How To Save Time, Save Money With Pilot-Plant Testing
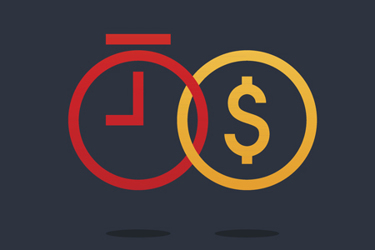
When developing water or wastewater treatment processes for entirely new applications or modifying existing processes to accommodate changing water characteristics or regulatory discharge requirements, understanding capital investment, operating cost, and long-term performance is critical. Here are several ways to view pilot plant or lab-scale testing as viable approaches to better outcomes with lower risks.
Taking Stock Of The Challenge
Not every feedwater or wastewater treatment application requires a full-blown pilot plant test. But there are many cases — especially in challenging industrial and municipal wastewater applications — where having the confidence instilled by pilot test results can accelerate success for manufacturing companies, their consulting engineers, and the equipment/systems suppliers.
- Dealing With Different Streams. Even with municipalities or corporations that run the ‘same’ process at multiple locations, the same treatment regimen might not yield identical results every time — due to differing source water composition, equipment, or even chemical-treatment suppliers.
- In areas concerned about water conservation, waste streams might be more concentrated due to reduced water use in industrial production and clean-up processes or impacted by low flow restrictions imposed by communities.
- In cases where sustainability is a particular concern, testing might need to address objectives for conserving heat and energy or for removing heavy metals, process additives, or other components before treated water can be recycled back into the process.
- In cases where industrial wastewater has the option of being discharged to a local municipal treatment plant, proper pilot plant testing can help to determine whether to:
- treat wastewater sufficiently to meet municipal utility requirements (e.g., < 300 biochemical oxygen demand and < 300 total dissolved solids) without paying a surcharge or
- treat it all the way down to federal or state regulatory levels for direct discharge to the environment.
- Dealing With Uncertainty. When dealing with a new or significantly changed process or waste stream, the likelihood of uncertainty is typically higher. Lab-scale or pilot plant testing can pay for itself by eliminating the least-effective treatment options and helping to quantify the impacts of new variables and justifying the optimal cost-effective alternatives (Figure 1). Complex or highly variable processes — such as those involving food, pulp and paper, mining, plastics, petrochemicals, heavy metals, and others — often present the types of challenges that warrant specific lab-scale or pilot plant testing. At the municipality, pilot testing variable flow rates can be incredibly valuable.
- Retrofit Applications. Pilot plant testing can offer significant advantages when retrofitting treatment trains due to new production processes or a tightening of regulatory requirements. In certain cases, it can even demonstrate that some of the original treatment system equipment can still be retained within the new design — at significant capital expense (CAPEX) savings.
Photos courtesy of Parkson
Figure 1. Whether using lab-scale or pilot-plant testing, be sure to consider treatment impacts at each potential stage of treatment — clarification (left), aeration (center), biosolids handling (right), etc. — to see where certain treatments or chemical applications can be most effective. Being able to do so can result in building a smaller, more compact system with lower operating expenses.
Overcoming Objections
Wastewater generators and wastewater treatment operations that have not used lab-scale/pilot plant testing, or have tried it without a comprehensive strategy, often have the same objections:
- It’s Too Expensive. Compared to the cost of installing a full treatment system that eventually requires costly modifications, properly constructed pilot plant testing can pay for itself in relatively short order. That includes the potential for CAPEX savings, lower operating expenses (OPEX), lower total lifecycle costs, and minimizing costly penalties for exceeding discharge compliance requirements. Work with suppliers to identify the overall ROI for tested alternatives.
- It Takes Too Long. Developing a structured testing protocol is key to a well-planned pilot test that can be run in a matter of weeks. And when a multifaceted test protocol is well planned out and methodically run, it can deliver far greater insights than just a go/no-go option — without significant additional testing time. In certain cases, lab-scale testing alone might be able to deliver the needed insights.
