Geophysical Approach Finds Leaks in Containment System Liners
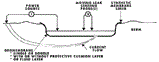
By Dr. Ian Bishop
Geomembrane liners manufactured from high density polyethylene (HDPE), polypropylene, polyvinyl chloride (PVC), and other synthetic materials are being used in numerous fluid and waste containment applications. These systems can develop undesirable leaks, which frequently are difficult to detect and locate. However, electrical techniques are being used successfully to locate leaks in these geomembrane liners. The international science and engineering consulting firm of Golder Associates has gained substantial experience with this technology and three of the firm's projects using the method are described later in this article.
Examples of containment systems using geomembrane liners are:
- Landfills
- Sewage/wastewater treatment ponds
- Tank farm containment berms
- Water transport canals
- Mine leach pads
- Roads and ditches in environmentally sensitive area such as tundra
- Snow containment bunds at airports
Geomembranes used in lining systems are robust, but prone to damage during and after installation. Some years ago, construction quality assurance (CQA) supervision by third parties was introduced and, as a result, there has been a significant reduction in the number of leaks. However, it is virtually impossible to eliminate all leaks and some fluid release through pinholes has always been assumed.
Holes in a geomembrane can be created by poor installation systems such as defective welding, especially as a result of inflections, material incompatibility, and traffic. Furthermore, there is documented evidence that liners in landfills have been punctured by contractor equipment during the installation of drainage layers and operational covers.
Additional failures can occur following completion of construction. For example, liner damage caused by people and animal traffic across the site, aeration equipment breaking loose in a storm, and rock or debris falls can all result in the development of leaks.
Such leaks in the liner create a potential for leachate contamination of the soil and groundwater beneath the liner. There is also the possibility, in the case of severe damage to the liner, that the structural integrity of the containment berm will be compromised.
Geophysicists on the staff of Golder Associates have been using an electrical leak location system to detect punctures and imperfections in geomembranes. Based in Redmond, Washington, in the U.S., and in Maidenhead, London, in the U.K., they have completed successfully two surveys in the US and three in the UK using the technique. The method is illustrated in Fig. 1.
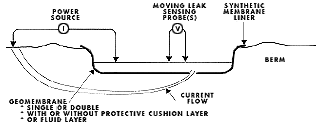
Fig. 1: General configuration of a leak location system
The leak location system is an electrical arrangement closely related to the direct-current electrical resistivity method. It can be used to detect leaks in single or double lining systems, used in fluid treatment ponds, or to locate leaks in liners beneath the drainage and protective cushion layers found in landfills. To locate the leaks, an electrical current is applied to the ground between two electrodes, one located in the pond and the other located outside in the earth around the pond. A second set of moving electrodes is used to measure the electric potential at closely spaced points throughout the area of concern.
If the geomembrane is intact, very little electrical current will flow through the highly resistive plastic liner. If a hole exists in the liner, there will be an increase in the electrical current flow through the point of leakage which will create an anomaly in the electric potential measurements.
Careful mapping of these changes in electric potential allows the team of geophysicists to locate holes ranging in size from less than a millimeter to very large splits in the liner. Generally, the minimum hole resolution is dependent upon the density of measuring points; the finer the measurement interval the smaller the hole that can be detected. The data are stored in the digital memory of the instrument used in the test and downloaded to a computer for processing. The results are displayed on a color contour map which shows the location of suspected leaks (Fig. 2).
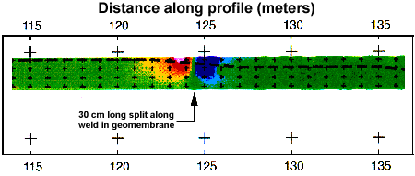
The above figure is an example of a typical leak anomaly, created by a 30 cm split in a seam.
Case Study # 1: Detecting Leaks in Vegetable Processing Plant's Storage Pond
Golder geophysicists successfully applied the technique in a leak location survey of a 10-acre storage pond at a vegetable processing plant. The pond was used to store wastewater during the winter when the ground is frozen and spray dispersion of excess waste water is not possible.
