How Industry Is Solving Its Water Supply Crisis
By Tom Iseman and Brian Arntsen
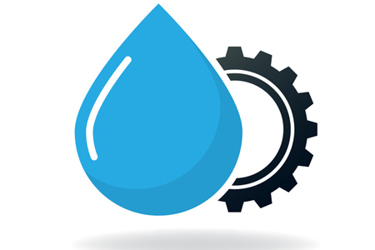
Every smartphone, every beverage, every manufactured product in America depends on water. Industry consumes nearly 20% of global water supplies, making it the second-largest water user after agriculture. For decades, this massive consumption followed a simple formula: Withdraw fresh water, use it once, discharge it. Companies built facilities near abundant water supplies, including lakes and rivers or municipal utilities with excess capacity, and considered clean, reliable water as an unlimited resource.
That approach is impossible to sustain as the world grapples with water scarcity. Multiple pressures are converging to transform water from a readily available, low-cost input to a variable and constrained resource. Companies recognize risk to their operations, as well as obligations to the communities in which they work and their employees live, and they are increasingly investing in stewardship and preservation of water. This entails work not just on their facilities, but in conjunction with multiple stakeholders, including municipal utilities, agriculture, and environmental groups. In short, water stewardship has become far more critical and complex for industry.
The most dramatic pressure comes from explosive demand growth in water-intensive sectors. U.S. hyperscale data centers are projected to consume 124 billion liters of water by 2028, more than doubling their 2023 usage of 55 billion liters. This surge reflects artificial intelligence and high-performance computing demands that require massive cooling infrastructure. Simultaneously, the push for a domestic manufacturing renaissance means more industrial facilities competing for finite water supplies.
Corporate sustainability mandates have evolved from aspirational goals to hard targets, and many major companies face 2030 deadlines for achieving water neutrality. This external and internal urgency is transforming water reuse from corporate social responsibility to operational necessity.
Leading The Transition
Companies are using a range of strategies and recycling technologies to address water risk, including siting decisions, climate modeling, and water use efficiency. The food and beverage sector has been a leader in industrial water reuse adoption, with major companies implementing comprehensive water reuse strategies to safeguard operations and reputations in drought-stressed regions.
Regional examples demonstrate how water availability drives rapid adoption. California recycles more than 1 million acre-feet of water annually, and Scottsdale, Arizona, is home to one of the most sophisticated recycled water facilities in the world, with 13 area golf clubs footing the bill for maintenance, operation and capital costs. The movement is spreading to other water-stressed areas. In Corpus Christi, Texas, which is reportedly at risk of running out of water by spring 2027, the city council is exploring selling reused wastewater to industrial customers. Indiana is now requiring registration for facilities withdrawing over 100,000 gallons daily, and Ohio is implementing permit requirements for large withdrawals from the Lake Erie watershed.
The momentum extends beyond individual initiatives. The Water Reuse Action Plan has grown to include over 70 actions and 170 action leaders since 2020, with increasing focus on industrial applications. Organizations like Climate Adaptive Infrastructure provide a financing model to help industrial facilities with the capital expenditures required for reuse.
The Available Technology
Water reuse technology has made major strides in innovation, performance, and value to meet the high standards needed for industrial reuse.
Solutions have standardized around membrane bioreactor (MBR) systems coupled with reverse osmosis (RO) treatment and brine management, since brine, also known as RO concentrate, is a byproduct of RO. Industrial reuse requires exceptionally clean water — far cleaner than typical wastewater discharge standards — because the treated water must meet specific process requirements for cooling systems, boiler feeds or direct product contact. MBR technology provides the reliable pretreatment necessary to produce high quality water to feed RO systems, which then deliver the ultra-high-quality effluent that industrial processes demand. This two-stage approach has become the industry standard because attempting to run RO systems without the proper pretreatment leads to fouling and system failures.
