Is Your Current Excavator Up To The Challenge Of Modern Water Projects?
By Emily Newton
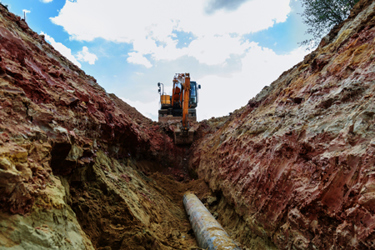
Digging may seem rudimentary, but there are important factors to consider for improving costs and outcomes when renewing pipelines and other water infrastructure.
The excavator is an essential piece of water utility equipment. Due to its importance, some decision-makers determine it is time to modernize their excavators to meet the demands of current or upcoming projects. Which factors should they consider when assessing whether their current models are up to the task?
Digging Depth Per Day
Project managers should start by calculating how much digging will occur during an underground utility construction project per day. That is a practical way to figure out whether a current excavator’s size and capabilities will fit the job. Some experts say the daily digging depth could become a deciding factor in whether a decision-maker chooses a 50,000-ton or an 80,000-ton model.1
However, decision-makers should consider other factors, such as the project’s water pipe depth and if the excavation work will happen in a heavily trafficked area or a more remote location. One best practice is to select an excavator that is as small as possible and can still complete the required task.
Even so, some prefer larger machines in almost all cases because they can move more dirt at a lower cost per yard than their smaller counterparts. Many individuals overseeing utility construction projects understand that time is money, and they do not want to waste hours trying to use insufficient equipment.
Another tip is to review data from past excavation projects to see how quickly the earth-moving activities occurred in those cases. How did the past depth-per-day metrics compare to upcoming projects? Such evaluations can determine if a company has suitable equipment or needs to obtain more capable options before work begins.
Age And Total Operating Hours
The total time in service is another aspect to consider when determining if it is time to update water utility equipment. In one example from India, decision-makers chose to replace all heavy machinery — including some track excavators — after using it for 15 years.2 That strategy may work well for some organizations. Still, others will find it overly broad or not well-aligned with their financial resources.
A more practical approach is considering age and operating hours alongside other more specific parameters. For example, has it become especially difficult to source replacement parts for some older excavators in a fleet? If so, replacing those machines with newer options may make sense from a financial and time-based perspective.
Does historical data indicate a utility company’s older models are significantly less energy-efficient than newer models available on the market? The money saved with upgraded equipment could quickly make the replacement costs worthwhile.
That said, older, adequately maintained equipment could last as long as newer equipment that rarely or never gets the required maintenance. Some necessary procedures are time-based, making it important to do them on the recommended schedules. For example, people should change their excavator’s final drive motor oil annually or after using the equipment for 100 hours.3
Similarly, relying on poorly trained or careless operators could result in parts wearing down faster than expected due to aggressive behaviors or usage mistakes. Those supervising underground utility construction projects should keep records of how long equipment stays in functional condition. After noticing excavators do not last as long as expected, they should assess all contributing factors. The results will help them evaluate how much equipment age impacts performance.
Energy Source
Many excavators are diesel-powered machines, so overall water utility equipment costs will include the fuel required to run the machines. Since older models may be less efficient than newer ones, operators may determine that those using less diesel during typical workdays are more appealing than those requiring comparatively more energy.
However, electric excavators are becoming more popular and accessible, especially among decision-makers who want to make their utility construction projects as sustainable as possible. One innovative example comes from a proof-of-concept project for an eight-ton excavator.4
It involves a modular battery-electric system that allows users to convert diesel-powered machines into zero-emissions models.
Additionally, this technology allows people to benefit from equipment with the precise battery capacity required for individual jobs. That is because the system enables fleet managers to attach the appropriate number of modules to provide the estimated energy needed for each day’s projects. This option could become more cost-effective than traditional possibilities because it prevents users from paying for unnecessary battery capacity and adding to overall project costs.
Some leaders have investigated other eco-friendly power sources, such as excavators that run on hydrogen fuel cells. Although these are less common than electric options, they are becoming more widely available.
Water project supervisors should consider calculating the average amount of diesel used across all excavators. The result will make it easier to determine the cost-effectiveness of switching to emissions-free power sources for some or all machines in the fleet. They should also research whether grants or other green energy programs could make the cost more affordable and manageable.
Reliability
Assessing a current excavator requires users to account for all recent occurrences where the equipment failed or introduced project inefficiencies. If such instances become more frequent, the worsening issue is strong evidence that the excavator is no longer reliable enough to use regularly.
Having the financial resources to cover the upfront costs of a newer model is not always a necessity. Leasing agreements typically allow people to spread the equipment expenses over periods as long as a decade.5 Then, they can benefit from new excavators without spending so much at once.
Safety concerns could also convince those leading underground utility construction projects that current excavators have become too unreliable to continue using. Excavators and other heavy equipment are inherently dangerous. However, inadequate maintenance or faulty parts also pose dangers. Main control valve problems can make excavators unexpectedly stop moving or move too slowly. Such erratic behavior could endanger operators and others nearby.
Injuries and fatalities could bring attention to water projects for all the wrong reasons. Excavator modernization is one factor contributing to safety and reliability, but operators must also pay attention to other contributing elements, such as training and choosing an excavator capable of a particular job.
Excavator Type
A common question surrounding underground utility construction projects is whether operators should use wheeled or tracked excavators on the site. Tracked excavators have a lower center of gravity and bigger surface area than wheeled types. These characteristics make tracked models comparatively more stable and better for muddy or slanted surfaces. Wheeled excavators are road-friendly, ideal for working on paved surfaces or in cities.
Wheeled excavators also move faster and are more maneuverable than the tracked type. A potential downside is that their digging depth is less than what tracked models achieve due to the wheels that keep the machine higher off the ground.
Tracked excavators may require less maintenance in rugged conditions due to the track’s durability. The track is less prone to punctures from debris often found on construction and infrastructure sites. The maintenance expenses associated with wheeled models vary due to factors such as the manufacturer’s design and the wheel system’s complexity.
Nondestructive excavators are also popular options for water utility equipment. These possibilities combine high-flow vacuums and high-pressure water, allowing people to accomplish excavation tasks more safely and with fewer infrastructure disruptions.6 Features such as adjustable water pressure and remote-controlled suction booms also give operators excellent control, helping them work around existing underground utilities when needed.
Choose The Appropriate Excavator For Upcoming Water Utility Projects
Is the best excavator currently in the fleet, or is it time for an upgrade? These discussion areas will help people make confident choices, whether considering single projects or all those they expect to tackle during the upcoming months and years.
References:
- https://www.heavyequipmentguide.ca/article/39307/how-to-select-the-rightexcavator-for-sewer-and-water-projects
- https://thenewshimachal.com/2023/12/state-pwd-modernizing-fleet-phasingout-aging-vehicles-for-cleaner-roads/
- https://precisionfinaldrives.com/blog/how-to-maintain-your-minicompactexcavator-/
- https://electrek.co/2024/01/26/moog-modular-battery-concept-for-heavyequipment-is-too-smart-to-ignore/
- https://revolutionized.com/equipment-leasing/
- https://www.pipeliner.com.au/abletech-underground-trailblazing-the-use-ofnon-destructive-excavation/
About The Author
Emily Newton is an industrial journalist. She regularly covers stories for the utilities and energy sectors. Emily is also editor in chief of Revolutionized (revolutionized.com).