Instrumentation And Digital Transformation

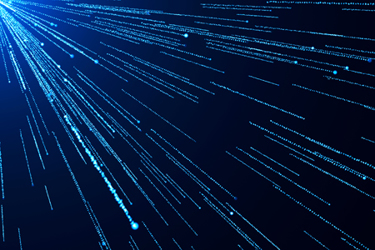
Whether you call it Digital Transformation, Water 4.0, or Smart Water, the water industry as a whole is changing drastically in the way that it operates. If you ask a dozen people what these buzzwords mean, you will naturally get a dozen answers. It is because the Digital Transformation of the water industry is different for different people and for different operational and management aspects of what is done to produce water, distribute it to customers, collect it, treat it, and put it back to the environment.
From an operational point of view, we have to know what is going on within the water & wastewater system, and we have used instrumentation to tell us what the situation is for years. So, what is new? Why should we digitally transform? What does it mean? It is a fact that the water industry has been monitoring its assets for years. It is a fact we monitor what the customer uses for billing purposes, but it is also a fact that the vast majority of the data that is collected is either collected in the wrong way or the data itself goes to waste as its use has never been well-defined. This is the general state of the water industry at the current time. In recent years, we have heard about data mining, Big Data, and a plethora of techniques that can provide insights and realise value in the data we collect. To me, this is where the Digital Transformation of the water industry starts, as there is a huge value in the data that the industry collects as long as that data is right. Of course, the major source of data (but not the only one) is in the operational instrumentation that is out in the field and this is the subject of a recent paper that has been written for the International Water Association.
Within Digital Transformation instrumentation is the source of data and, according to the SWAN Layers Diagram, it represents Layer 2 sitting on top of the physical infrastructure layer. What we as an industry quite often don’t think about is that the underlying layer in the SWAN Layers is vital for the layer above. So naturally, as the bottom-most layer in the concept of “Smart Water”, the layers representing telemetry & communications, visualisation, and analytics have no place without the successful implementation of the instrumentation layer.
From this we can conclude that instrumentation is a fundamental part of the Digital Transformation of the water industry as it is where the potential begins and is the fundamental source of where data come from. Instrumentation is present throughout water & wastewater systems and ranges from the use of smart meters at a customer’s premises to what amounts to industrial instrumentation systems on the various network and treatment work systems within the water industry.
All the examples of where Digital Transformation has succeeded in the water industry so far have been based upon three basic tenants:
- Good quality data from properly installed instrumentation;
- A basic knowledge of the uncertainty of the data; and
- A robust instrumentation maintenance processes, making sure that instrumentation accuracy is maintained.
Conversely, it has been poor quality data, from either poorly installed or poorly maintained instruments, that has resulted in the failure of some of the most promising Digital Transformation projects.
For any Digital Transformation project to succeed, a data and information strategy needs to be put in place. This strategy can be in a specific area, such as non-revenue water, or in a more generalised company-based operational area. An example of this is in the Global Omnium Digital Twin model built for the City of Valencia (Conjeos,2020). This application-specific Digital Transformation project saw instrumentation installed along with dual redundancy on telemetry outstations, coupled with an understanding of the accuracy of the instrumentation using general uncertainty principles. This has allowed the construction of a hydraulic digital twin that enables operators to not only understand the system performance, but to use the system to predict future outcomes. Such functionality can only be achieved using accurate instrumentation, which is ideally coupled with the instrumentation meta-data to provide full functionality of both visualisation and analytics.
Clearly, with the right instrumentation, situational awareness of the system can be achieved, thus facilitating informed decision-making, which is where the value exists for companies within the water industry. As an industry, we know that accurate instrumentation is an absolute must but does not always exist. Why not? Is this due to resistance to the effective use of instrumentation?
Resistance To The Effective Use Of Instrumentation
Resistance to the effective use of instrumentation usually starts when instruments are not installed correctly or have been installed for little or no purpose. In these circumstances, there can be a perception that an instrument is not correct which, in turn, leads to lack of maintenance of the instrument and, therefore, additional wrong measurements.
This leads to a vicious circle where the instrument provides inaccurate or useless data — and therefore useless information — and is consequently abandoned. The risk in this approach lies in the use of incorrect data, which, in some cases, can cause poor control of the treatment works and result in regulatory issues.