Technical complexities around brine management create additional challenges. Concentrate streams from advanced treatment contain high dissolved solids, requiring specialized handling. Some facilities implement a dynamic RO process to maximize water recovery; others go as far as thermal treatment for zero liquid discharge (ZLD).
Unlike traditional wastewater treatment focused on discharge compliance, reuse systems must consistently produce high-quality water for specific industrial processes. This requires sophisticated monitoring, automation, and operator training beyond conventional systems. Industrial users committed to sustainability often want to use recycled water from municipal systems but struggle to identify where it’s available. Addressing this data gap could help unlock demand and signal opportunities for utilities.
The New Economics Of Water Security
The business case for industrial water reuse has fundamentally shifted. Companies once evaluated these systems against environmental goals or regulatory compliance costs. Today, they’re measuring them against operational risk and supply security — a calculation that increasingly favors reuse regardless of sustainability credentials.
Data centers are the starkest example. As AI computing demands explode, operators are increasingly confronting water availability as they develop new data centers. For example, Nevada’s deserts have become a major hub for data centers. In these cases, companies are deploying sophisticated reuse systems that treat water as a closed-loop resource rather than a consumable input are key. Amazon has taken this approach, expanding its use of recycled water from 20 data centers to 120.
Manufacturing needs to do the same. Companies expanding U.S. operations find that securing reliable, high-quality water requires more than traditional utility connections. In many markets, reuse systems provide supply certainty that utilities cannot guarantee.
Perhaps most significantly, the competitive dynamics around water access are shifting location decisions for a range of industries like semiconductor, car, and solar panel manufacturing. Companies evaluating site selection now factor water supply security alongside traditional considerations like transportation and workforce availability. Those implementing comprehensive reuse systems gain operational flexibility and make a necessary ecological transformation as water stress expands beyond traditionally arid regions.
Still, a primary obstacle to adopting water reuse involves the initial investment decision. Companies explore every alternative before committing to reuse infrastructure: deeper groundwater wells, alternative supply contracts, and demand reduction measures.
Policy momentum is building to address these barriers. In April, Representatives Darin LaHood (R-IL), Claudia Tenney (R-NY), Linda Sanchez (D-CA), and Brad Schneider (D-IL) introduced the bipartisan Advancing Water Reuse Act (H.R. 2940). The legislation would establish an investment tax credit for industrial water reuse projects, incentivizing industrial companies to make the investment that helps preserve precious water resources.
Water reuse systems are becoming as essential as power generation and waste treatment in modern facilities. In an economy where supply security increasingly determines operational success, comprehensive water management has evolved from an environmental initiative to a core business strategy.
[Note, for those of you with shining examples of industrial water reuse, please consider nominations to the Global Industrial Water Reuse Champions Award. The award recognizes Fortune 1000 companies that incorporate the best-in-class water recycling and reuse programs. Nominations accepted through August 15.]
Tom Iseman serves as the Vice President of Government Affairs for Veolia's water technology activities in North America. In this role, he is responsible for leading the company's global government affairs strategy and operations. He manages regulatory, legislative, political, and reputational risks while also seeking out growth opportunities within the water sector. Tom has over two decades of experience in water resource management, with particular expertise in drought and climate adaptation, water infrastructure, nature-based solutions, the energy-water nexus, and water markets. He earned a BA in history from Princeton University and an MS in freshwater ecosystems from the University of Michigan.
Brian Arntsen is the Global Domain Sales Leader for Veolia's water technology activities in North America. He holds a BS in Agricultural Engineering from UCA Buenos Aires, Argentina, as well as a postgraduate degree in Business Management from I.A.E Buenos Aires. In 2024, he was appointed WEF Community Leadership Council (CLC) Director. Additionally, he has been a member of the Wastewater Committee at the Water Environment Association of Ontario (WEAO) since 2022. Throughout his 40-year career, Brian has published over two dozen peer-review papers and has spoken at more than 30 conferences and symposiums.