories for the utilities and energy sectors. Emily is also editor-in-chief of Revolutionized (revolutionized.com)