The root causes for a lack of trust in instrumentation are:
- Instrument reliability – There is resistance to the use of instrumentation to full effectiveness, as it is perceived as unreliable. This can be true if an instrument was badly installed or installed in the wrong place. However, in other cases, the instrument reliability is compromised by poor maintenance;
- The threat of instruments – The perceived threat that instrumentation and automation will be used to retrench or replace the workforce. On the contrary, instrumentation should be a tool for operators to operate more efficiently by reducing the time spent manually analysing samples;
- Over-design of the automation system – The design and then use of instrumentation so that the system is over-complicated and un-operable. This causes a gap between the design engineer and the user;
- Poor use of current data and poor data management – Instrumentation that is currently in place at treatment works normally feeds through to a SCADA system. However, the vast majority of data that the instruments produce is generally not used, leading to “data richness, but information poverty”;
- A lack of understanding of what instrumentation can achieve – There is generally a poor knowledge over what instrumentation can achieve to deliver process control/advanced process control. Poor integration of the current instrumentation leads to the loss of most of data and information that instrumentation produces, which results in poor efficiencies in current process control and the inability to utilise the instrumentation to its full effectiveness;
- Lack of trust in instrumentation – Instrumentation is not trusted from the operator level to the corporate level, or at the regulatory level; therefore, it cannot be used for regulatory compliance.
All of these examples cause barriers to the effective use of instrumentation and lead to poor confidence in adoption of the systems that will generate the data to support Digital Transformation. The experience of these barriers has led to the development of the instrumentation lifecycle philosophy.
The instrumentation lifecycle has five stages. These are intended to take the designer and operator of instrumentation through the operational life of an instrument and highlight early-on issues that could cause problems in the future. The first three stages of instrumentation lifecycle assessment are to help users think about the process of instrumentation and understand the value that an instrument brings. The five stages are illustrated in Figure 1.
Stage 1 – Instrumentation Purpose
The first stage defines what an instrument is going to be used for in the water or wastewater system, the data it will produce, and how this is going to satisfy an information strategy, thus addressing and clarifying the real application of the instrument. The reason why an instrument is needed could be multiple, including (but not limited to):
- Regulatory
- Financial
- Monitoring/Alert purposes only
- Asset Monitoring or Protection
- Control Purpose
Stage 2 – Instrument Specification
The second stage is the instrumentation specification and selection. For this, it is important to understand:
- What parameter is the instrument meant to measure (level, flow, temperature, state)?
- How is it meant to measure it? What technique is going to be used? What is the accuracy requirement? In what range it needs to operate? What is the required response time and measurement frequency?
- What is the application (e.g., in the network, on the inlet or outlet of the treatment works)?
- What are the physical constraints of the measurement location?
- What are the power and communication requirements?
- How is the instrument going to be operated and maintained?
- What are the sample conditioning requirements such as sample delivery, filtration, and sample preparation, and how this going to affect the measurement?
- What are the costs involved in the purchase and the operation of the instrument (e.g., ongoing chemical cost and/or ongoing consumable costs)?
- What are the legal limitations of installing the instrument? If some legal schemes are in place, the instrument may have to reflect this limitation.
The examples in this list, albeit not exhaustive, can have a significant impact on whether and how an instrument is installed.
Stage 3 – Instrument Installation
The third stage is to consider the instrument installation and how this is going to be achieved, including ability to access, verify, calibrate, maintain, and replace. This is an iterative process, as an instrument may be ideal in terms of specification but not installation requirements.
At this stage, it is also vitally important to understand how the instrument is going to be maintained and eventually replaced. At the end of the instrumentation asset life, where flows are passing through the works, replacement will result in significant disruptions and cost implications. If future replacement is considered prior to installation, the cost of the instrument and its replacement can be significantly less in the long run. Therefore, putting together an operational maintenance and instrumentation replacement plan is worth the investment in time.
Stage 4 – Operation
The fourth stage is the operation and maintenance of an instrumentation system. This should include an operation and maintenance plan based upon the manufacturer’s guidelines and adapted based on practical evidence including:
- Instrumentation cleaning frequency and methodology of how to achieve proper cleaning;
- Instrumentation end-to-end testing;
- Instrumentation calibration versus instrumentation primary verification;
- Instrumentation secondary verification techniques; and
- Instrumentation consumables (chemicals, wipers, etc.).
The operation and maintenance phases are circular during the life of the asset and can be measured using primary and secondary verification to predict when an asset is likely to fail.
Stage 5 – Review & Replace
The fifth stage begins as the instrument is about to fail and comprises the review of its lifespan, its usefulness, and whether and how it is replaced.
In summary, the instrument lifecycle is a tool that is used to ensure the accuracy of instrumentation. This is absolutely vital within the Digital Transformation concept as the majority of projects have failed due to poor-quality data.
Even from this summary article of the International Water Association white paper, we can see that instrumentation is a fundamental part of the Digital Transformation of the water industry. For those of you who would like to find out more detail, please read the full white paper written by Oliver Grievson of Z-Tech Control Systems and Water Industry Process Automation & Control on behalf of the International Water Association. The paper can be accessed for free at https://iwa-network.org/publications/digital-water-the-role-of-instrumentation-in-digital-transformation/.