4 Keys To Adopting Industry 4.0 At Your Water Processing Facility
By Bryan Christiansen
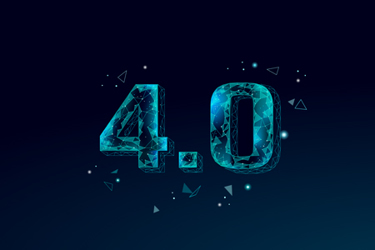
As the water industry continues to walk the road of digital transformation, here’s a step-by-step guide to help utilities keep pace.
Using modern technology to automate processes and equipment in facilities has proven to be beneficial. Successfully integrating digital technology reduces operational costs and streamlines workflows. It also enhances the quality of water treatment and distribution processes.
There is increased pressure on water facilities to serve a growing population. Most of them use aged equipment and distribution networks. That, along with climatic changes, complicates operations in the water sector. Water processing facilities are embracing Industry 4.0 to address these challenges.
Industry 4.0 combines different, interoperable technologies. The digital solutions work in unison to improve the productivity of water facilities. Popular Industry 4.0 technologies for water processing facilities include:
- The Industrial Internet of Things (IIoT)
- Cloud computing
- Blockchain
- Big Data analytics
- Artificial intelligence (AI) and machine learning (ML)
Industry 4.0 revolves around data. Companies utilize data for process improvement, asset management, and performance optimization. Some of the benefits of Industry 4.0 in water facilities include:
- Increasing the efficiency of available water treatment and distribution resource
- Combating water scarcity
- Using innovative upgrades to old water processing and distribution systems
- Predicting floods and droughts and their impacts on water reserves
- Doing real-time analysis of water quality
- Centralizing the management of the workforce and dispersed water equipment
- Reducing operational costs and increasing revenue by using smart meters, leak detectors, and SCADA systems to eliminate nonrevenue water
The adoption of Industry 4.0 in different sectors is expected to grow further as digital technologies mature. The water industry is keen on leveraging digitization to adapt to global water challenges. Industry 4.0 ushers in innovative water management solutions. How can water facilities successfully implement Industry 4.0 in their operations?
1. Identify opportunities for automation with a quick return on investment.
There are endless opportunities for automating water facilities. Some technologies require a short time to implement, while others take time to mature and yield visible results. The variation in implementation timelines depends on the sophistication of technology, cost of acquisition, and availability of expertise. Water facilities that successfully undergo a digital transformation during the early stages of implementation have an easy time upscaling and introducing newer technologies for water management.
Once the company decides to adopt Industry 4.0, the management needs to conduct a facility-wide audit of equipment, processes, and personnel. They must identify the prevalent challenges and suggest relevant technologies to resolve them. The facility then initiates a pilot program and begins automating a small section of processes or equipment.
The company uses the pilot digitization program to collect data on the relevance of various solutions. They evaluate the early success of the pilot program and identify possible bottlenecks or challenges that can derail future implementation. The water facility leverages the lessons from the pilot program to draft policies for full-scale implementation of Industry 4.0 and measures for prioritizing subsequent automation of processes or equipment.
2. Develop a long-term implementation strategy.
Industry 4.0 is a combination of diverse digital technologies with varying levels of success in the water industry. Water processing facilities may shun new technologies out of fear of failure. The most common cause of failure is a lack of a long-term implementation strategy. The challenges of the water sector, like digital technology, are dynamic and change by the day.
Companies aiming to adopt Industry 4.0 must establish a robust implementation strategy and increase the probability of success. An implementation strategy defines:
- The cost of acquiring and maintaining digitization tools and technologies
- Short-, medium-, and long-term digital transformation goals
- Implementation timelines
- Scale and quality of implementation
- Innovative measures for addressing arising challenges during the implementation phase
- Guidelines for prioritizing technology and processes for automation
- Indicators for measuring the success of adopted digital solutions
Water facilities require access to relevant data when developing an Industry 4.0 adoption strategy. They can utilize data from their operations or evaluate how companies from other industries managed their digital transformation. The implementation strategy should estimate the success rates and possible failures likely to accompany digital technologies. The facility must be ready to embrace the different outcomes of digitalization.
3. Train your employees.
Employees are a critical ingredient when implementing technological solutions in the water sector. They understand the shortcomings of different water industry operations. Water processing facility employees provide feedback to improve workflows, streamline equipment maintenance, and eliminate waste. When a company resolves to adopt Industry 4.0, it must engage the employees and provide requisite training to enable them to exploit advanced digital tools or solutions.
Training sessions are instrumental in driving a culture shift among employees. It is common for experienced workers to shun digital technology over fears of job losses or salary reduction. A well-structured training session is a powerful utility to convince employees of the benefits of new technology. Gaining buy-in from all levels of the organization improves the adoption and implementation of Industry 4.0 solutions.
Water facilities use training sessions to showcase the technical capabilities of different solutions. Field and office workers demonstrate their comprehension of the digital tools and provide feedback for improving them. Such inclusiveness boosts employee morale and enhances the integration of solutions to routine activities. The early success of digital solutions manifests as better productivity and visibility of operations.
4. Continuously explore opportunities for improvement.
Adoption of Industry 4.0 follows a continuous learning path. Apart from streamlining routine operations, the facility should focus on achieving excellence in water management. Industry 4.0 technologies collect vast amounts of data critical for decision-making and operational improvement. The availability of accurate computerized maintenance management software (CMMS) data improves predictive maintenance of assets, real-time monitoring of water processing systems, and better communication with customers.
Water facilities can enhance the success of Industry 4.0 by systematically updating digital tools and exploring opportunities for integrating advanced solutions like blockchain for water management. Evaluating the performance of each technological solution enables the company to identify its efficiency. That way, the facility can scale up the implementation of high-value digital solutions. Continuous improvement involves periodically training employees to upskill them and acquaint them with changes in digital technology.
Summing Up
Industry 4.0 is the next big thing in the water sector. The potential of the different technologies will change the fortunes of the companies in the water sector, enabling them to compete favorably against other industries. Companies can enhance the success rates of new technology through a culture shift, strategic implementation, training, and continuous, data-driven improvement.
About The Author
Bryan Christiansen is the founder and CEO of Limble CMMS. Limble is a modern, easy-to-use, mobile CMMS software that takes the stress and chaos out of maintenance by helping managers organize, automate, and streamline their maintenance operations.