Leaks in an HDPE liner were suspected after three pieces of aeration equipment, normally tethered to steel cables extending across the pond, broke free from their moorings during a storm and came into contact with the HDPE geomembrane liner. The impacts of the aerators on the geomembrane created an unknown number of punctures below the water line. The breaches were allowing fluids to enter the berm, as evidenced by a steady stream of water flowing from a portion of the berm, thus threatening its structural integrity. One large hole was patched after a diver found a tear and a washout behind the geomembrane liner. However, after the pond was refilled, the berm continued to leak, indicating that one or more holes were still allowing fluid to escape. When the company was threatened with plant shutdown if the storage pond couldn't be used, Golder was asked to assist in locating other leaks.
The consultant's team performed a methodical, high-resolution leak location survey over the corner of the pond where the equipment had come to rest. The survey collected data from the waterline to a depth of 15 m down-slope, using a 0.5 m control grid. Gathered data were monitored for any indications of anomalous readings that could signify a leak. Locations of suspected leaks were marked on the liner for reference. After processing the data in the field, the locations of three anomalies were identified and the successful repair of the hole initially identified was confirmed.
The first of three anomalies now identified was at a fresh breach discovered the night before the geophysical survey. A second anomaly, located at a depth of 0.25 m below the water line, was caused by a puncture hole produced when the mooring arm of one of the stray aerators collided with the liner. The third anomaly was more unusual in that it was much broader in shape with an apparent depth below water line of 3.5 m.
This last anomaly had been caused by electrical grounding through the power cable still attached to a run-away aerator floating approximately 3.5 m from the bank. Examination of the aerator discovered that it was still connected to ground, through its power cable, at the time of the survey despite its trek across the pond. This anomaly highlights one of the requirements for the successful use of the technique. All possible electrical short circuits such as pipe work, steel mooring cables and power cables should be isolated.
A puncture also was located visually in the liner above the waterline, probably caused by traffic during the emergency.
Case Study # 2: Increased Cyanide Levels Detected Due to Leaks in Liner
Cyanide was discovered in the leak detection system beneath the geomembrane liner of a gold mine tailings pond, following an increase in the depth of water level above a welded seam in the liner. A number of splits in the seam, as well as a few bullet holes, were found during visual inspection of this seam lying above the water line. This raised concern over the condition of 1500 m of the seam lying below the water line, which could not be examined by conventional methods. The mining company asked our geophysicists to conduct a geophysical survey to locate any leaks in the liner and, particularly, to evaluate the presence of possible failures in the suspect welded seam.
The leak location survey was conducted around the perimeter of the pond to maximum depths of 5 meters below the suspect seam. Four holes were located beneath the water line with the leak location system. All were either on the suspect seam or on adjacent patches. They ranged in size from a pinhole to a 30 cm long split with voids beneath the liner. In addition, five punctures were visually located in the liner above the water line. These punctures apparently were caused by stones or rocks and deer hooves. All the detected holes in the liner were marked and labeled for future repair.
Case Study # 3: Landfill with a Protective Gravel Blanket Over a Geomembrane
A more conventional survey of a landfill covered the base of a cell, the berms to the west, east and north of the cell and an inter-panel berm to the south. In this example, the geomembrane was covered by a protective cushion of gravel. The survey found three small anomalies, the first of which, when excavated, proved to be a pinhole in the middle of a panel, while the other two were both pinholes at a weld in the seam at the intersection of 3 panels.
With the increased awareness of how commonplace leaks in geomembrane liners have become (by some U.S. statistics, measured at an average of 14 leaks per 10,000m2 on soil covered liners), and the strict regulations governing the protection of groundwater now in place in the United States and abroad, the use of leak detection surveys based on the technique described above to evaluate liners in landfill and detention pond environments is expected to increase.
About the Author: Ian Bishop, Ph.D., is an associate and senior geophysicist on the staff of Golder Associates in the firm's Maidenhead, United Kingdom office. He is responsible for the technical direction of geophysical projects and new market development, and can be reached at: Tel. +44 1628 771731; Fax. +44 1628 770699; email. ibishop@golder.com for more information about leak location or other geophysical services.
Golder Associates (UK) Ltd. is the British affiliate of Golder Associates Corporation, an international group of science and engineering consulting companies. Founded in 1960, the firm now has more than 1,800 employees in 75 offices worldwide and has completed project assignments in over 130 countries.
Edited by Ian Lisk