Both of those concerns can be diminished by having a good Q&A discussion with the pilot plant supplier to establish an understanding of the testing and reduce its duration. Developing protocols that clearly define objectives and parameters can enable pilot tests of consistent water streams to run their course in just a few weeks. With wastewater streams that fluctuate periodically — as frequently occurs with food or chemical processing applications — well-planned testing might need to run for a slightly longer time or in several waves to cover all levels of wastewater demand.
Photo courtesy of Parkson
Figure 2. Developing pilot-test protocols that evaluate multiple permutations of equipment and chemical options makes it easier to find the most cost-efficient treatment solution up front, rather than trying to fine-tune full-scale equipment after installation. For example, this automated, skid-mounted Lamella® gravity settler and thickener unit lets users test various concentrations of chemical treatment in various stages of treatment to target the optimum treatment approach for heavy-metals removal.
Setting Goals
Developing testing processes as a series of steps to answer different aspects of concern is important for creating multiple levels of options, not just one take-it-or-leave-it proposal (Figure 2). The key to good insight lies in both the preparation and follow-through of the approach taken — lab-scale or pilot test.
- Plan Ahead. Work closely with suppliers who have both the experience and the portable pilot plant equipment for all relevant aspects being studied to anticipate, hone in on, and quantify the most viable treatment methods.
- Map out testing strategies ahead of time. Consider a broad range of parameters (e.g., total solids, total suspended solids, volatile solids, turbidity, alkalinity, pH, material composition, etc.). Also, schedule pilot testing to run under the most-challenging scenarios.
- Agree on what parameters will be covered in the test reports. Avoid surprises by spelling out expectations for test methodologies, preliminary findings, conclusive results and recommendations, and even recommended sizing of full-scale equipment.
- Evaluate financial as well as chemical/biological implications. Create test parameters that can help to quantify both the best physical treatment options and total lifecycle costs for equipment, chemical treatment, dosing levels, etc.
- Lab-Scale vs. Onsite Pilot Testing. Consider lab-scale testing to qualify treatment alternatives. But for applications with complex or highly variable conditions, explore onsite pilot plant testing to confirm actual results under real-world conditions (Figure 3).
- Don’t Limit The Scope Of Possibilities. Use lab-scale or pilot testing to evaluate the full spectrum of treatment demands and influencing factors — such as pH adjustment prior to clarification and biological treatment or effluent polishing after primary treatment.
Photo courtesy of Parkson
Figure 3. Mobile pilot plants can be configured to meet specific application parameters. They provide a convenient way to evaluate physical and financial impacts of specialized treatment protocols.
What To Look For In A Pilot-Plant Testing Supplier
Obviously, having the right equipment for testing that imitates the real-life challenge is essential. But beyond that, be sure to ask about the supplier’s experiences with similar applications, as well as their ability to tailor lab-scale or pilot plant protocols to evaluate as many variations as needed. For example, the Parkson Water Research Facility provides both laboratory and full-scale pilot testing (Figure 4) to ensure that proposed systems can perform to a client’s specific needs — complete with associated ROI calculations. Buyers should also encourage system suppliers to provide perspectives on both the CAPEX and OPEX considerations of each treatment alternative. And, finally, work collaboratively with suppliers who ask insightful questions to focus the scope of testing for quicker, more reliable results. For information on how Parkson’s lab and pilot testing capabilities (shown here) can help, contact a water treatment expert to discuss options and how we can help you.
Photos courtesy of Parkson
Figure 4. Dedicated research facilities provide the ability to pilot-plant test advanced treatment technologies in conditions similar to the ultimate end-use application. This mobile DynaSand® EcoWash® unit at the Parkson Water Research Facility quantifies the ROI on effective chemical treatment for precipitating solids and on proper filter size and configuration to accommodate desired flow rates.